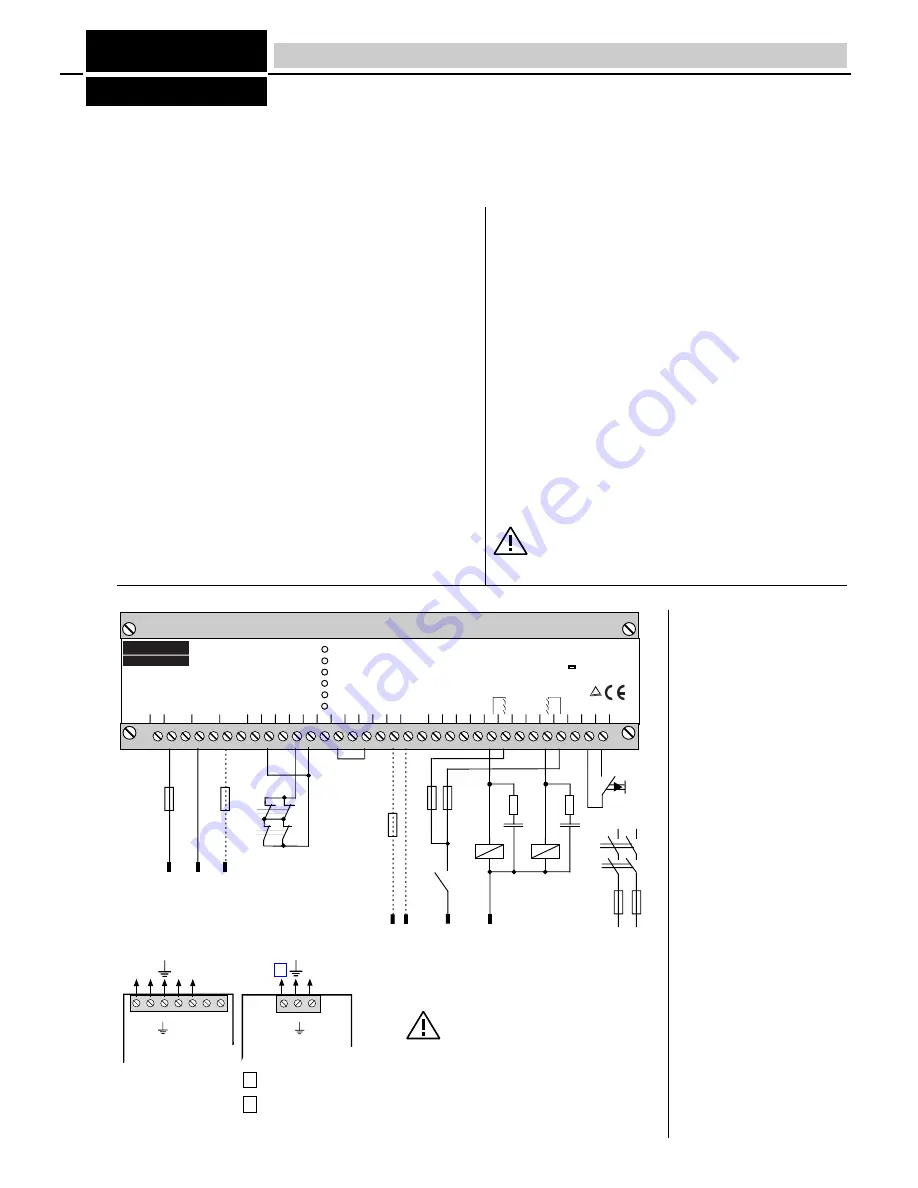
7.2.4 Safety mode with restart interlock during the hazardous movement "B1"
e.g. For applications with manual cyclic penetrations of the protective field during a non-hazardous movement or machine
standstill.
Connection diagram for operating mode "B1"
FIESSLER
E L E K T R O N I K
27
Functional example
Having switched on the safety facility, the protective field must
be penetrated in order to carry out a startup test. Having
subsequently pressed the start button with the protective field
free, the output contacts 16-17 and 20-21 close and the
machine movement is started.
If the protective field of the light barrier is penetrated during
the hazardous movement, the contacts 16-17 and 20-21 are
opened and the machine stopped.
The checking path 6-7 is used to perform an additional check
of the hydraulic valves or the contactor. The activation of a new
operating stroke or a hazardous movement will only be
performed if both or valves K1 and K2 had fallen when the
protective field, and the protective field is subsequently free
again.
During the idling status of the operating materials, or during a
non-hazardous opening movement (opened switch "S"), its is
possible to access the operating materials at any time without
having to press the start button.
When activating the closing movement via contactors K1 and
K2, the respective make contacts of K1 and K2 must be
switched in series!
In this operating mode, it must be ensured that it
is not possible to walk behind the light barrier!
(Refer to Section 4.4)
1
2
3
1
2
3
4
5
6
7
12
12
13
15
14
4
3
6
-
7
+
2
3
+
2
1
5
1
-
OSSD2
OSSD1
EDM
Start
6
FIESSLER
E L E K T R O N I K
Schaltgerät BWS Typ 4
Switching unit ESPE Type 4
Boîtier de commande ESPS Type 4
Nr./Baujahr
Ansprechzeit
Temp.
Schutzart
Versorgung
Kontaktbel.
Kastellstr.9 73734 Esslingen
Tel. 0711/ 91 96 97-0
Achtung
Vor Abziehen der Klemmleiste Netzspannung abschalten!
Attention
Turn off the supply voltage !
Attention
Couper l'alimentation !
A
1
2
3
7
4
5
8
10
9
17
B
C
12
13 14 15
16
LSUW NSR 3-1 K
No./year of construction
response time
t
emp.
enclosure rating
supply voltage
contact max
No./année de fabrication
temps de réponse
temp.
degré de protection
tension d'alimentation
charge contact maxi.
.................................
30 mS
-10… + 55 °C
IP 20
24VDC/115VAC/230VAC
-15% +10 %, 50Hz
2 A, 250 VAC
18
Netz
tension
power
LS Frei
BS libre
LC free
output interupted
sortie interrompue
Ausgang unterbrochen
output free
sortie libre
Ausgang frei
interdiction de redémarrage
restart interlock
Wiederanlaufsperre
19 20 21
22
LS unterbrochen
BS interrompue
LC interrupted
D
Made in Germany
11
TÜV Rheinland
AA
AA
AA
TÜV Rheinland
N
L1 230 VAC
L1 115 VAC
0 V DC
+24VDC
k1
k2
X
X
X
X
M 2,0 A
K1
K2
M 2,0 A
k1
k2
M 2,0 A
M 2,0 A
M 2,0 A
S
X
7 Additional functions with safety switchgears
- "B1"
LSUW NSR 3-1 K switchgear
Cable routing:
- Separately from power lines.
- The cable routing for the contactor
check (terminals 6 & 7) must prevent
short-circuiting of wires.
- On terminals 4, 5, 8, 9, the max. cable
length is limited to <= 1m.
The hazardous movement must
only be activated via output
contacts 16-17 and 20-21.
The output contacts are
potential-free, monitored, guided
make contacts are must be
loaded with max. 2 A/250 VAC
or 60 VDC, 30 W. With inductive
load, the load (not the contacts)
is to be switched at the same
time as the spark arresting
sections (e.g. 0.22 uF, 220
Ω
.
Optional power supply:
The contact 18 - 19 serves as an
alarm path and is not permitted
to activate the hazardous closing
movement.
To increase the switching
reliability, collateral contacts
should be used on terminals 5,
6, 7, 8, 9, 10, 11, D and 22. No
external potential must be
connected to these terminals.
When performing electric
welding work on the machine,
the terminal strip of the
switchgear is to be removed,
otherwise the vagrant welding
currents may cause destruction
of the installed electronics.
Start button
0V
24V DC
L1
N
L1
BA - ULVT
Optional power supply:
Terminal 1 & 2: 230 VAC -15% + 10%
or
Terminal 1 & 3: 115 VAC -15% + 10%
or
Terminal A & 12: 24 VDC -10% + 20%
ULVTS Transmitter
ULVTE Receiver
Set operating mode:
Without contactor check
Without restart interlock
(both functions are
performed by switchgear)
antivalent outputs
Voltage depending on type of contactor
L1 = 230 V AC
or 24 V DC
Contactor
monitoring
X = For interruption
of hazardous
movement
Spark arresting
sections
N
or
0V
Fuses to be sized so
that contact
touching is
prevented reliably!
X
X
For 230 V AC and 115 V AC :
terminal 3
For 24 V DC :
terminal C
Содержание ESPE Type 4
Страница 4: ...4 FIESSLER E L E K T R O N I K BA ULVT ...
Страница 39: ...FIESSLER E L E K T R O N I K 39 BA ULVT ...