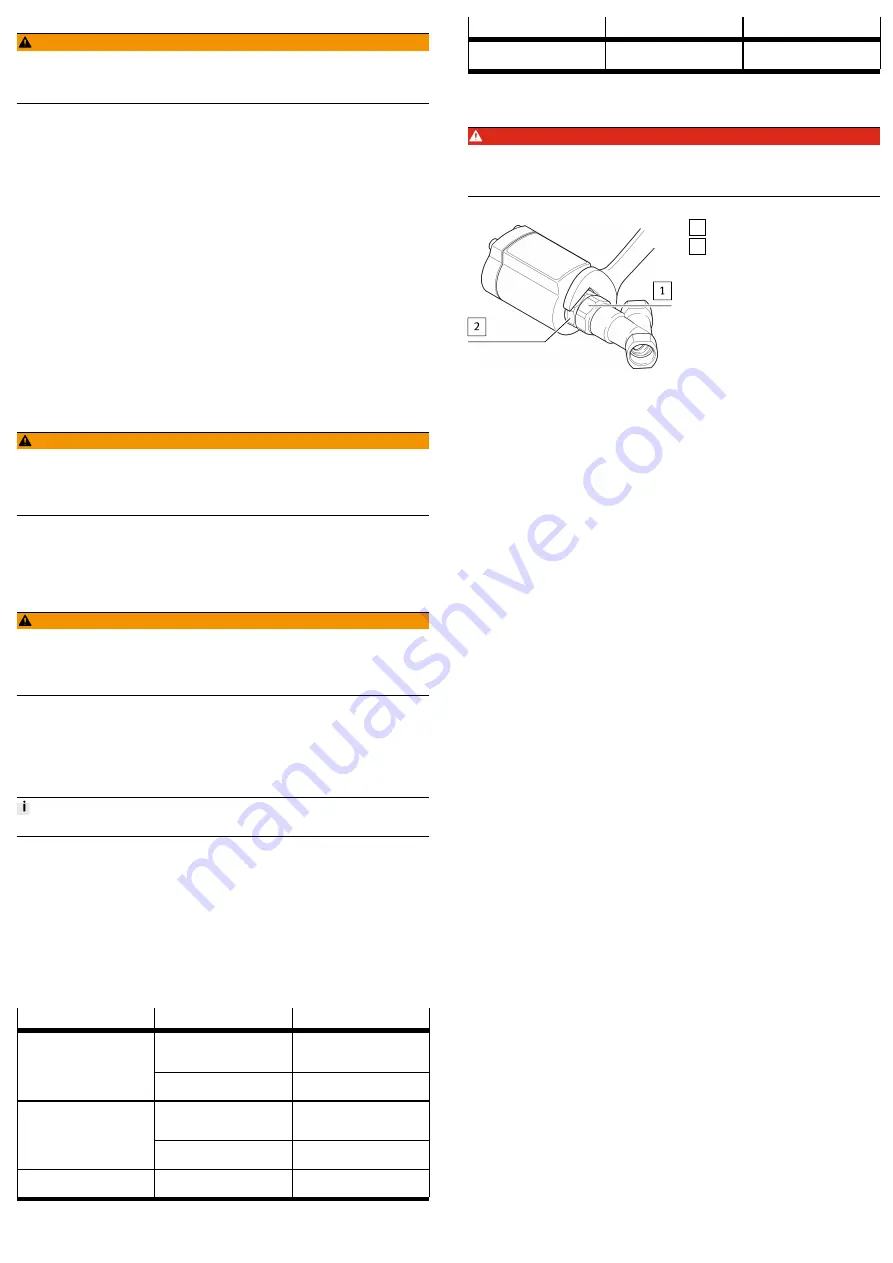
9
Commissioning
WARNING!
Risk of injury from manipulation in the operating area of the angle seat valve.
Limbs can be cut or severed.
•
Operate the angle seat valve only if it is fully mounted.
Requirements
–
The valve is fully mounted and connected.
Checking operating conditions
1. Check operating conditions and limit values
è
2. Check connection points for tightness.
3. Check compatibility of the devices in the system for maximum pressure (con-
sider pressure peaks). If necessary, adjust the application parameters.
Commissioning the valve with single-acting drives
1. Supply medium.
2. Slowly apply operating pressure to the valve. The operating pressure required
for reliable switching of the valve depends on the medium pressure
è
16.2 Technical data, pneumatic.
3. Function and direction control of the individual pneumatic drives.
Commissioning the valve with double-acting drives
1. Slowly apply operating pressure to the valve. The operating pressure required
for reliable switching of the valve depends on the medium pressure
è
16.2 Technical data, pneumatic.
2. Supply medium.
3. Function and direction control of the individual pneumatic drives.
10
Operation
WARNING!
Risk of injury from touching hot surfaces.
Valve housing and actuator can become hot at high temperature of medium.
Severe burns are possible.
•
Do not touch the angle seat valve during operation or immediately afterward.
•
Comply with operating conditions.
•
Comply with maintenance conditions
è
After longer idle times:
•
Actuate the valve several times and check for correct function.
11
General
WARNING!
Risk of injury from touching hot surfaces.
Valve housing and actuator can become hot at high temperature of medium.
Severe burns are possible.
•
Allow the angle seat valve to cool off before working on it.
•
Check product regularly from the outside for leakage and function.
•
Check function of the product regularly.
•
Clean product regularly with commercial cleaning agents.
11.1
Proof test Proof Test)
The proof test (Proof Test) consists of shutting the operating pressure off and on.
•
Run the proof test once a year.
During the proof test, the safety of the application must be ensured.
1. Shut off operating pressure.
2. Check valve position.
Ä
The test is successful if the safe state is reached within the specified
time. For assessment of the safe state
è
3. Slowly apply operating pressure to the valve.
Ä
The test will be successful if the valve returns to its original position.
4. Check the valve externally (visual inspection).
Ä
The test is successful if no defect or leakage is detected.
5. Document test results.
12
Malfunctions
Fault description
Cause
Remedy
VZXA-B: media pressure is too
high or operating pressure too
low.
Set required differential pres-
sure or adjust operating pres-
sure
è
Valve does not close or closes
too slowly.
Medium contains too many or
too large contaminants.
Comply with operating condi-
tions.
VZXA-A: operating pressure is
too low or media pressure is
too high.
Adjust operating pressure or
media pressure.
Valve does not open or opens
too slowly.
VZXA-B: operating pressure is
too low.
Adjust operating pressure.
Medium leaks out of leakage
hole.
Seal cartridge is defective.
Replace seal cartridge
è
Spare
parts documentation.
Fault description
Cause
Remedy
Medium cannot be shut off.
Seat seal is defective.
Replace seat seal
è
Spare
parts documentation.
Tab. 7
13
Modification
DANGER!
Risk of injury from flying objects.
Unsecured parts under pressure can fly around and injure people.
•
Before replacing wearing parts, depressurise the valve and piping.
1 Spanner flat for counter holding
2 Interface screw SW46
Fig. 2 Demounting actuator
13.1
Removing actuator from the valve housing – in installed position
The actuator can be removed from the valve housing without having to remove
the valve from the piping.
1. Depressurise the piping and allow valve to cool to room temperature.
2. Secure the actuator with suitable equipment to prevent it from falling or slip-
ping.
3. Extend the actuator stem.
–
With double-acting valves: pressurise port (4) (3 bar).
–
With valves with NO control function: pressurise connection (2) (3 bar).
–
For valves with NC control function: exhaust the actuator.
4. Loosen interface screw
5. Remove actuator from the valve housing.
6. Shut off operating pressure.
13.2
Removing actuator from the valve housing – in removed position
1. Extend the actuator stem.
–
With double-acting valves: pressurise port (4) (3 bar).
–
With valves with NO control function: pressurise connection (2) (3 bar).
–
For valves with NC control function: exhaust the actuator.
2. Loosen interface screw
3. Remove actuator from the valve housing.
4. Shut off operating pressure.
13.3
Mounting actuator on the valve housing
1. Extend the actuator stem.
–
With double-acting valves: pressurise connection (4) slowly (3 bar).
–
For valves with NO control function: pressurise connection (2) slowly
(3 bar).
–
For valves with NC control function: exhaust the actuator.
2. Push valve body spindle completely into the valve body.
3. Place actuator on valve housing.
4. Tighten interface screw
.
–
Tightening torque: 50 Nm
5. Shut off operating pressure.
13.4
Turning actuator
1. Loosen interface screw
½
turn).
2. Rotate actuator to desired position.
3. Tighten interface screw
.
–
Tightening torque: 50 Nm