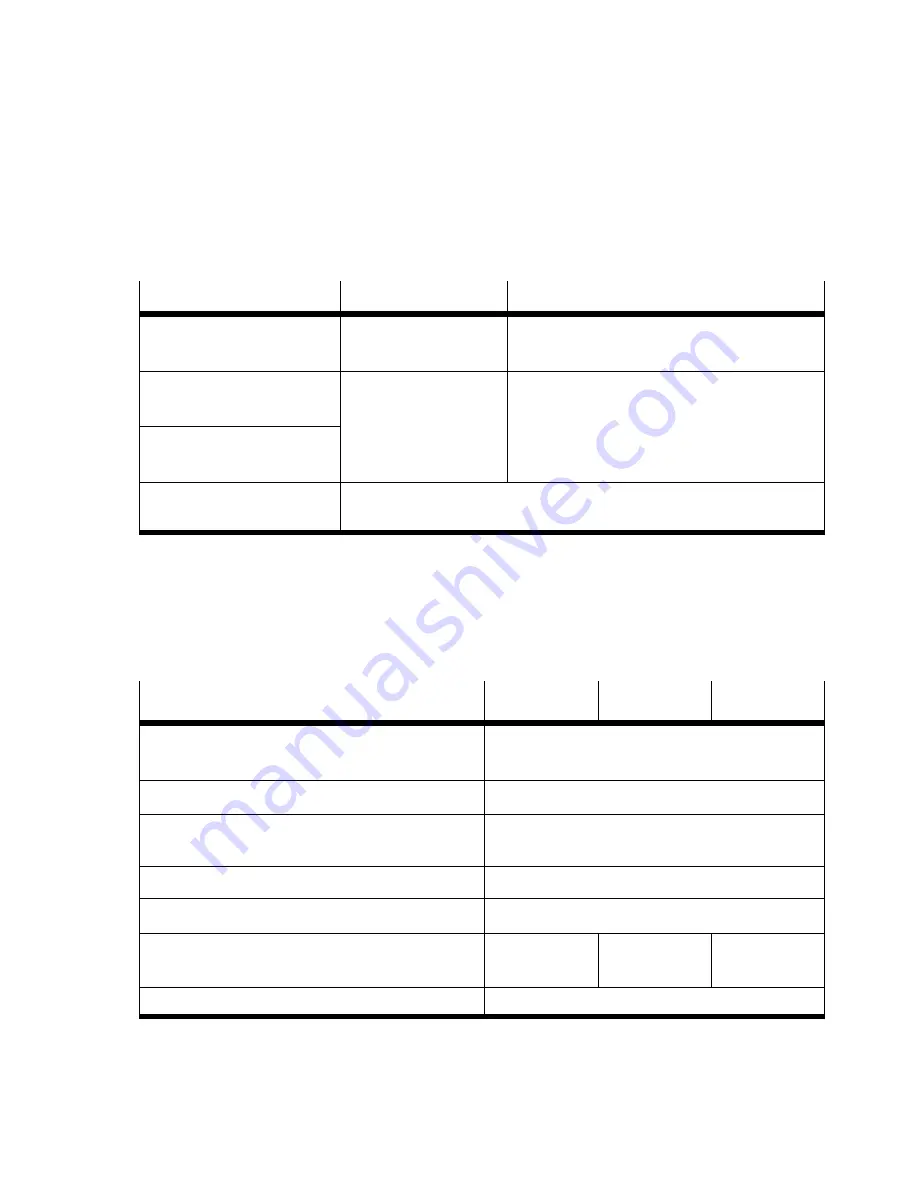
DSMI-B
Festo DSMI-B 2017-12d English
21
11
Troubleshooting
Fault
Possible cause
Remedy
Uneven movement of the
moving mass
Asymmetric angle
setting
Symmetric setting preferred
Hard metal impact at the
end position
Residual energy too
high
– Select lower swivel speed;
– Use internal or external shock absorbers;
– Move only against residual air cushion on
the exhaust side;
– Select a small mass.
Drive shaft does not
remain in the end position
In combination with
positioning controllers
See detailed description of the relevant positioning controller
Fig. 30
12
Technical data
DSMI-...-B
25
40
63
Design
Semi-rotary vane drive with drive shaft on ball
bearings and integrated displacement encoder
Mode of operation
Double-acting
Operating medium
1)
Filtered and unlubricated compressed air
(filter fineness: 5 μm)
Assembly position
2)
As desired
Max. swivel angle
[°]
272
Pneumatic connection
M5 (with
QSM-M5-6)
G
Á
(with
QS-1/8-8)
G¼ (with
QS-1/4-8-I)
Operating pressure
1)
[bar]
4 ... 8
1)
Applies only to applications with positioning controller
2)
Please observe the additional data in the descriptions of the positioning controller