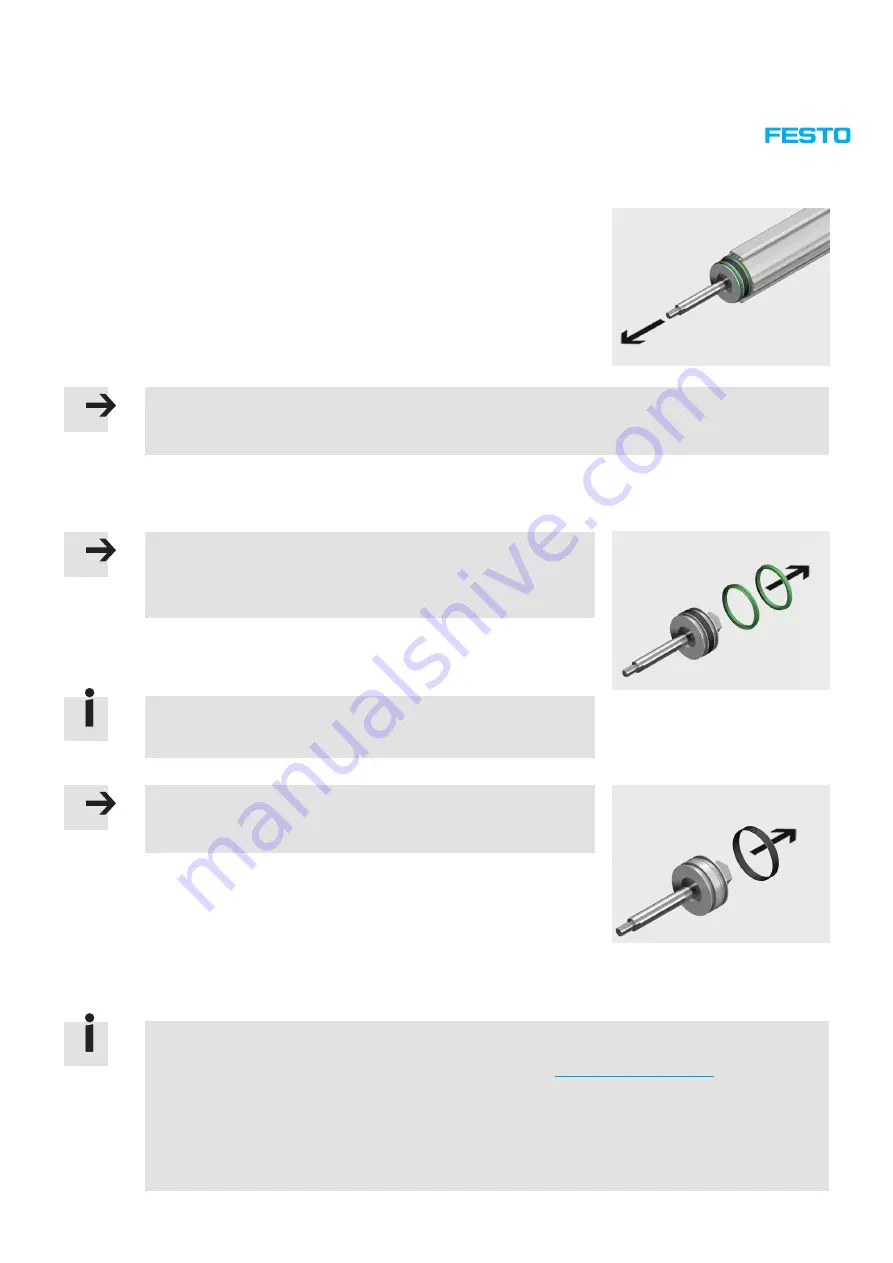
27 / 55
Festo 7DFPIb_en
4.4
Repair steps for the piston
1. Carefully pull the piston rod out of the cylinder barrel.
2. Inspect the cylinder barrel and piston rod for damage.
Note
If the cylinder barrel is showing signs of significant damage (especially scoring on the bearing surface), the seals of
the piston can no longer provide a clean seal and the entire linear actuator must be replaced.
4.4.1
Replacing the piston components
Note
The lip rings must not, under any circumstances, be levered out of the
groove using a sharp-edged object as this can damage them. Use a flat,
blunt object.
1. Carefully remove the lip rings from the seats in the piston.
2. Inspect the lip rings for damage.
Scores in the lip seals cause leaks between the lip ring and the cylinder
barrel bearing surface. Damage to the sliding seal has a negative effect on
the sliding characteristics of the piston.
Note
Do not, under any circumstances, bend the sliding ring open too far, as this
can damage it.
3.
Slightly
open the sliding ring at the transverse groove and remove from the
piston in the direction of the axis.
4.4.2
Replacing the magnet holder
If the magnetic driver (magnet) of the displacement encoder is damaged, together with the corresponding holder or
the displacement encoder (linear potentiometer) that is still in the cylinder barrel, these can only be replaced using a
spare parts kit. Further information can be found on the Festo website (
).
In this case, the magnet holder must be removed from the piston rod.
The spare parts kit contains:
– The magnet
– The magnet holder with O-ring and retaining ring
– The magnet rod with cable connector, all electrical cables and the plug