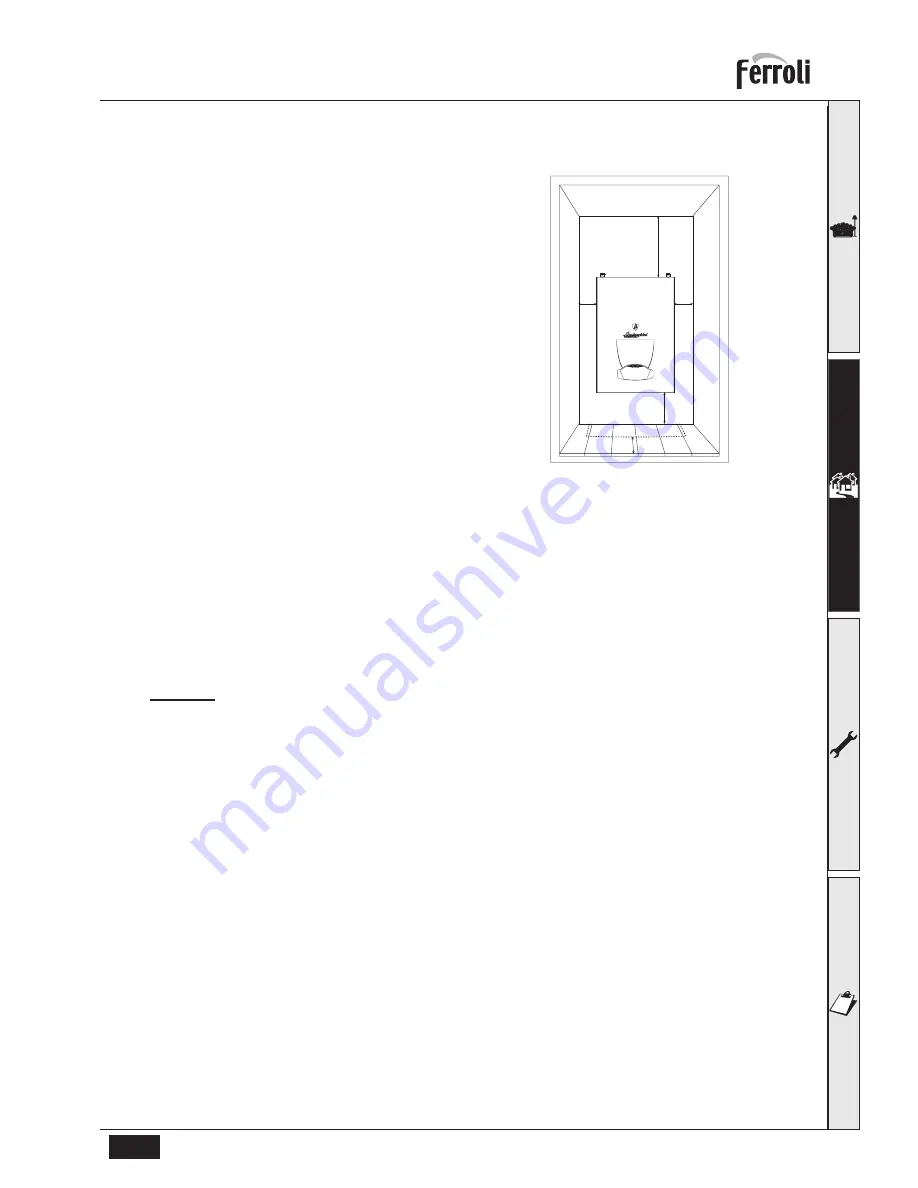
EXTREMA
11
EN
cod. 3540S060 - 04/2010 (Rev. 00)
2.2 Place of installation
The combustion circuit is sealed with respect to the
place of installation and therefore the unit can be in-
stalled in any room. However, the place of installation
must be sufficiently ventilated to prevent the creation
of dangerous conditions in case of even slight gas
leaks. This safety regulation is provided for by EEC Di-
rective no. 90/396 for all gas units, including those with
a sealed chamber.
The unit is suitable for operation in a partially protect-
ed place in conformity with EN 297 pr A6, with mini-
mum temperature -5°C. It is advisable to install the
boiler under the slope of a roof, inside a balcony or in
a sheltered recess.
In any case, the place of installation must be free of
dust, flammable materials or objects or corrosive gas-
es.
The boiler is arranged for wall mounting and comes
standard with a hanging bracket. A paper template for
marking the drilling points on the wall is provided in the
box. The wall fixing must ensure stable and effective
support for the generator.
A
If the unit is enclosed in a cabinet or mounted
alongside, a space must be provided for re-
moving the casing and for normal mainte-
nance operations. The minimum
measurements to be respected are given in
fig. 17.
fig. 17 - Minimum distances around the boiler
A
Min. 1 cm
B
Min. 15 cm
C
Min. 30 cm
D
Min. 32 cm (via an openable panel)
2.3 Plumbing connections
Important
The heating capacity of the boiler must be previously established by calculating the building's heat requirement accord-
ing to the current regulations. To ensure proper operation and long boiler life, the plumbing system must be adequately
sized and complete with all the necessary accessories, including a room thermostat, a termostatic radiator valve (TRV),
etc. The system flow and return pipes must have a diameter of at least 22 mm for the first 3 m of length from the unit.
If the system delivery and return pipes follow a path where air pockets could form in certain places, it is advisable to
install vent valves at these points. Also, install type "A" drain cocks at the lowest points in the system to allow complete
emptying.
The temperature drop between the delivery manifold and the return to the boiler should not exceed 20 °C.
A flow rate of at least 6 litres/min through the heat exchanger is required. An automatic bypass installed in the boiler
guarantees maintaining of the required flow rate.
B
Do not use the water system pipes to earth electrical appliances.
Before installation, carefully wash all the heating system pipes to remove any residuals or impurities that could affect
proper operation of the unit (as required by BS 7593 Building regs Doc L).
Carry out the connections to the unit as indicated in fig. 36.
B
The safety valve discharge must be connected to a 15 mm diameter copper pipe descending from the boiler
to run off system water in case of overpressure in the heating circuit. Otherwise, if the discharge valve cuts in
and floods the room, the boiler manufacturer cannot be held liable. The discharge must be run to the outside
of the building to prevent the risk of damage or injury caused by discharged hot water in case of overpressure
in the system.
D
A
A
B
C