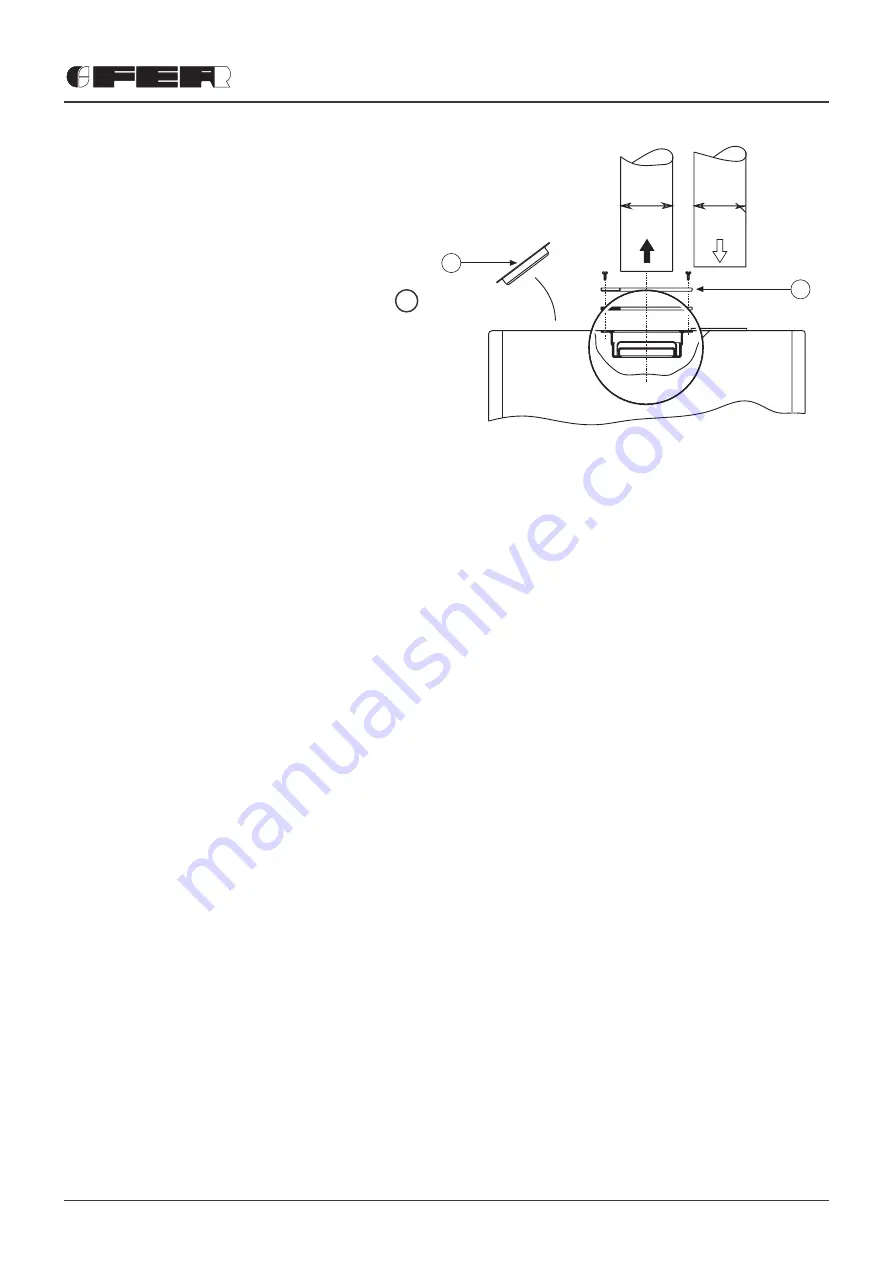
FALCON II
16
Fig. 18
Ø80
Ø80
AIR
FLUE
1
2
3.04 Top Outlet: Two Pipe Flue System
3.04.1 Two pipe connection
Two separate ducts Ø80 for air intake and flue gas
discharge can be directly connected to the boiler.
mount the separate outlet kit "1".
Insert blanking plate 2
in remaining air intake
Connect flue duct to central hole Ø80 and air duct to
left or right air intake hole Ø80. Insert blanking plate
"2" in remaining air intake.
A varied selection of accessories for two pipe systems are available from FER (ref. to page 17). Before
installing your system please check via calculation table at 3.04.2 you are not exceeding the maximum
permissible length for the appliance.
IMPORTANT:
Notes on two pipe system installation:
When using the two pipe system the flue discharge pipe must have a 25mm air gap when passing through combustible
materials. Where the flue discharge pipe passes through the airing space of an airing cupboard it must be protected
by a non combustible guard or expanded metal giving an annular air gap of at least 25mm.
Where the flue discharge pipe passes through a wall containing cavity insulation, a non combustible sleeve must
be fitted. Additionally a gap of 25mm between the sleeve and the insulation should be provided by cutting
back the insulation or packing loose fill bead insulation with mineral fibre. Where the flue pipe is run
through an unheated roof space it should be insulated with non combustible insulating material to prevent
condensation. The flue pipe should be supported at intervals of not more than 1.8m and the support
should be preferably below a joint.
3.04.2 Two pipe fl ue system
To determine the maximum length of fl ue and air pipe permissible.
The calculation is based on a standard reference resistance of 1 metre of 80 mm horizontal air intake pipe. For
every configuration of the two-pipe system all components will have a resistance factor based upon this reference.
(I.e. a 90 degree bend fitted in the flue line would attract a resistance factor equivalent to 2.5 Metres of horizontal
80mm pipe). This is expressed as
X
metres. Each boiler will have a maximum equivalent length of flue/air pipe and
this is shown in the table as
N
metres. Therefore when calculating the proposed flue run the equivalent resistance
of every length of pipe and every bend, whether air intake or flue discharge is added together to give an actual
total flue length. The final figure calculated must not exceed the permitted maximum length (N metres) for each
boiler type.
Calculation Routine
1. Identify all the components needed to complete the proposed flue/air pipe run.
2. Calculate the sum of all the equivalent lengths (see table at next page).
3. For boilers, which may require a flue restrictor, refer to table at page 13 (par. 3.02) to ascertain the correct
size and add this resistance to your total.
4. Check and verify that the total flue/air pipe length (flow resistance) does not exceed 50 mt. maximum
permitted for
Falcon II
.
IMPORTANT: Resistance factors apply to standard férroli components only.