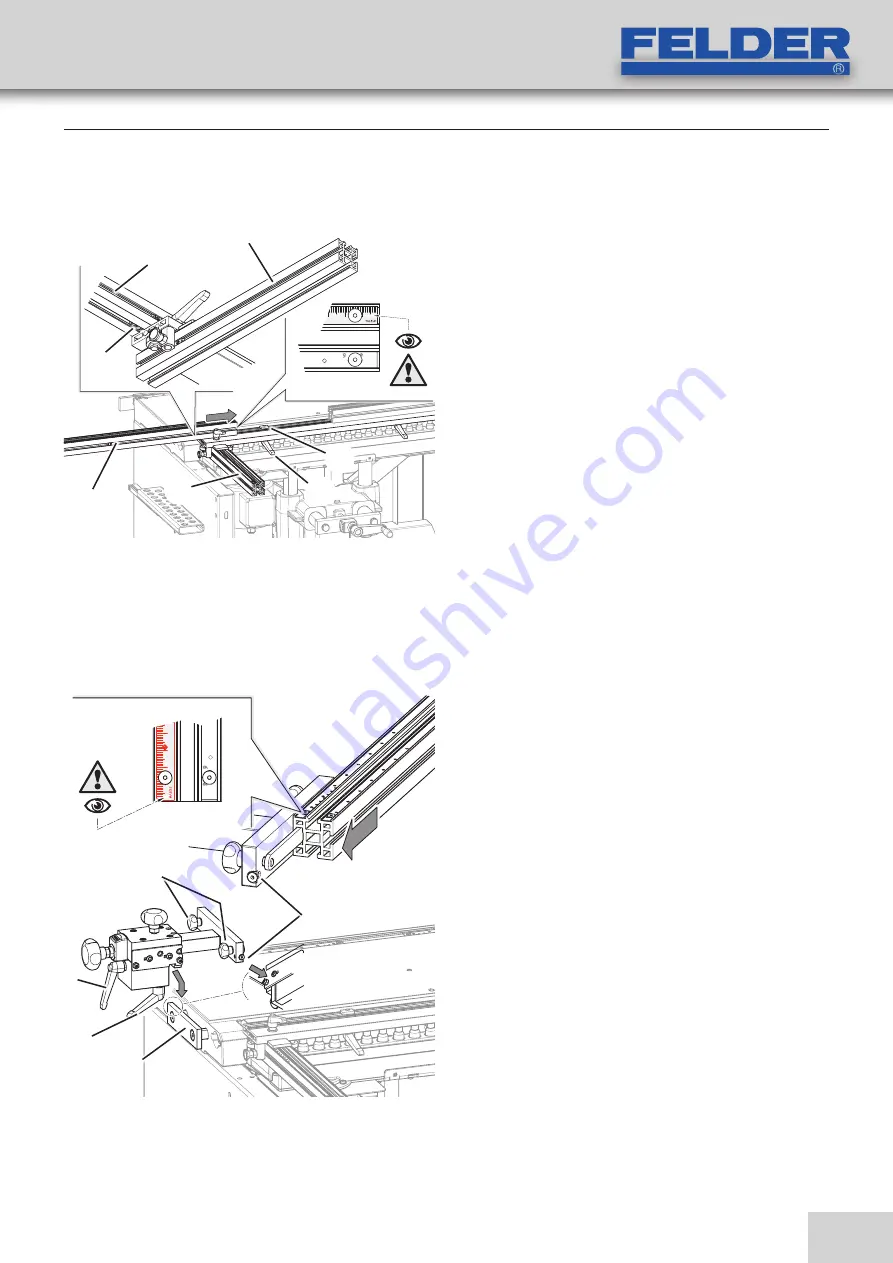
23
1, 2, 3...
5432
1
"
!
#
&
$
... 3, 2, 1
4
3
2
1
$
$
%
%
!
"
#
Multi Boring Machine
FD 21 professional
1.
Assembly of the coupler system:
See individual assembly instructions
2.
Thread the side stop into the machine table.
is pulled fully to the front (up to stop)
3.
Secure clamping levers 1 and 2.
4.
Loosen the thumb screws.
5.
Mount lateral stop extension fence onto the lateral
clamps
6.
Stop extension:
is pulled fully to the front (up to stop)
7.
Tighten the thumb screws.
!"
Single-hand clamping lever
#
coupling system
$
Thumb screws
%
Stop extension
&
Fence screw
Position the vertical borer
See chapter entitled
>Making adjustments and preparations< / > Drill unit
tilt<
1.
Release the clamping lever.
2.
Mount lateral stop extension fence onto the lateral
clamps
3.
Stop extension:
is pulled fully to the front (up to stop)
4.
Tighten the clamping lever
5.
The second stop extension should be mounted on the
opposite side in the same way
!
Single-hand clamping lever
"
U-clamp
#
Fence screw
$
Stop extension
%
Depth stop profile
5.4.5 Lateral stops digital
Fig. 5-7: Assembly instructions
5.4.4 Mounting the extension as depth stop
Fig. 5-6: Stop extension
Setup and installation