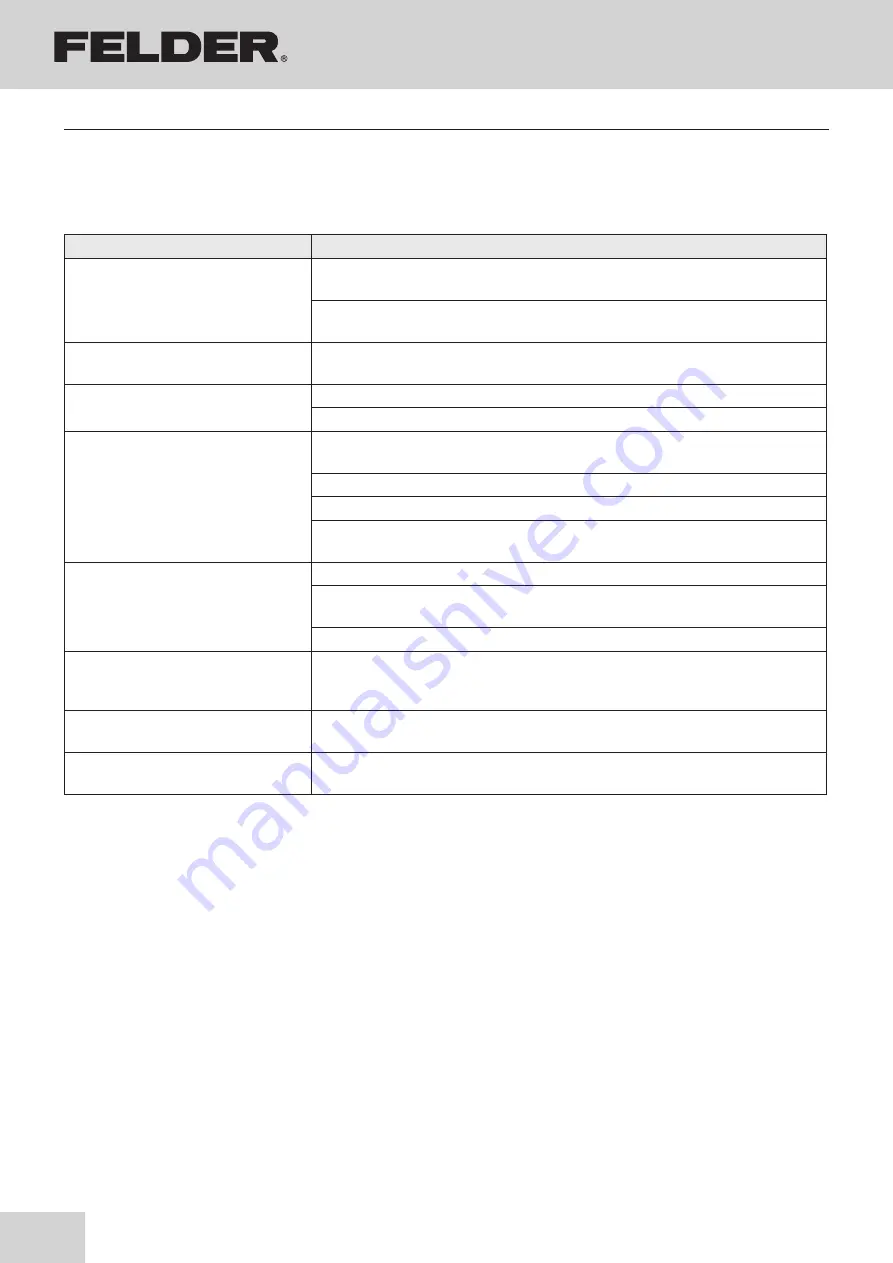
34
Bandsaw
FB 510/610/710 & FB 710 c-tech
9.4 Faults, causes and repairs
Faults
Fault
Cause and problem elimination
Machine does not start
Safety break switches are breaking the electric circuit
Ensure that the side doors are closed properly
Emergency stop switch engaged (FB 710 c-tech)
Unlock the emergency stop switch
Squeaking noises when starting up
Insufficient tension (Drive belt)
Retensioning the drive belt
The cuts are not straight
Check sharpness and set of saw blade
Check the guide fence alignment
The saw blade is torn at the base of
the individual teeth
Incorrect sharpness and constant overheating, or otherwise incorrect set of
saw blade
Width of saw blade is too thick in relation to the diameter of the wheel
Defect or soiled wheel running surfaces
Incorrectly aligned wheels
✆
Felder
The saw blade is rupturing on the
rear side
Feed rate or pressure is too high during cutting
Poor welded joint
Saw blade replacement
The rear support roller of the saw blade guide is defective
The machine comes to a stillstand
with the saw belt locked into the
workpiece
Stop the motor and loosen the the brake. Enlarge the cutting gap with a
wedge and remove the workpiece. Prior to switching the machine on again,
check the condition of the saw belt and its position on the wheels
The saw belt is straying forwards
and backwards
The belt is not aligned with the welded joints
Saw blade replacement
The saw blade is slipping to the
back at the beginning of the cut
The saw blade is not sharp enough or is unsuitable for the type of material to
be cut, or the surface of the wheel is defective