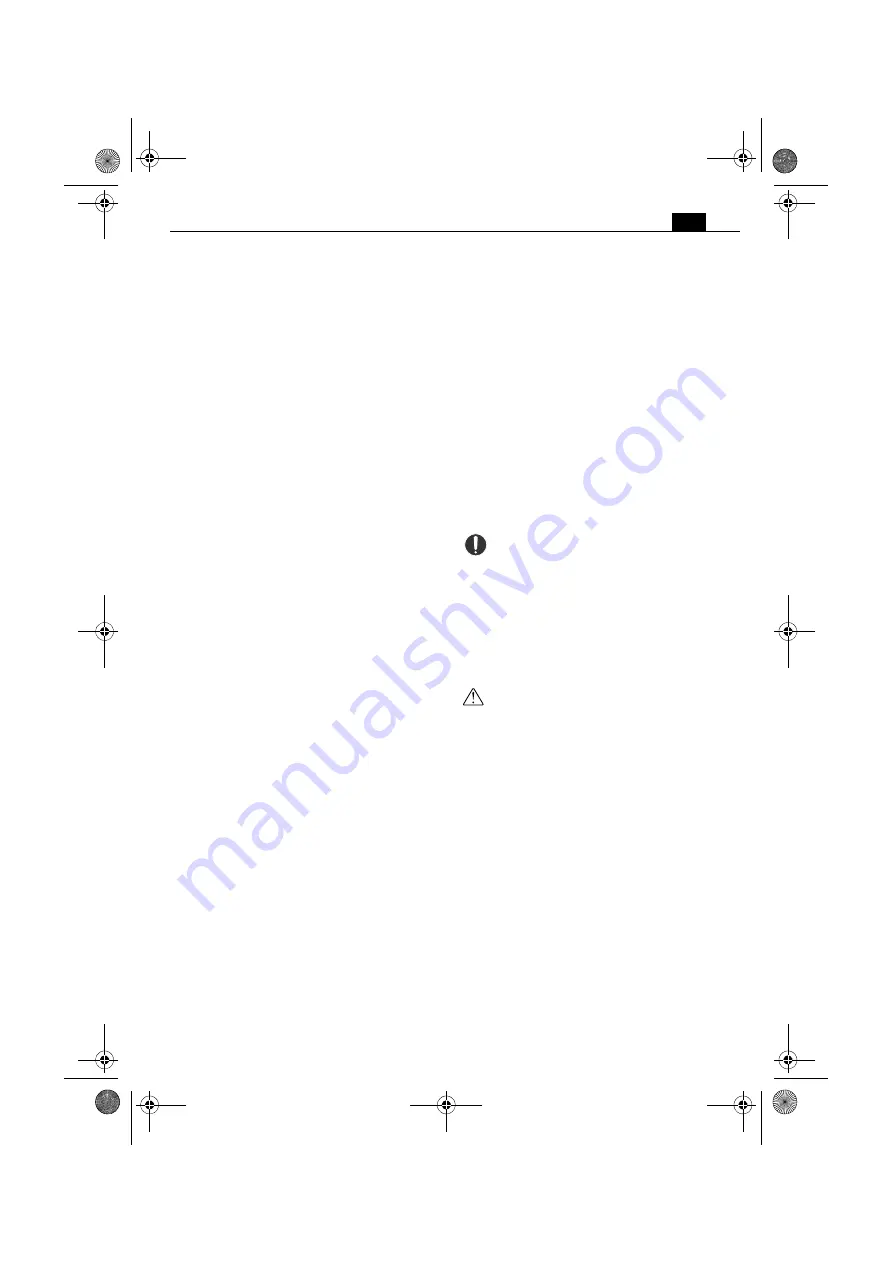
13
en
Check the rotation direction of the motor before starting
the operation of the machine for the first time.
If the rota-
tion direction of the motor is incorrect, the workpiece
can be thrown from the machine and cause an accident.
The rotation direction may be changed only by a quali-
fiedelectrician.
Make sure that you or other persons are not standing
directly next to the grinding belt when switching the
machine on.
The grinding belt can tear apart and cause
serious injuries.
Handling hazardous dusts
For work procedures with this power tool where mate-
rial is removed, dusts develop that can be hazardous to
one’s health.
Contact with or inhaling some dust types, e. g. asbestos
and asbestos-containing materials, lead-containing coat-
ings, metal, some wood types, minerals, silicate particles
from materials containing stone, paint solvents, wood
preservatives, antifouling paints for vessels, can trigger
allergic reactions to the operator or bystanders and/or
lead to respiratory infections, cancer, birth defects or
other reproductive harm. The risk from inhaling dusts
depends on the exposition. Use dust extraction matched
appropriately for the developing dust, as well as personal
protective equipment and provide for good ventilation of
the workplace. Leave the processing of asbestos-contain-
ing materials to specialists.
Wood and light-metal dust, hot mixtures of grinding dust
and chemical materials can self-ignite under unfavourable
conditions or cause an explosion. Avoid sparking in the
direction of the dust collector as well as overheating of
the power tool and the materials being sanded, empty the
dust collector/container in time, observe the material
manufacturer’s working instructions, as well as the rele-
vant regulations in your country for the materials being
worked.
At a glance.
1
Safety cover, top
2
Star-knob bolt, safety cover
3
Screws for adjustment of the gap clearance
4
Stop
5
Spark guard
6
Wing bolts of the spark guard
7
Grinding rest
8
Dust collector
9
Hose connection socket for dust extraction
10
Screw for chip/grinding-dust box
11
Star-knob bolt for grinding rest
12
Adjustment screw of support surface for plane grind-
ing
13
Clamping lever
14
Screws for coarse adjustment of the belt tension
15
Safety pushbutton
16
Plug
17
Star-knob bolt for adjusting the tracking of the grind-
ing belt
18
Ventilation openings
19
On/Off switch
20
Speed selector (only 2H models)
21
Contact wheel
22
Support surface for plane grinding
23
Drive wheel
24
Lubricating nipple
25
Screw for side cover
26
Side cover
27
Instruction label
28
Clamping lever for adjustment of the working height
Assembly instructions (figure 7).
Mount the machine on the Fein GIB/GIBE sub base (see
assembly instructions).
Fasten the sub base to the floor using suitable dowel/bolt
connections. The connections must withstand the forces
that arise during working.
Faulty assembly can cause the sub base or work bench to
tilt over or the machine to loosen from the sub base or
work bench during operation, and lead to serious acci-
dents.
Electrical connection.
The electrical connection, which is to be provided
by customer, must be carried out by a qualified
electrician.
Observe mains voltage:
The mains voltage and the fre-
quency of the power source must agree with the data
onthe type plate of the machine.
Before starting operation for the first time, check the
rotation direction of the motor. The rotation direction
may be changed only by a qualified electrician.
Adjustments.
Before any work on the machine itself, pull the
mains plug.
Adjusting the incline (figure 7).
Loosen both clamping levers (
28
). Set the machine to the
required working height.
Tighten both clamping levers (
28
) again.
Adjusting the spark guard (5).
Loosen both wing bolts (
6
) and adjust the spark guard (
5
)
in such a manner that the grinding belt is covered off as
far as possible.
Tighten both wing bolts again.
Adjusting the grinding rest (7) (figure 1).
Loosen star-knob bolt (
11
) and adjust the gap size to
2 mm (max.)
.
Tighten the star-knob bolt again.
Adjusting the stop (4) (figure 2)
Loosen screws (3) and adjust a max. gap clearance of
2 mm
.
Tighten screws (3) again.
OBJ_BUCH-0000000317-001.book Page 13 Tuesday, July 10, 2018 9:45 AM