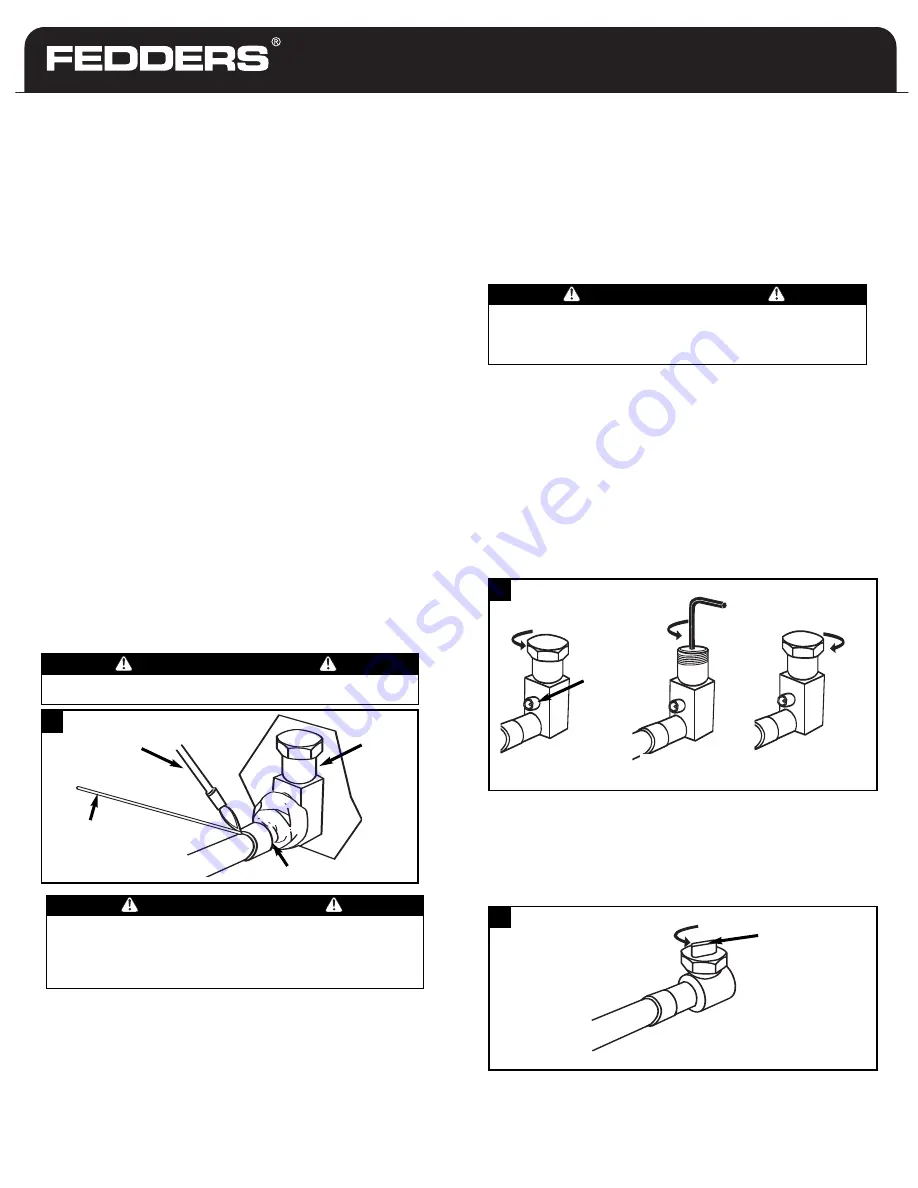
SERVICE VALVE CONNECTIONS
Braze joints
1.
Remove the valve core from the schrader port. Wrap a
quenching cloth around the service valve. Clean and flux
the joint and braze with brazing rod containing at least
10% silver (such as silphos type brazing rod). DO NOT USE
SOFT SOLDER. Replace the schrader valve core after
brazing has cooled.
2.
Leak-check all braze joints at approximately 80 psi
pressure, purge, and evacuate the lines.
Evacuation
The outdoor unit is factory charged. Evacuation is necessary
on the uncharged portions of the total system. Purge the
system with dry nitrogen. Then connect a vacuum pump and
a vacuum gage capable of accurately measuring below
1,000 microns vacuum depth. The deep vacuum method is
the most positive way of assuring a system is free of air and
liquid water.
WARNING
IF THE INSTALLER IS MAKING UP HIS OWN LINE SETS,
HE MUST MAKE SURE THE TUBING IS CLEAN OF ANY
IMPURITIES OR MOISTURE.
WARNING
DO NOT USE AIR TO LEAK-CHECK BRAZE JOINTS.
DRY NITROGEN SHOULD BE USED TO LEAK-CHECK.
WARNING
ALWAYS HAVE A FIRE EXTINGUISHER AVAILABLE
WHEN WORKING WITH AN OPEN FLAME.
ALWAYS USE SAFETY GLASSES, PROTECTIVE
CLOTHING, AND WORK GLOVES.
Torch
Brazing rod
Quenching Cloth
Service
valve
Model
3
Connect Control Wiring
1. Route 24 volt control wires through control wiring
grommet and connect leads to control wiring.
2. Use No. 18 AWG color coded, insulated wire. If thermostat
is located more than 100 ft. from unit, as measured along
the control voltage wires, use No. 16 AWG wire to avoid
excessive voltage drop.
3. All wiring must be NEC Class 1 and must be separated from
incoming power leads. Use furnace transformer, fan coil
transformer, or accessory transformer for control power.
Note: Use of available 24 volt accessories may exceed the
minimum power requirement. Determine total transformer
load and increase the transformer capacity or split the load
with an accessory transformer as required.
Final wiring check
Check factory wiring and field wire connections to ensure
terminations are secured properly. Check wire routing to
ensure wires are not in contact with tubing, sheet metal,
etc.
Electrical Connections (cont.)
Opening the Service Valve (Step Valve)
NOTE: This is not a back-seating valve.
1. Remove the valve cap using an adjustable wrench.
2. Open the valve by inserting a hex wrench (3/16" for the
liquid line, 5/16" for the vapor line) into the stem and back
out counter-clockwise until the valve stem just touches the
retaining ring. Do not over tighten.
3. Replace the valve cap finger-tight, then tighten an
additional
1
/
12
turn or
1
/
2
hex flat. A metal-to-metal seal is
now complete.
Opening the Service Valve (Straight Valve)
NOTE: This is not a back-seating valve.
Open the valve by using an adjustable wrench to turn the
adjusting flange 1/4 turn counter-clockwise. The flange will
come to a stop and the seal is now complete.
Remove cap
Replace cap
Open valve
Schrader
valve port
Open valve
Adjusting
flange
11
6
11
5
11
4