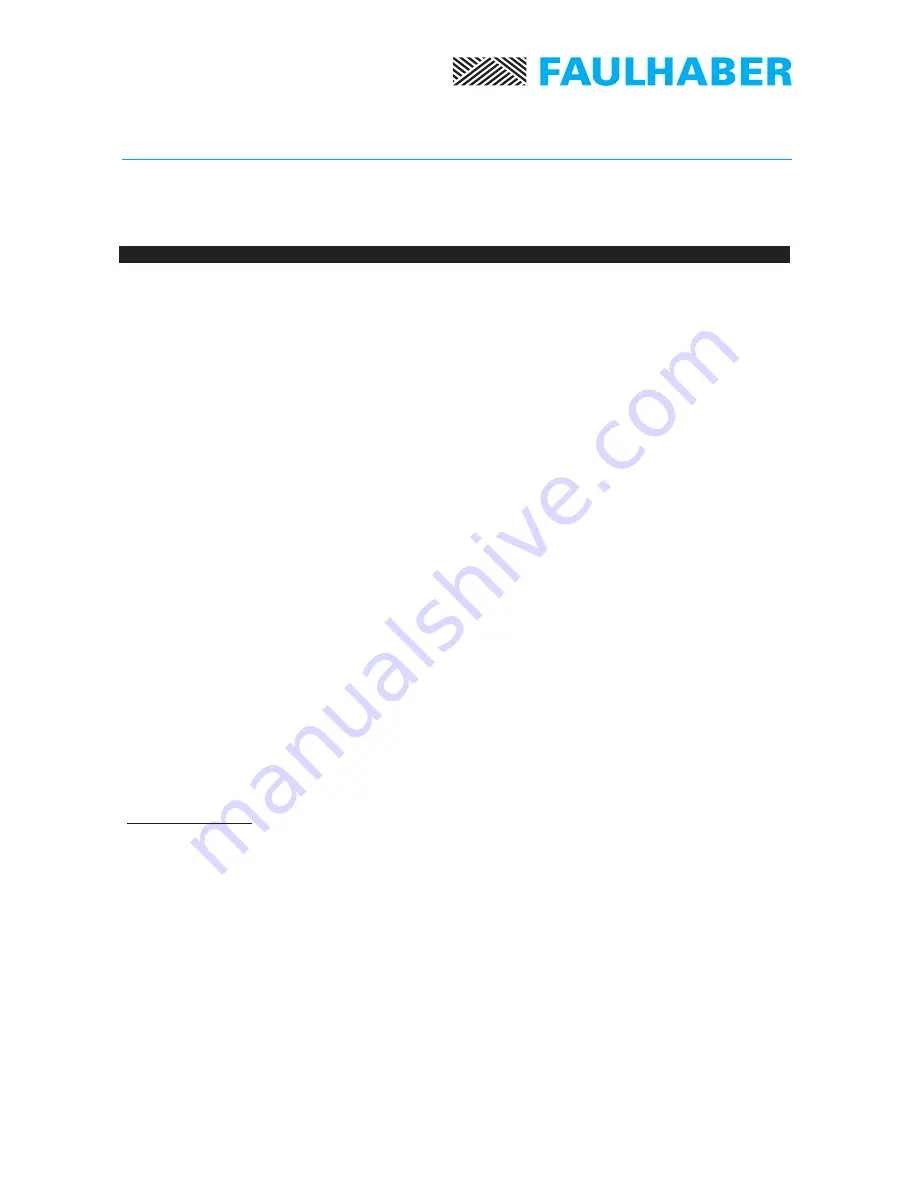
4
Specifications subject to change without notice
General characteristics
6. General characteristics
6.1 Analog Speed command
The speed command is given by an external voltage from 0 to +5 V (optional 0 to +10 V)
or by a potentiometer connected directly to the Servo Amplifier (see fig. 5). The total
potentiometer resistance must be between 10 k
Ω
and 47 k
Ω
.
Furthermore, a PWM signal with a maximum amplitude of 5 V and a minimum frequency of
1 kHz, can be used as speed command.
To control the Servo Amplifier using an analogue speed command voltage
from 0 to +10 V, it is necessary to change the R20 resistance value from 18 k
Ω
(standard) to
5,6 k
Ω
.
6.2 Direction
The direction of rotation is reversed using either a logic high or low input signal.
If not connected (internal pull-up resistance) or a high input signal is applied,
the motor runs in CW direction.
If a low input signal is applied, the motor runs in CCW direction.
6.3 Enable
A high logic at this input causes the motor run.
If not connected (internal pull-up resistance) the Servo Amplifier is enabled.
6.4 Brake
A logic low state (connect to GND) at this input allows the motor to run.
6.5 Power supply internal fuse
An internal F1 fuse is provided on the print board to protect the Servo Amplifier against:
- power supply polarity inversion
- over-load (over-current).
Fuse specification:
2A / 125V - subminiature fuse / Littelfuse type 251.002HE
6.6 Encoder feedback
The option with encoder allows the two incremental encoder channels to be used to
control the motor speed down to 100 rpm.
To use this speed control configuration it is necessary to remove the two jumpers on X4.
Refer to the start-up procedure point 7.3.