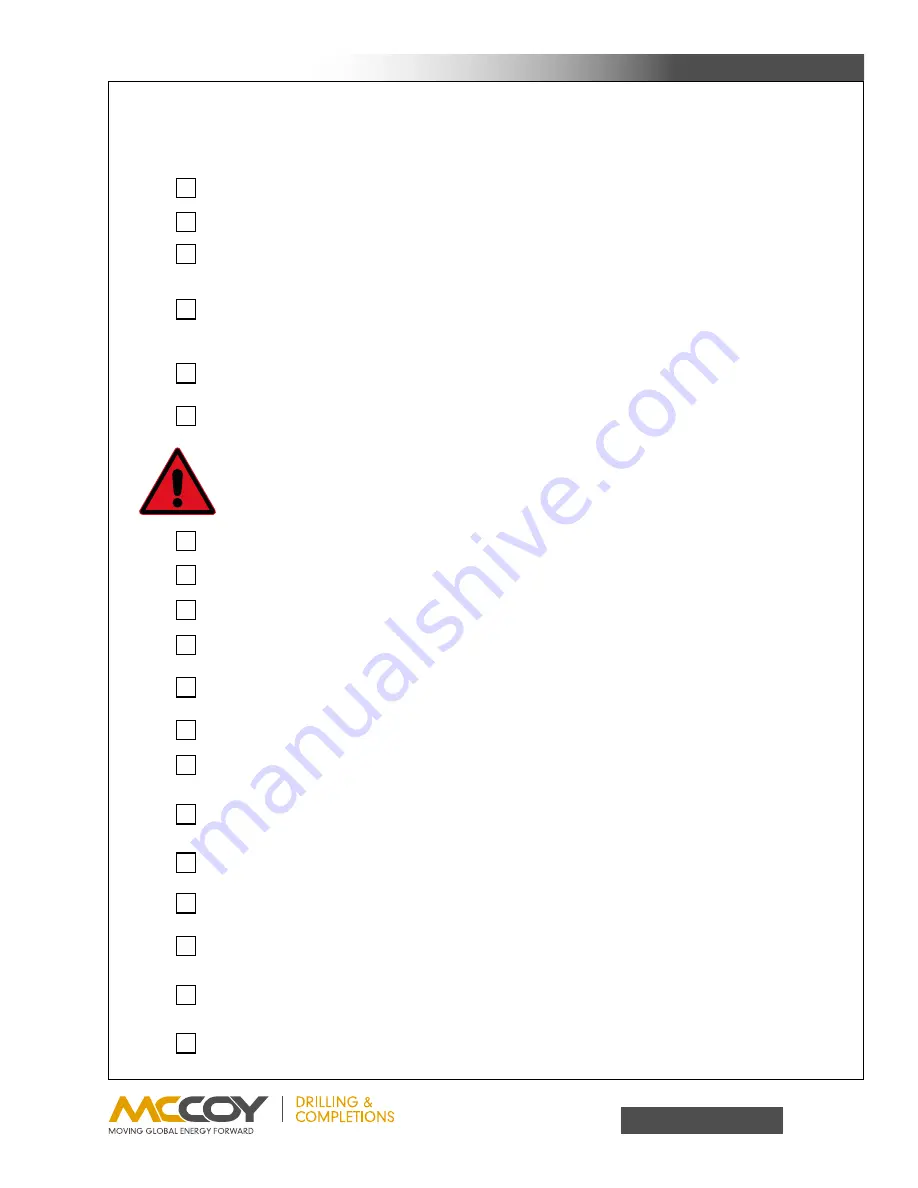
KT5500 5-
1
/
2
” T
ong
& CLInCHER® B
aCKup
S
ECTIon
C
onTEnTS
3.31
T
ECHnICaL
M
anuaL
M
aInTEnanCE
N.
TUBULAR CONNECTION EQUIPMENT RE-COMMISSIONING PROCEDURE
Perform the following recommissioning procedures when removing tubular connection equipment from short or long-term storage
back into regular service. These procedures are essential for ensuring proper equipment preparation and operation. The following
procedures also assume that the decommissioning and storage procedures recommended by Farr have been strictly observed.
7.
Energize power unit.
8.
Ensure that supply pressure is at or above the tong’s specified operating pressure, and that the return pressure is less
than 350 psi.
9.
Perform a thorough inspection of pressurized hydraulic lines and fittings. Any leaking hydraulic fluid lines or fittings must
be replaced before the equipment is returned to service.
10.
Perform a thorough inspection of all seals. Any seal that is leaking or “weeping” must be replaced before the equipment
is returned to service.
11.
Rotate tong in low gear for 5 minutes while monitoring pressurized seals and hydraulic lines. If a seal, line, or fitting begins
to leak while tong is rotating, it must be replaced before the equipment is returned to service. Finish this step with the
rotary gear opening facing the gear train. De-energize the power unit.
12.
Inspect all flexible hydraulic lines for signs of wear, blistering, or any other signs of potential failure - replace if signs of
potential failure are identified.
13.
Inspect the gear train housing. If the amount of grease is inadequate, liberally grease the gear train through the access
panel, and through the opening in the rotary gear.
14.
Inspect top and bottom brake band linings - replace if necessary. Unequal wear of the brake bands indicates that the
brake band tension is not evenly adjusted. Refer to the maintenance section of the manual for instructions on properly
adjusting brake bands. Ensure that all grease is wiped from brake band linings and the parts of the cage plates that come
into contact with the brake band linings
15.
Re-install access panel. Install a set of pre-inspected jaws that are the correct size for the pipe or casing being run.
16.
Install load cell. If using a tension load cell, perform a visual inspection and replace any cracked, broken, or distorted
components including links and chains. If using a compression load cell, replace any component that has been crushed
or otherwise distorted through compression.
17.
If applicable, inspect the load cell anchor pins (tension load cell only). Replace the anchor pins if cracking or metal distor-
tion is seen.
18.
If applicable, the weld securing the single load cell anchor to the bridge bar main plate must be inspected (compression
load cell only). If the integrity of the weld has been compromised, the tong must be removed from service until the weld
is repaired. The load cell beam will need to be disconnected and removed so the weld is visible. Before re-installing the
beam, liberally grease the anchor pin before reinserting into the load cell beam.
19.
Re-energize power unit.
FAILURE TO ENSURE THAT THE SELF-SEALING SUPPLY AND RETURN LINES ARE FULLY
MADE UP MAY RESULT IN CATASTROPHIC EQUIPMENT FAILURE.
1.
Remove all protective plastic wrapping. If there are desiccant packs with the assembly, they may be disposed of with the
regular garbage.
2.
Remove the access panel on the side of the tong directly adjacent to the shifter mechanism.
3.
Wipe excess grease or heavy oil from exposed cylinder rods.
4.
If applicable, re-connect chain sling to lifting lugs. Perform a visual inspection of all lifting points - if visible damage is seen,
including cracks, broken lugs, distorted metal, etc. replace damaged part(s) before placing tong in service. Also inspect
all chains, master links, and turnbuckles - again, if any damage is noted replace the damaged part(s) before placing the
tong in service. If your company requires yearly certification of lifting equipment, ensure that the most recent test date falls
within the past year. Perform recertification if necessary.
5.
Perform a liberal lubrication of the equipment - refer to Maintenance section of manual to determine lubrication points.
Generously fill the gear train housing with grease through the access panel, and also through the opening in the rotary
gear.
6.
Connect the equipment to a hydraulic power unit. Ensure all lines are fully made up to prevent equipment damage from
excessive back pressure. Do not neglect to connect the motor drain.
Содержание KT5500
Страница 2: ......
Страница 4: ...This page intentionally left blank...
Страница 6: ...This page intentionally left blank...
Страница 10: ...This page intentionally left blank...
Страница 23: ...KT5500 5 1 2 Tong CLINCHER Backup Section Contents 2 9 Technical Manual Setup Operation 7 1 2 6 5 12 3 4 11 9 8...
Страница 24: ...KT5500 5 1 2 Tong CLINCHER Backup Section Contents 2 10 Technical Manual Setup Operation 10 13 18 17...
Страница 34: ...This page intentionally left blank...
Страница 78: ...KT5500 5 1 2 Tong CLINCHER Backup Section Contents 5 2 Technical Manual Gear Train Layout J L A B C E F D G H K...
Страница 80: ...KT5500 5 1 2 Tong CLINCHER Backup Section Contents 5 4 Technical Manual Support Roller A B C D E F G E D C H...
Страница 96: ...KT5500 5 1 2 Tong CLINCHER Backup Section Contents 5 20 Technical Manual Brakeband Assembly A B C D E F G...
Страница 120: ...This page intentionally left blank...
Страница 128: ...This page intentionally left blank...
Страница 130: ...This page intentionally left blank...
Страница 137: ...KT5500 5 1 2 Tong CLINCHER Backup Section Contents 7 9 Technical Manual Hydraulic Motor Information...
Страница 144: ...KT5500 5 1 2 Tong CLINCHER Backup Section Contents 7 16 Technical Manual Hydraulic Valve Information...
Страница 145: ...KT5500 5 1 2 Tong CLINCHER Backup Section Contents 7 17 Technical Manual Hydraulic Valve Information...
Страница 146: ...KT5500 5 1 2 Tong CLINCHER Backup Section Contents 7 18 Technical Manual Hydraulic Valve Information...
Страница 147: ...KT5500 5 1 2 Tong CLINCHER Backup Section Contents 7 19 Technical Manual Hydraulic Valve Information...
Страница 148: ...KT5500 5 1 2 Tong CLINCHER Backup Section Contents 7 20 Technical Manual Hydraulic Valve Information...
Страница 149: ...KT5500 5 1 2 Tong CLINCHER Backup Section Contents 7 21 Technical Manual Hydraulic Valve Information...
Страница 150: ...KT5500 5 1 2 Tong CLINCHER Backup Section Contents 7 22 Technical Manual Hydraulic Valve Information...
Страница 151: ...KT5500 5 1 2 Tong CLINCHER Backup Section Contents 7 23 Technical Manual Hydraulic Valve Information...
Страница 152: ...KT5500 5 1 2 Tong CLINCHER Backup Section Contents 7 24 Technical Manual Hydraulic Valve Information...
Страница 153: ...KT5500 5 1 2 Tong CLINCHER Backup Section Contents 7 25 Technical Manual Hydraulic Valve Information...
Страница 154: ...KT5500 5 1 2 Tong CLINCHER Backup Section Contents 7 26 Technical Manual Hydraulic Valve Information...
Страница 155: ...KT5500 5 1 2 Tong CLINCHER Backup Section Contents 7 27 Technical Manual Hydraulic Valve Information...
Страница 156: ...KT5500 5 1 2 Tong CLINCHER Backup Section Contents 7 28 Technical Manual Hydraulic Valve Information...
Страница 157: ...KT5500 5 1 2 Tong CLINCHER Backup Section Contents 7 29 Technical Manual Hydraulic Valve Information...