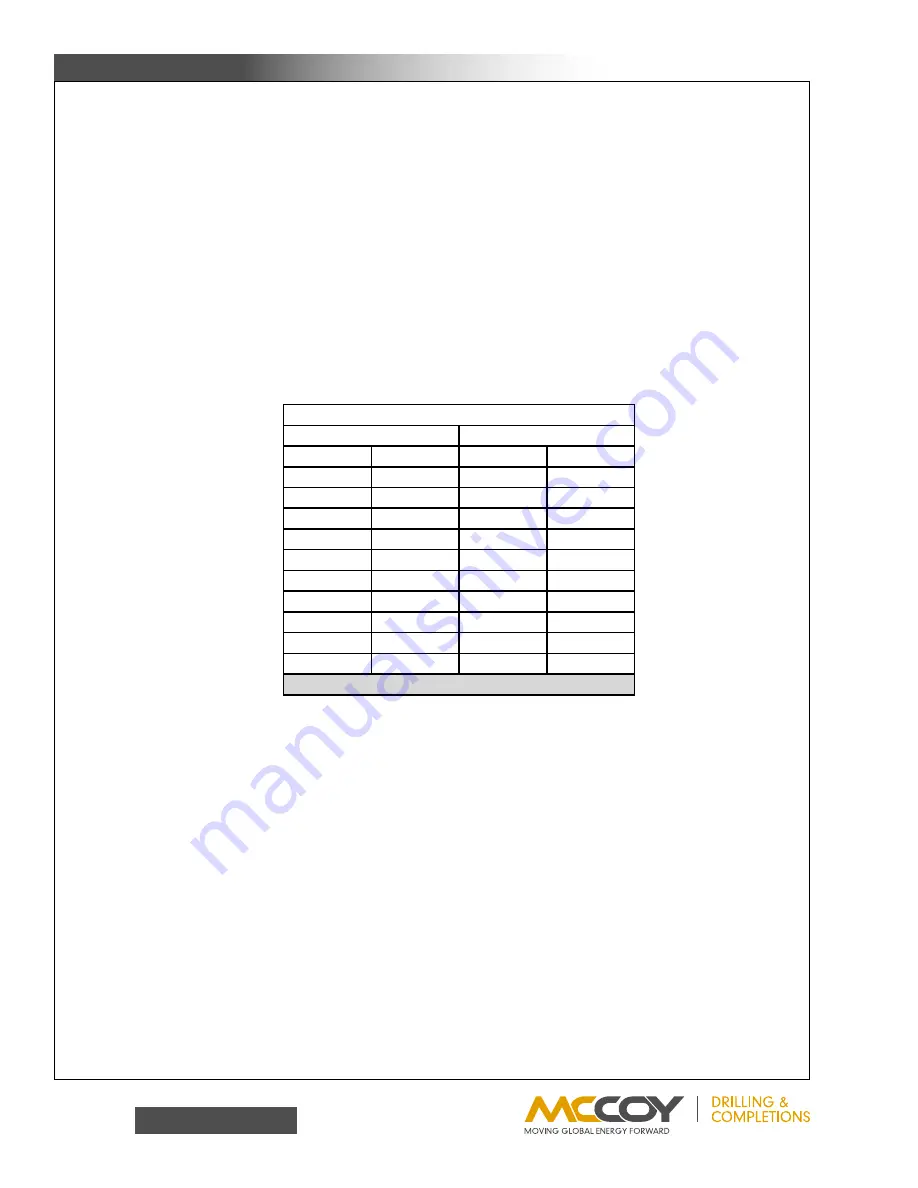
KT5500 5-
1
/
2
” T
ong
& CLInCHER® B
aCKup
S
ECTIon
C
onTEnTS
2.2
T
ECHnICaL
M
anuaL
S
ETup
& o
pERaTIon
1. Inspection Of Slings
McCoy Drilling & Completions strongly recommends the following practices:
A complete inspection of new load-bearing devices and attachments shall be performed by a qualified, designated person prior
to initial use. Each link and component shall be examined individually, taking care to expose and examine all surfaces including
the inner link surface. The sling shall be examined for conditions such as those listed in the removal criteria below. In addition,
daily inspection of slings, fastenings and attachments shall be performed by a designated person. If damage or defects are found
at either inspection, the damaged or defective component shall be quarantined from service until it can be properly repaired or
replaced.
Removal Criteria:
A load-bearing device shall be removed from service if conditions such as the following are present:
• Missing or illegible sling identification.
• Cracks or breaks
• Evidence of tampering is seen - sling tag has been modified or obscured, or tamper-proof nuts are missing.
• Signs of impact on load-bearing components, including spreader bars, lifting lugs, rigid slings & rigid sling weldments, and
legs & leg mounts.
• Broken or damaged welds.
• Excessive wear, nicks, or gouges. Refer to the chart below to ensure minimum thickness on chain links supplied is not be
below the values listed:
Minimum Allowable Chain Link Thickness at Any Point
Nominal Chain Size
Minimum Thickness
Inches
MM
Inches
MM
7/32
5.5
0.189
4.80
9/32
7
0.239
6.07
5/16
8
0.273
6.93
3/8
10
0.342
8.69
1/2
13
0.443
11.26
5/8
16
0.546
13.87
3/4
20
0.687
17.45
7/8
22
0.750
19.05
1
26
0.887
22.53
1-1/4
32
1.091
27.71
Refer To ASME B30.9
• Stretched, bent, twisted, or deformed chain links or components.
• Evidence of heat damage.
• Excessive pitting or corrosion.
• Lack of ability of chain or components to hinge (articulate) freely.
• Weld splatter.
• For hooks, removal criteria as stated in ASME B30.10
• Other conditions, including visible damage, that cause doubt as to the continued use of the sling.
Inspect all lugs and fixing points for signs of elongation and/or bending, or for material build-up around the hole. Repair or
replace components that appear distorted. Ensure all hardware is tight and in good condition. Replace missing hardware if
necessary. All hardware must be free of rust and corrosion.
Additional inspections shall be performed during sling use where service conditions warrant. Periodic inspection intervals shall
not exceed one year. The frequency of periodic inspections should be based on:
• Frequency of use of the load-bearing device.
• Severity of service conditions
• Nature of lifts being made
• Experience gained on the service life of load-bearing devices used in similar circumstances.
Guidelines for the interval are:
• Normal Service - yearly
• Severe Service - monthly to quarterly
• Special Service - as recommended by a qualified person
Содержание 80-0420-16
Страница 2: ......
Страница 4: ...This page intentionally left blank ...
Страница 6: ...This page intentionally left blank ...
Страница 10: ...This page intentionally left blank ...
Страница 24: ...KT5500 5 1 2 Tong CLINCHER Backup Section Contents 2 10 Technical Manual Setup Operation 10 13 18 17 ...
Страница 34: ...This page intentionally left blank ...
Страница 80: ...KT5500 5 1 2 Tong CLINCHER Backup Section Contents 5 4 Technical Manual Support Roller A B C D E F G E D C H ...
Страница 96: ...KT5500 5 1 2 Tong CLINCHER Backup Section Contents 5 20 Technical Manual Brakeband Assembly A B C D E F G ...
Страница 120: ...This page intentionally left blank ...
Страница 128: ...This page intentionally left blank ...
Страница 130: ...This page intentionally left blank ...
Страница 137: ...KT5500 5 1 2 Tong CLINCHER Backup Section Contents 7 9 Technical Manual Hydraulic Motor Information ...
Страница 144: ...KT5500 5 1 2 Tong CLINCHER Backup Section Contents 7 16 Technical Manual Hydraulic Valve Information ...
Страница 145: ...KT5500 5 1 2 Tong CLINCHER Backup Section Contents 7 17 Technical Manual Hydraulic Valve Information ...
Страница 146: ...KT5500 5 1 2 Tong CLINCHER Backup Section Contents 7 18 Technical Manual Hydraulic Valve Information ...
Страница 147: ...KT5500 5 1 2 Tong CLINCHER Backup Section Contents 7 19 Technical Manual Hydraulic Valve Information ...
Страница 148: ...KT5500 5 1 2 Tong CLINCHER Backup Section Contents 7 20 Technical Manual Hydraulic Valve Information ...
Страница 149: ...KT5500 5 1 2 Tong CLINCHER Backup Section Contents 7 21 Technical Manual Hydraulic Valve Information ...
Страница 150: ...KT5500 5 1 2 Tong CLINCHER Backup Section Contents 7 22 Technical Manual Hydraulic Valve Information ...
Страница 151: ...KT5500 5 1 2 Tong CLINCHER Backup Section Contents 7 23 Technical Manual Hydraulic Valve Information ...
Страница 152: ...KT5500 5 1 2 Tong CLINCHER Backup Section Contents 7 24 Technical Manual Hydraulic Valve Information ...
Страница 153: ...KT5500 5 1 2 Tong CLINCHER Backup Section Contents 7 25 Technical Manual Hydraulic Valve Information ...
Страница 154: ...KT5500 5 1 2 Tong CLINCHER Backup Section Contents 7 26 Technical Manual Hydraulic Valve Information ...
Страница 155: ...KT5500 5 1 2 Tong CLINCHER Backup Section Contents 7 27 Technical Manual Hydraulic Valve Information ...
Страница 156: ...KT5500 5 1 2 Tong CLINCHER Backup Section Contents 7 28 Technical Manual Hydraulic Valve Information ...
Страница 157: ...KT5500 5 1 2 Tong CLINCHER Backup Section Contents 7 29 Technical Manual Hydraulic Valve Information ...