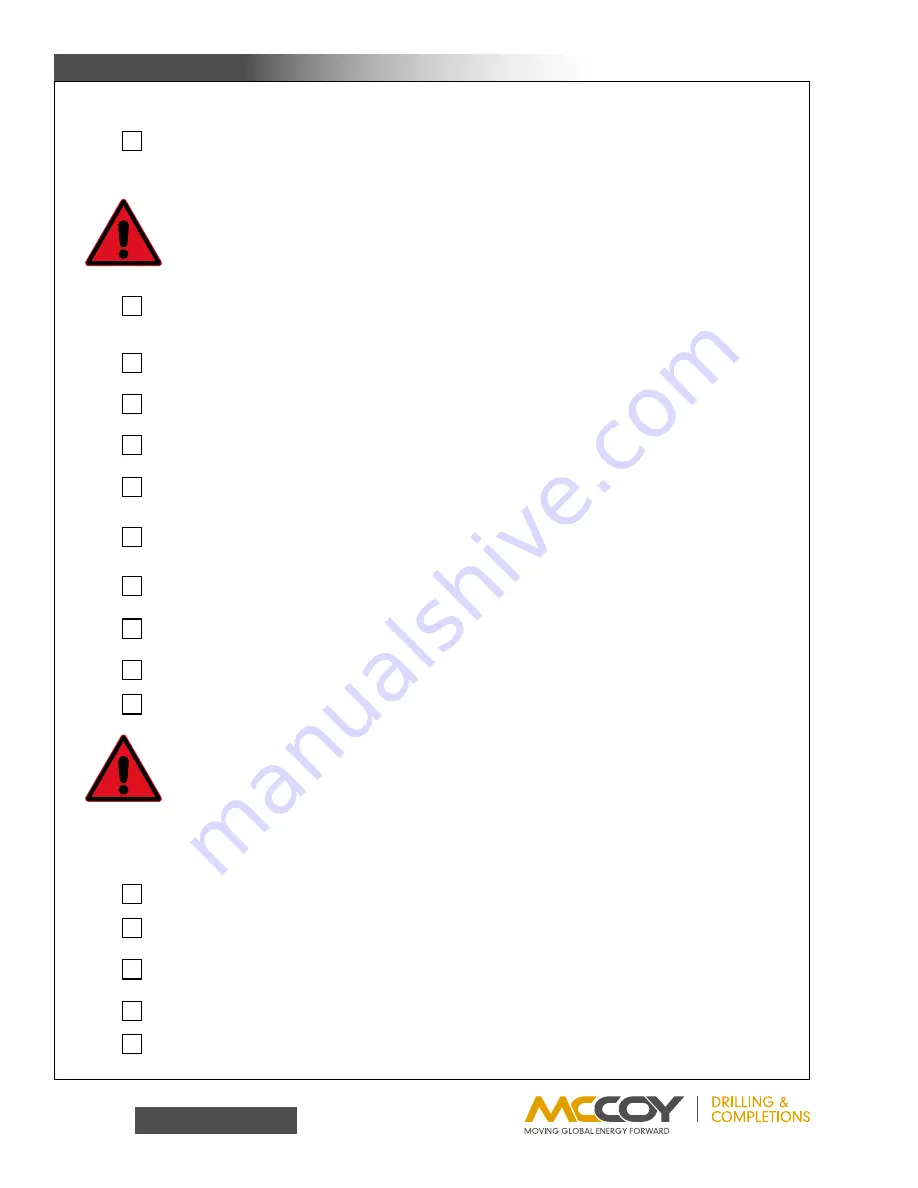
KT5500 5-
1
/
2
” T
ong
& CLInCHER® B
aCKup
S
ECTIon
C
onTEnTS
3.24
T
ECHnICaL
M
anuaL
M
aInTEnanCE
12.
Perform a visual inspection of all lifting points - if visible damage is seen, including cracks, broken lugs, distorted metal,
etc. replace damaged part(s) before placing tong in service. Also inspect all chains, master links, and turnbuckles -
again, if any damage is noted replace the damaged part(s) before placing the tong in service. Refer to Section 2A of
the technical manual (Sling/Load Bearing Device Safety) for information on recommended testing and recertification.
Please note that turnbuckles with part number 101-3086 (short turnbuckles) use a high-strength pin which must be
supplied by Farr.
If using a stand-alone power unit, start it now - refer to the power unit technical manual for startup procedures. Listen to power unit for
a moment to see if there are any unusual mechanical sounds (rubbing, grinding, excessive pump noise). If using a diesel unit, allow
sufficient time for the engine to reach operating temperature before increasing engine RPM. Once engine is warm, gradually increase
engine RPM until operating speed is reached.
23.
Ensure that supply pressure is at or above the tong’s specified operating pressure, and that the return pressure is less
than 350 psi.
24.
Perform a visual inspection of pressurized hydraulic lines. If any hydraulic fittings or hoses are leaking they must be
repaired or replaced before proceeding.
25.
Rotate tong for one minute, stop, and reverse the direction of rotation for another minute, ending with the opening of
the rotary gear facing the gear train. De-energize the power unit, and perform another generous lubrication of the gear
train, including the gear housing.
26.
Energize power unit. Rotate tong for one minute, stop, and reverse the direction of rotation for another minute, ending
with the opening of the rotary gear facing the gear train.
27.
De-energize the power unit, and perform a third generous lubrication of the gear train, including the gear housing.
FAILURE TO ENSURE THAT THE SELF-SEALING SUPPLY AND RETURN LINES ARE FULLY
MADE UP MAY RESULT IN CATASTROPHIC EQUIPMENT FAILURE.
“SHORT” TURNBUCKLES HAVING PART NUMBER 101-3086 EMPLOY HIGH-STRENGTH PINS
WHICH MUST BE SUPPLIED BY FARR.
13.
Rotate the gear train by hand, and use a flashlight to perform a visual inspection of the gear train through the access
panel and the opening of the rotary gear while the gear train is being rotated. If gear damage or chips of metal are
seen, the tong should be removed from service and overhauled to avoid further damage. Replace access panel when
inspection is complete.
14.
Inspect all jaws and dies in use for the maintenance interval. Inspect the jaw roller pins for signs of damage - replace
pins if necessary. If the pins are welded in place, remove and quarantine the jaw until the weld is repaired. Ensure dies
are secure in the jaw - replace worn dies if necessary. Ensure that the jaw rollers rotate freely.
15.
Inspect backing pin(s). If cracked, broken, or bent it (they) must be replaced.
16.
Inspect top and bottom brake band linings - replace if necessary. Unequal wear of the brake bands indicates that the
brake band tension is not evenly adjusted. Refer to the maintenance section of the manual for instructions on properly
adjusting brake bands.
17.
Inspect door springs. Ensure the springs retain sufficient strength to be able to assist the opening of the door, and to
keep the door open. The springs should also help to “snap” the door shut.
18.
Inspect backup springs (if applicable). The rear extension springs should be equally extended, and the front leg springs
should be equally compressed. Ensure that neither of the rear backup springs have been over-extended and lack
sufficient tension to adequately support the backup. Ensure that neither of the front leg springs have been over-com-
pressed, and still retain enough spring strength to support the front of the backup.
19.
Extend all hydraulic cylinders, and inspect cylinder rods for signs of mechanical damage, flaking, or rust. Farr recom-
mends that damaged cylinders be replaced prior to storage.
20.
Perform a visual inspection of all hydraulic lines. Replace flexible lines if they appear to be cracked, fatigued, or have
visible signs of wear from contact with a rigid object. If your tong is equipped with rigid hydraulic lines, replace any line
that is dented or appears to be stressed or cracked.
21.
Generously fill the gear train housing with grease through the access panel, and also through the opening in the rotary
gear. Perform a full lubrication - refer to Maintenance section of manual to determine lubrication points.
22.
Ensure main supply and return connections to the tong are fully made up. Re-connect the remainder of the hydraulic
lines, and, if applicable, the electrical line to the turns counter.
Содержание 80-0420-16
Страница 2: ......
Страница 4: ...This page intentionally left blank ...
Страница 6: ...This page intentionally left blank ...
Страница 10: ...This page intentionally left blank ...
Страница 24: ...KT5500 5 1 2 Tong CLINCHER Backup Section Contents 2 10 Technical Manual Setup Operation 10 13 18 17 ...
Страница 34: ...This page intentionally left blank ...
Страница 80: ...KT5500 5 1 2 Tong CLINCHER Backup Section Contents 5 4 Technical Manual Support Roller A B C D E F G E D C H ...
Страница 96: ...KT5500 5 1 2 Tong CLINCHER Backup Section Contents 5 20 Technical Manual Brakeband Assembly A B C D E F G ...
Страница 120: ...This page intentionally left blank ...
Страница 128: ...This page intentionally left blank ...
Страница 130: ...This page intentionally left blank ...
Страница 137: ...KT5500 5 1 2 Tong CLINCHER Backup Section Contents 7 9 Technical Manual Hydraulic Motor Information ...
Страница 144: ...KT5500 5 1 2 Tong CLINCHER Backup Section Contents 7 16 Technical Manual Hydraulic Valve Information ...
Страница 145: ...KT5500 5 1 2 Tong CLINCHER Backup Section Contents 7 17 Technical Manual Hydraulic Valve Information ...
Страница 146: ...KT5500 5 1 2 Tong CLINCHER Backup Section Contents 7 18 Technical Manual Hydraulic Valve Information ...
Страница 147: ...KT5500 5 1 2 Tong CLINCHER Backup Section Contents 7 19 Technical Manual Hydraulic Valve Information ...
Страница 148: ...KT5500 5 1 2 Tong CLINCHER Backup Section Contents 7 20 Technical Manual Hydraulic Valve Information ...
Страница 149: ...KT5500 5 1 2 Tong CLINCHER Backup Section Contents 7 21 Technical Manual Hydraulic Valve Information ...
Страница 150: ...KT5500 5 1 2 Tong CLINCHER Backup Section Contents 7 22 Technical Manual Hydraulic Valve Information ...
Страница 151: ...KT5500 5 1 2 Tong CLINCHER Backup Section Contents 7 23 Technical Manual Hydraulic Valve Information ...
Страница 152: ...KT5500 5 1 2 Tong CLINCHER Backup Section Contents 7 24 Technical Manual Hydraulic Valve Information ...
Страница 153: ...KT5500 5 1 2 Tong CLINCHER Backup Section Contents 7 25 Technical Manual Hydraulic Valve Information ...
Страница 154: ...KT5500 5 1 2 Tong CLINCHER Backup Section Contents 7 26 Technical Manual Hydraulic Valve Information ...
Страница 155: ...KT5500 5 1 2 Tong CLINCHER Backup Section Contents 7 27 Technical Manual Hydraulic Valve Information ...
Страница 156: ...KT5500 5 1 2 Tong CLINCHER Backup Section Contents 7 28 Technical Manual Hydraulic Valve Information ...
Страница 157: ...KT5500 5 1 2 Tong CLINCHER Backup Section Contents 7 29 Technical Manual Hydraulic Valve Information ...