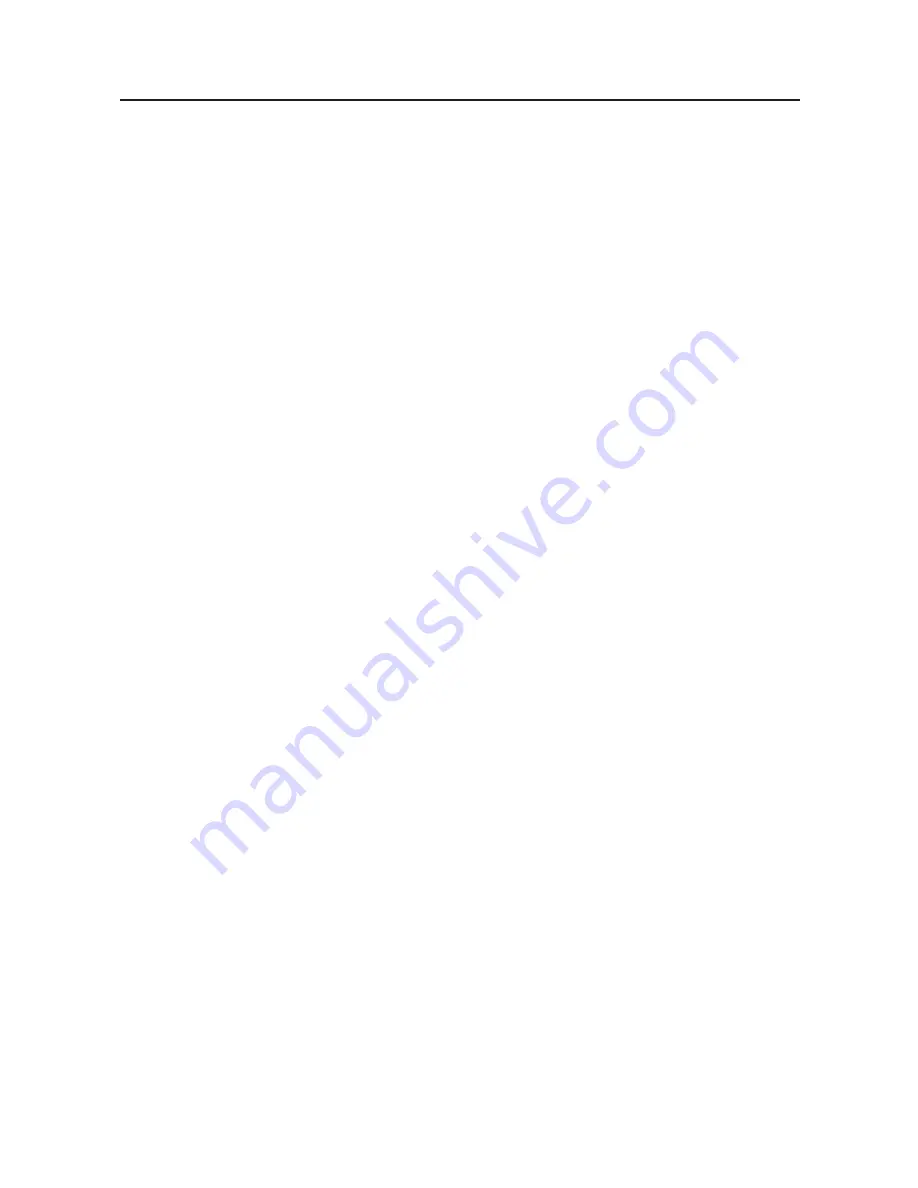
17
Before commissioning the appliance, the whole gas installation including the meter MUST be purged and test-
ed for gas soundness.
IMPORTANT: open all doors and windows, extinguish naked lights, and DO NOT SMOKE whilst purg-
ing the gas line.
Before commencing the commissioning procedure, ensure that the central heating system and the domestic
hot and cold water system have been flushed. This will remove contamination which could cause the boiler
to fail.
6.1 DOMESTIC HOT WATER
Turn on the DHW isolation valve.
Fill and vent the installation by turning on the various hot water taps in the installation
Make sure that there are no leaks in the installation
6.2 CENTRAL HEATING CIRCUIT
In order for the boiler to function correctly, the pressure in the central heating circuit must be between 0.75
and 1 bar when cold.
Both the boiler and the central heating installation must be purged of any air in the water pipes which may
cause noise and the incorrect functioning of the system.
The boiler is fitted with an automatic air vent. Check that the cap, found on the top left surface of the boiler,
is loose.
In order to fill the installation correctly the following sequence must be followed:
- Turn on the radiator air vents.
- Fill the central heating circuit using the approved method given in section 4.8
- Turn off each of the air vents as water starts to appear from them.
- Turn off the filling tap when the pressure gauge exceeds 1 bar.
- Turn the main control switch to the winter setting, making sure that the pump runs. Do not allow the pump
to run when dry.
- Vent the central heating circuit once more. Then let the pressure in the circuit settle at 1 bar.
- Make sure that there are no leaks in the installation.
VERY IMPORTANT: Never turn on the boiler before the system is filled. Allowing the pump to run dry
will cause serious damage.
6.3 GAS CIRCUIT
Purge the gas circuit as described above. Turn on the gas cock to the installation and check that there are
no leaks using leak detection fluid
6.4 SETTINGS
Before leaving the factory the boiler is pre-set in accordance with the information on the data plate, and there-
fore needs no further adjustment.
6.- COMMISSIONING INSTRUCTIONS
Содержание FEB-20E UK ECOPLUS
Страница 1: ...FEB 20E UK ECOPLUS USER INSTRUCTIONS AND TECHNICAL INSTRUCTIONS...
Страница 23: ......