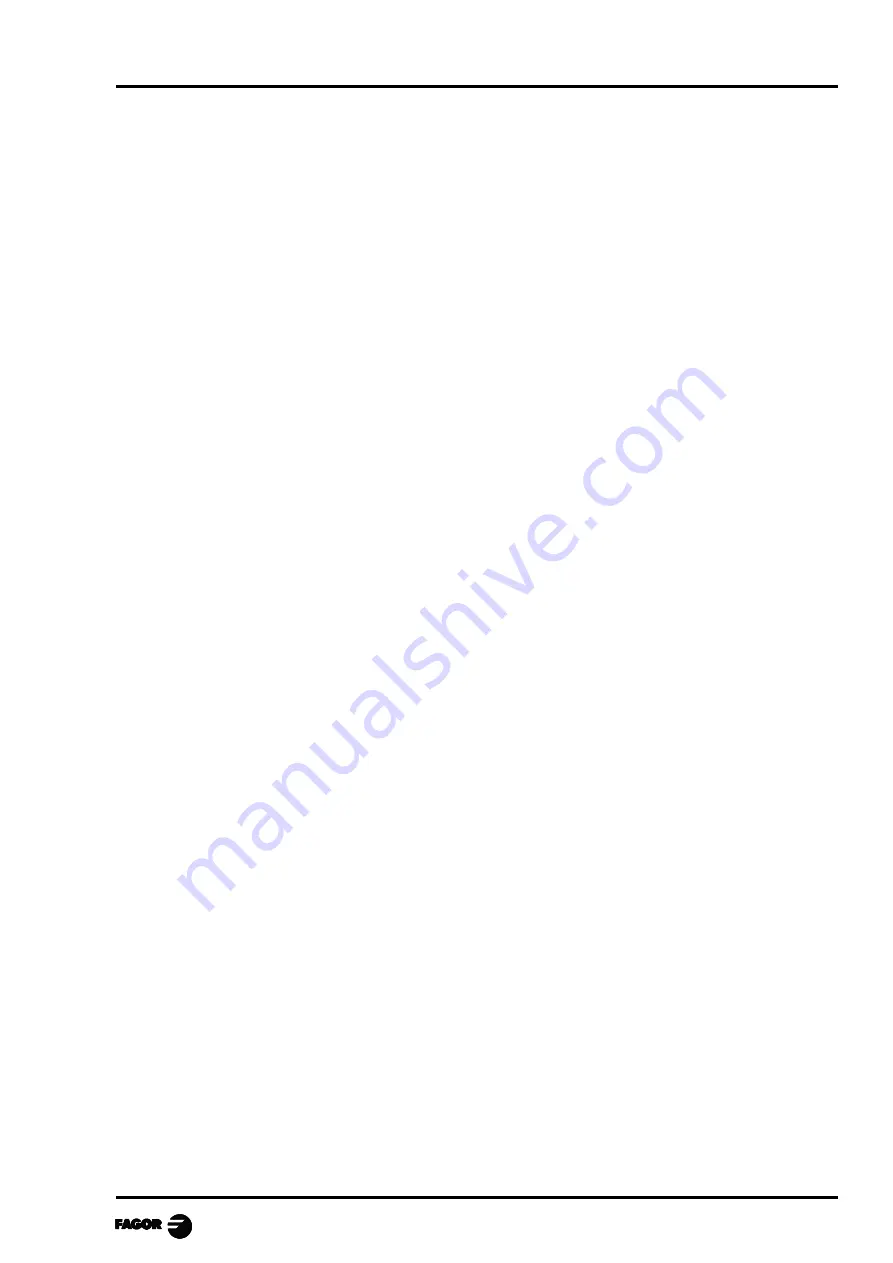
Chapter 2 - page 11
MC work mode
2.
Operating in JOG mode
2.4
Jogging the axes
2.4.4 Feed Handwheel
2.4.4 FEED HANDWHEEL
Usually, when making a part for the first time, the machine feedrate is controlled by means of the
feedrate override switch.
From this version on, it is possible to use the machine handwheels to control that feedrate. This way,
the machining feedrate will depend on how fast the handwheel is turned.
To do this, proceed as follows:
Inhibit all the feedrate override switch positions from the PLC.
Detect how far the handwheel is turned (reading of pulses received)
Set the corresponding feedrate from the PLC depending on the pulses received from the
handwheel.
The following CNC variables return the number of pulses the handwheel has turned.
HANPF
shows the number of pulses of the 1st handwheel.
HANPS
shows the number of pulses of the 2nd handwheel.
HANPT
shows the number of pulses of the 3rd handwheel.
HANPFO shows the number of pulses of the 4th handwheel.
To use this feature, the handwheel must be associated with one of the axes of the machine. General
machine parameters “AXIS1....8” or “HANDWHE1....4” set with values: “21....29”
Example: The machine has a button to activate and deactivate this feature (feed handwheel) and the
feedrate control is carried out with the second handwheel.
CY1
R101=0
Resets the register containing the previous handwheel
reading
END
PRG
DFU I71 = CPL M1000
Every time the button is pressed, mark M1000 is inverted
M1000 = MSG1
If the feature is active, a message is displayed.
NOT M1000
If the feature is not active
= AND KEYDIS4 $FF800000 KEYDIS4
enables all the positions of the feedrate override
switch
= JMP L101
and goes on with program execution
If the feature is active
DFU M2009
and a leading edge (up flank) occurs at the clock mark
M2009
= CNCRD(HANPS,R100,M1)
We read the number of handwheel pulses contained in
R100
= SBS R101 R100 R102
calculates the number of pulses received from the last
reading
= MOV R100 R101
updates R101 for the next reading
= MLS R102 3 R103
calculates in R103 the proper % of feedrate override
= OR KEYDIS4 $7FFFFF KEYDIS4
inhibits all the other positions of the feedrate override
switch
CPS R103 LT 0 = SBS 0 R103 R103
ignores the handwheel turning direction
CPS R103 GT 120 = MOV 120 R103 Limits the maximum feedrate override to 120%.
DFU M2009
With the leading edge (up flank) of the clock mark
M2009
= CNCWR(R103,PLCFRO,M1)
set the calculated feedrate override (PLCFRO=R103)
L101
END
Содержание 8040 CNC - FEATURES
Страница 1: ...REF 0307 SOFT M 7 XX SOFT M 7 1X 8040 CNC NEW FEATURES ...
Страница 2: ...Page 2 of 2 8040 CNC NEW FEATURES SOFT M 7 XX SOFT M 7 1X ...
Страница 45: ...User notes NEW FEATURES SOFT M 7 XX Page 41 of 48 8040 CNC ...
Страница 46: ...User notes NEW FEATURES SOFT M 7 XX Page 42 of 48 8040 CNC ...
Страница 52: ...User notes NEW FEATURES SOFT M 7 1X Page 48 of 48 8040 CNC ...
Страница 53: ...Operating Manual MC option Ref 0204 ing ...
Страница 143: ...Self teaching Manual MC option Ref 0112 ing ...
Страница 147: ...Chapter 1 Theory on CNC machines ...
Страница 156: ...Chapter 2 Theory on tools ...
Страница 164: ...Chapter 3 Hands on training ...
Страница 186: ...Chapter 4 Automatic Operations ...
Страница 201: ...Chapter 5 Summary of work cycles ...
Страница 220: ...Chapter 6 Conversational part programs ...
Страница 235: ...Appendix I Programming example ...
Страница 237: ...Self teaching Manual Appendix I Page 3 MC Model Programming example Step 1 Surface milling 1 ...
Страница 238: ...Self teaching Manual Appendix I Page 4 MC Model Programming example Step 2 Machining the profile 2 Other data ...
Страница 239: ...Self teaching Manual Appendix I Page 5 MC Model Programming example Step 3 Rectangular boss 3 ...
Страница 240: ...Self teaching Manual Appendix I Page 6 MC Model Programming example Step 4 Circular pocket 4 ...
Страница 241: ...Self teaching Manual Appendix I Page 7 MC Model Programming example Step 5 Rectangular pocket 5 ...