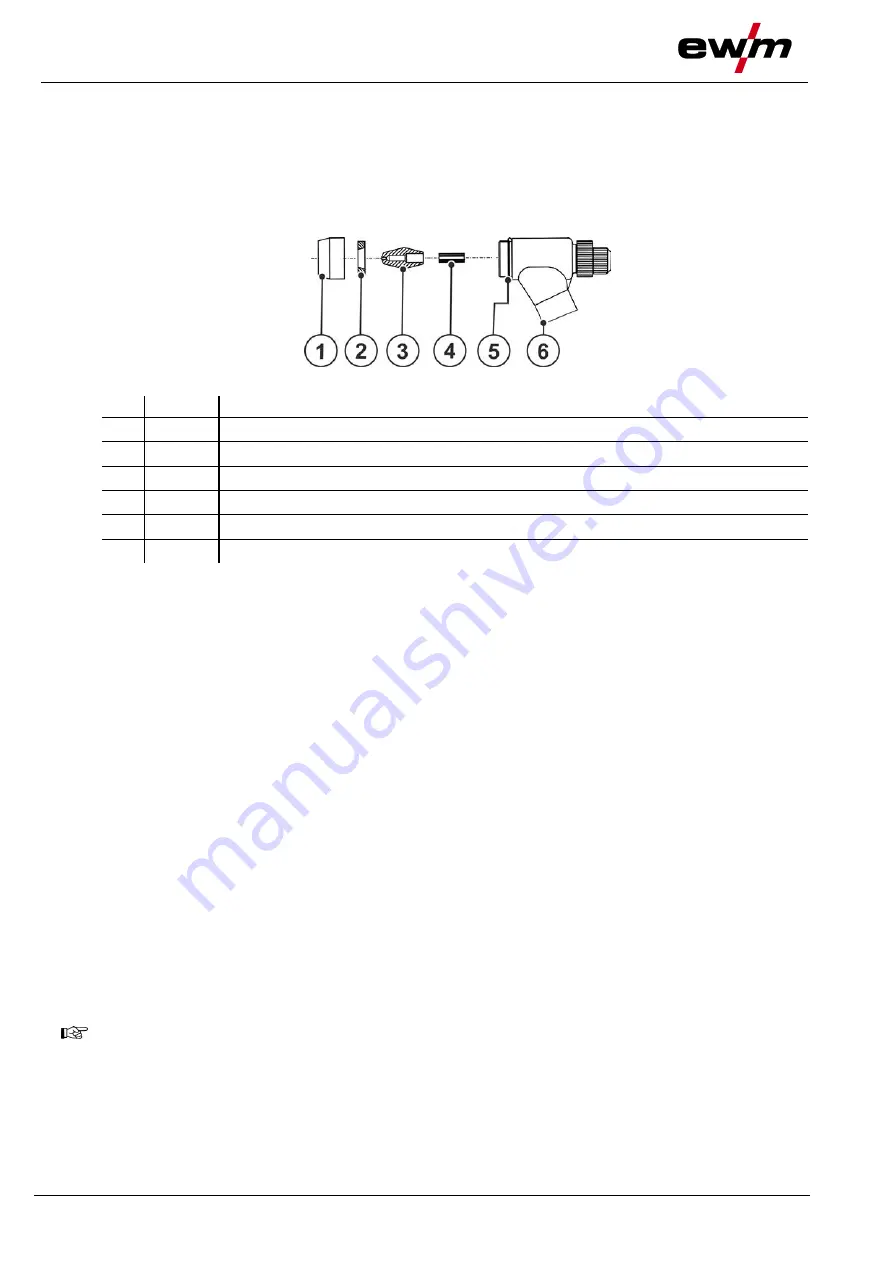
Design and function
Wear part replacement
20
099-008232-EW501
26.05.2020
5.9.2 Changing the contact tip
The choice of the plasma nozzle depends on the application and the associated current
load
> see 5.8 chapter
.
The plasma nozzle should be replaced when the nozzle channel is damaged and therefore no longer cir-
cular.
When changing the nozzle, the electrode and the centring piece should always be checked for wear and
damage.
Figure 5-10
Item Symbol Description
0
1
Gas nozzle
2
Gas lens
3
Plasma nozzle
4
Gas guide insert
5
Sealing ring of the gas nozzle
6
Torch body
• Unscrew the gas nozzle (1).
• Remove the gas lens (2) from the gas nozzle or plasma nozzle (3).
• Pull the plasma nozzle carefully by hand out of the torch body (6). Turn the nozzle slightly around its
axis if it is too tight. For plasma nozzles with a circumferential groove, pliers can be used; for plasma
nozzles with key flats, the nozzle key must be used. Never force the plasma nozzle out by canting as
the retainer cone in the torch body will be deformed.
• Remove the gas guide insert (4) from the plasma nozzle.
• Clean the sealing surfaces and check for defective components before inserting new parts.
• Check the sealing ring of the gas nozzle (5) and replace if damaged. Rub the sealing ring of the gas
nozzle lightly with lubricant VR 500
[1]
.
• Check the gas lens for damage, especially the retainer cone for the plasma nozzle.
• Place the gas lens in the gas nozzle and make sure that it lies flat on the provided attachment of the
gas nozzle and that it can still be moved freely when inserted in the gas nozzle.
• Push the gas guide insert into the new plasma nozzle.
• Rub the contact surface of the plasma nozzle towards the torch body lightly with thermal paste
[1]
,
place it in the retainer cone of the gas lens and insert it together with the gas nozzle in the welding
torch. The electrode leads through the centre hole of the gas guide insert.
• Screw the gas nozzle with the plasma nozzle firmly onto the welding torch to ensure good heat dissi-
pation to the water-cooled retainer cone of the nozzle.
[1]
> see 10 chapter
5.9.3 Electrode change
To prevent damage to the device and incorrect welding results, the electrode gap must be set
with an electrode setting gauge each time the electrode is changed > see 5.9.3.3 chapter.