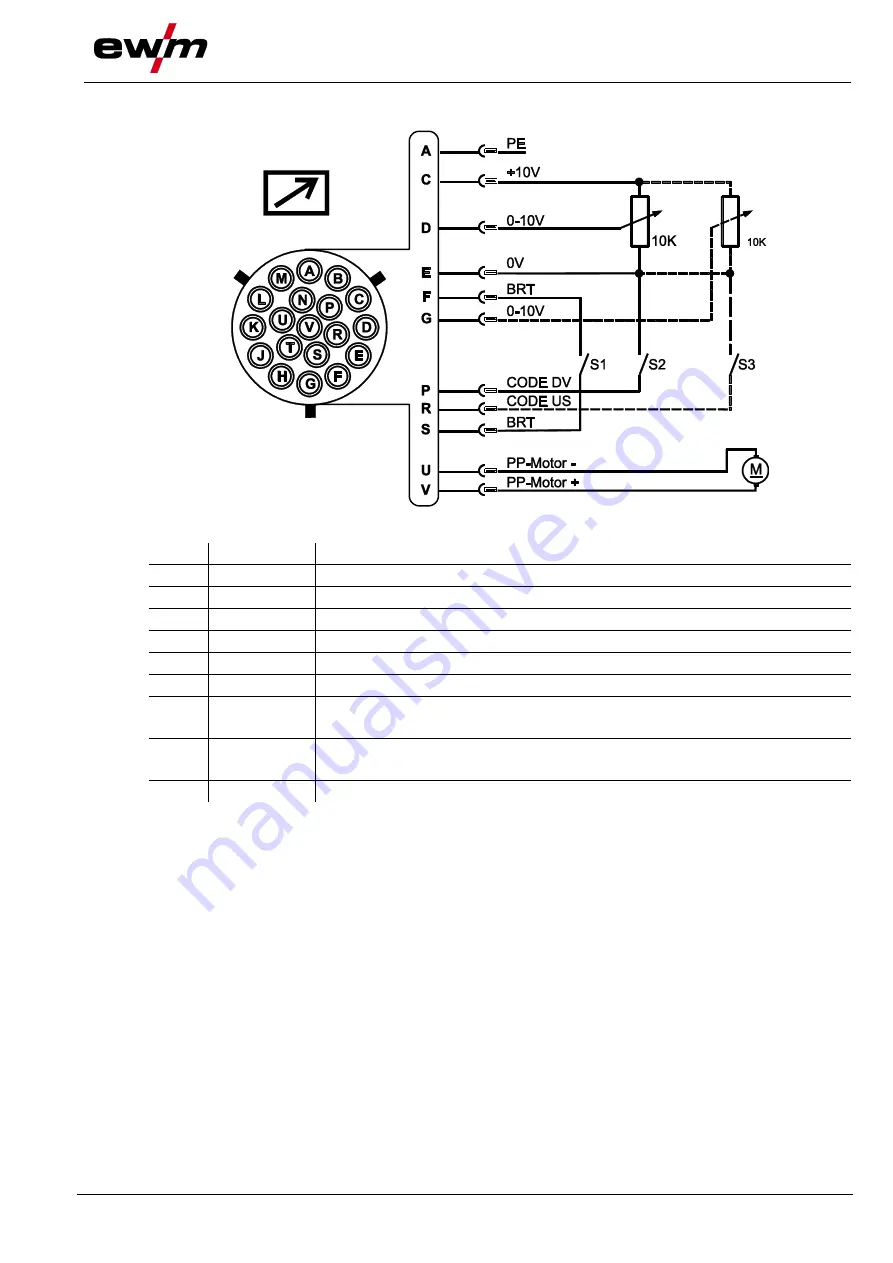
Design and function
Interfaces for automation
099-005504-EW501
20.11.2015
73
5.14.2 Remote control connection socket, 19-pole
Figure 5-40
Pin
Signal form
Short description
A
Output
Connection for PE cable screen
C
Output
Reference voltage for potentiometer 10 V (max. 10 mA)
D
Input
Control voltage specification (0 V
–10 V) – wire feed speed
E
Output
Reference potential (0 V)
F/S
Input
Welding power start/stop (S1)
G
Input
Control voltage specification (0 V
–10 V) – arc length correction
P
Input
Activation of control voltage specification for wire feed speed (S2)
For activation, put signal to reference potential 0 V (pin E)
R
Input
Activation of control voltage specification for arc length correction (S3)
For activation, put signal to reference potential 0 V (pin E)
U/V
Output
Supply voltage push/pull welding torch
Содержание Phoenix 401 Progress puls LP MM FKW
Страница 6: ...Contents Notes on the use of these operating instructions 6 099 005504 EW501 20 11 2015...
Страница 20: ...Machine description quick overview Rear view 20 099 005504 EW501 20 11 2015 4 2 Rear view Figure 4 2...
Страница 22: ...Machine description quick overview Inside view 22 099 005504 EW501 20 11 2015 4 3 Inside view Figure 4 3...
Страница 105: ...Appendix A JOB List 099 005504 EW501 20 11 2015 105 11 Appendix A 11 1 JOB List Figure 11 1...
Страница 106: ...Appendix B Overview of EWM branches 106 099 005504 EW501 20 11 2015 12 Appendix B 12 1 Overview of EWM branches...