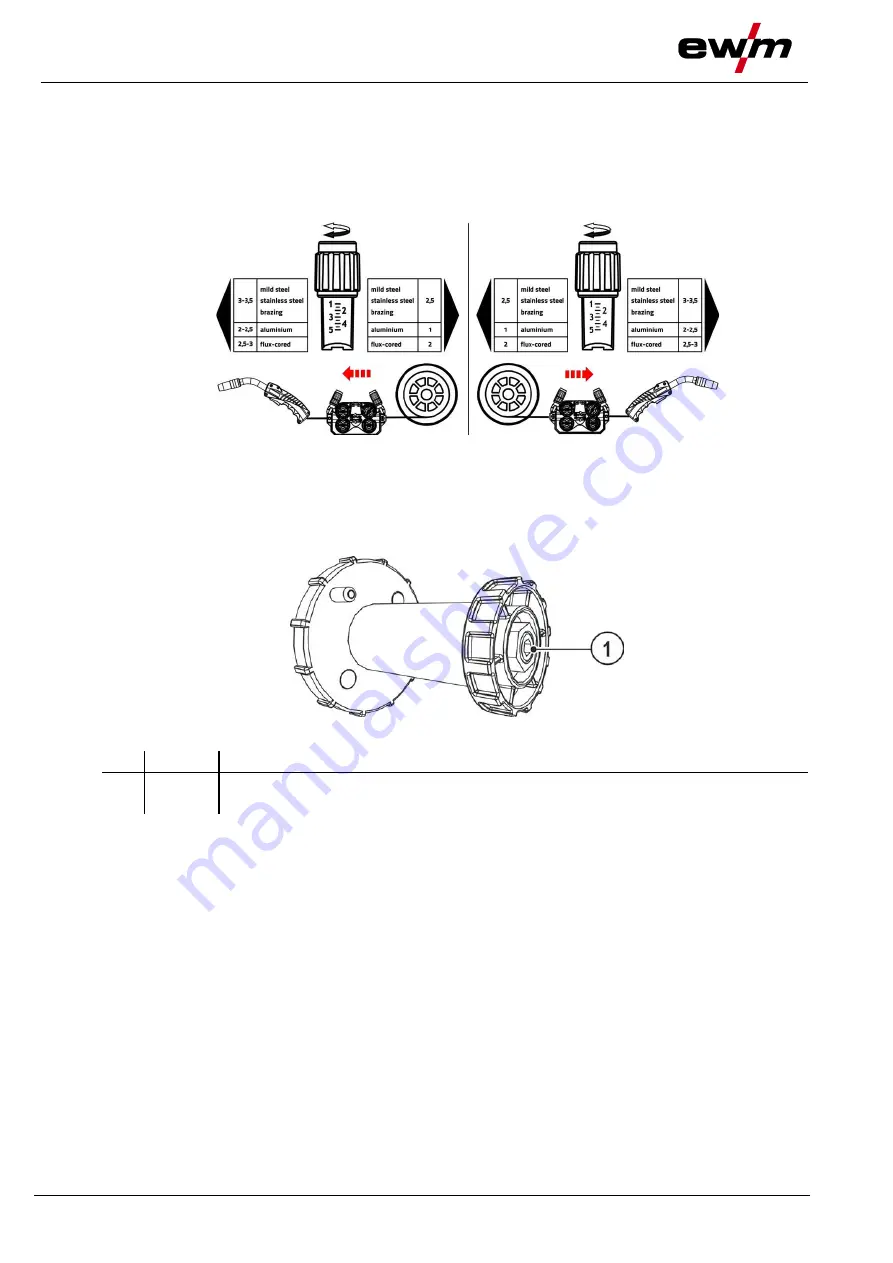
Design and function
MIG/MAG welding
30
099-005613-EW501
23.04.2019
A prerequisite for the automatic inching process is the correct preparation of the wire guide,
especially in the capillary and wire guide tube area > see 5.3.2 chapter.
•
The contact pressure has to be adjusted separately for each side (wire inlet/outlet) at the feed roll ten-
sioner setting nuts depending on the welding consumable used. A table with the setting values can be
found on a sticker near the wire drive.
Version 1: left hand mounting
Version 2: right hand mounting
Figure 5-15
Automatic inching stop
Touch the welding torch against the workpiece during inching. Inching of the welding wire will stop as
soon it touches the workpiece.
5.3.3.4 Spool brake setting
Figure 5-16
Item Symbol
Description
0
1
Allen screw
Securing the wire spool retainer and adjustment of the spool brake
•
Tighten the Allen screw (8 mm) in the clockwise direction to increase the braking effect.
Tighten the spool brake until the wire spool no longer turns when the wire feed motor stops but
without it jamming during operation!