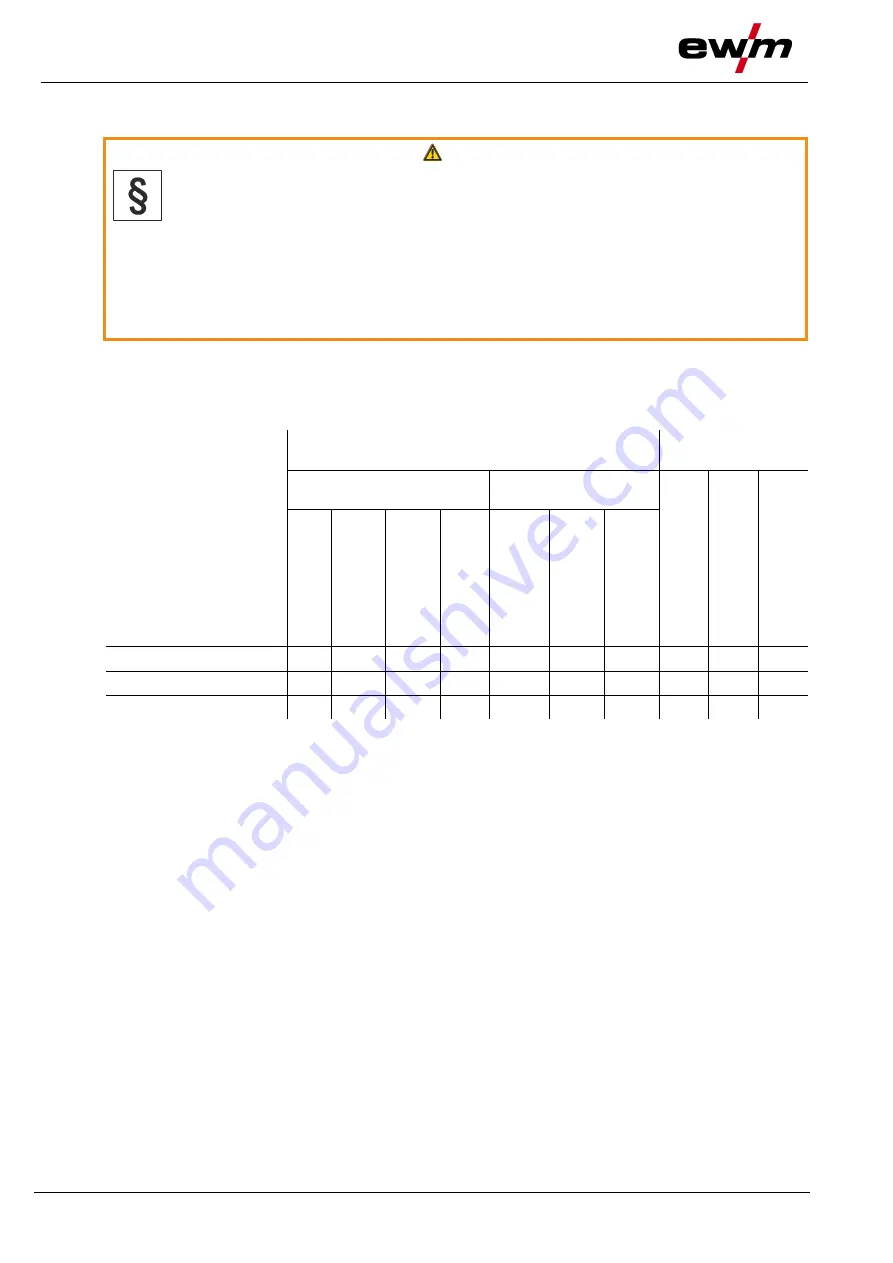
Intended use
Applications
14
099-005402-EW501
24.11.2016
3
Intended use
WARNING
Hazards due to improper usage!
The machine has been constructed to the state of the art and any regulations and
standards applicable for use in industry and trade. It may only be used for the welding
procedures indicated at the rating plate. Hazards may arise for persons, animals and
material objects if the equipment is not used correctly. No liability is accepted for any
damages arising from improper usage!
• The equipment must only be used in line with its designated purpose and by trained or
expert personnel!
• Do not improperly modify or convert the equipment!
Arc welding machine for standard and pulsed gas-shielded metal-arc welding with TIG welding and lift arc
(touch starting) or MMA welding as secondary process. It may be possible to expand the functionality by
using accessories (see the documentation in the relevant chapter).
3.1
Applications
Machine series
Main process
Secondary
process
Standard MIG/MAG
welding
Pulsed MIG/MAG
welding
TIG
we
ldin
g (
lif
t
ar
c)
MMA
weldin
g
Goug
ing
forc
eA
rc
ro
otA
rc
co
ldA
rc
pipeSolutio
n
forc
eA
rc puls
ro
otA
rc pul
s
co
ldA
rc
p
uls
alpha Q puls MM
Phoenix puls MM
Taurus Synergic S MM
possible
not possible
Содержание alpha Q 330 Progress puls MM TKM
Страница 18: ...Machine description quick overview Rear view 18 099 005402 EW501 24 11 2016 4 2 Rear view Figure 4 2...
Страница 20: ...Machine description quick overview Inside view 20 099 005402 EW501 24 11 2016 4 3 Inside view Figure 4 3...
Страница 128: ...Appendix B Overview of EWM branches 128 099 005402 EW501 24 11 2016 12 Appendix B 12 1 Overview of EWM branches...