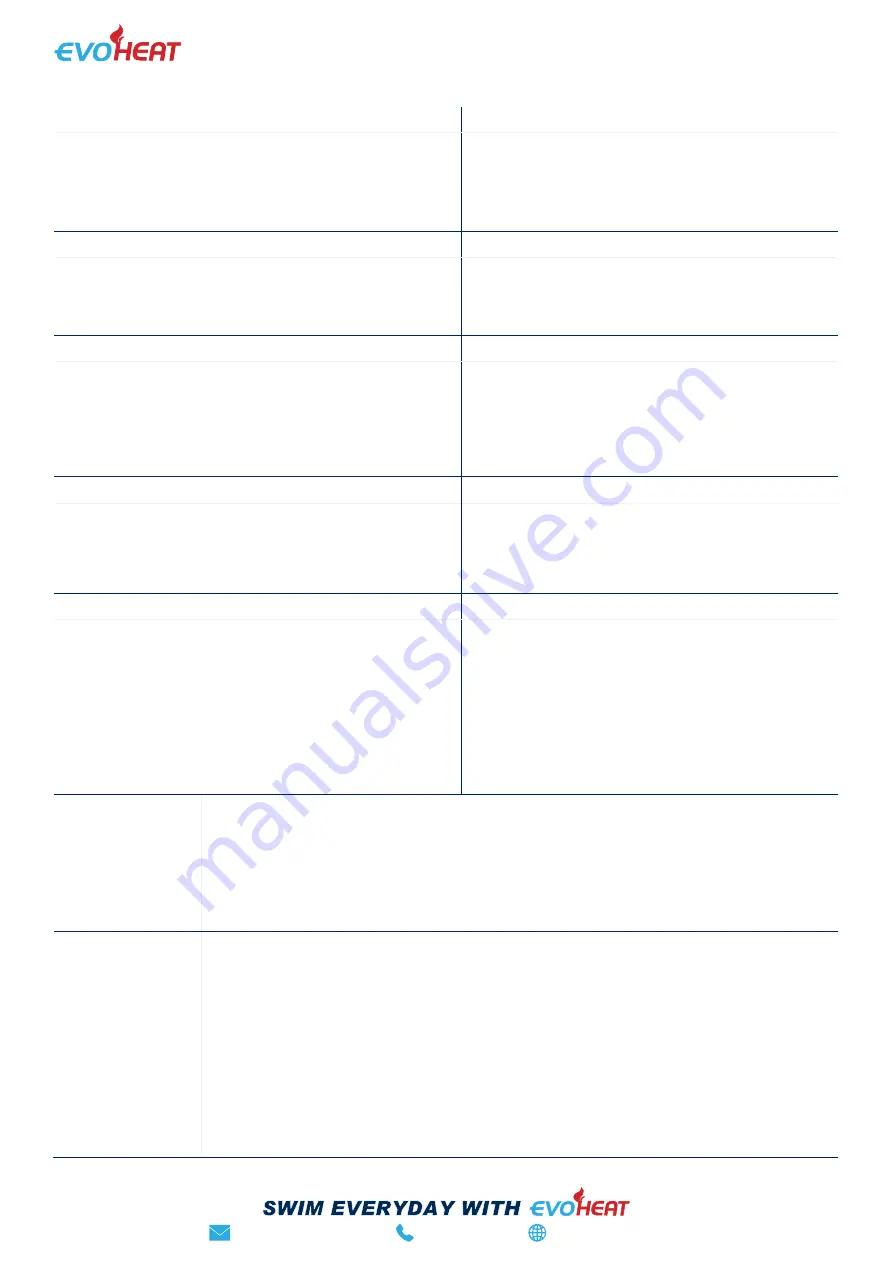
1300 859 933
www.evoheat.com.au
CS-i Series Manual
Page 23
8.3 Advanced
CHECK THE AREA
GENERAL WORK AREA
Prior to beginning work on systems containing flammable
refrigerants, safety checks are necessary to ensure that the risk
of ignition is minimised. For repair to the refrigerating system, the
following precautions shall be complied with prior to conducting
work on the system. prolonged period of no usage.
All maintenance staff and others working in the local area
shall be instructed on the nature of work being carried out.
Work in confined spaces shall be avoided. The area around
the workspace shall be sectioned off. Ensure that the
conditions within the area have been made safe by control
of flammable material.
PRESENCE OF FIRE EXTINGUISHER
WORK PROCEDURES
If any hot work is to be conducted on the refrigeration equipment
or any associated parts, appropriate fire extinguishing equipment
shall be available to hand. Have a dry powder or CO2 fire
extinguisher adjacent to the charging
Work shall be undertaken under a controlled procedure to
minimise the risk of a flammable gas or vapour being
present while the work is being performed.
CHECKING FOR PRESENCE OF REFRIGERANT
VENTILATED AREA
The area shall be checked with an appropriate refrigerant
detector prior to and during work, to ensure the technician is
aware of potentially flammable atmospheres. Ensure that the
leak detection equipment being used is suitable for use with
flammable refrigerants, i.e. non-sparking, adequately sealed or
intrinsically safe.
Ensure that the area is in the open or that it is adequately
ventilated before breaking into the system or conducting any
hot work. A degree of ventilation shall continue during the
period that the work is carried out. The ventilation should
safely disperse any released refrigerant and preferably
expel it externally into the atmosphere. prolonged period of
no usage.
CABLING
DETECTION OF FLAMMABLE REFRIGERANTS
Check that cabling will not be subject to wear, corrosion,
excessive pressure, vibration, sharp edges or any other adverse
environmental effects. The check shall also consider the effects
of aging or continual vibration from sources such as compressors
or fans.
Under no circumstances shall potential sources of ignition
be used in the searching for or detection of refrigerant leaks.
A halide torch (or any other detector using a naked flame)
shall not be used.
REPAIR TO INTRINSICALLY SAFE COMPONENTS
LABELLING
Do not apply any permanent inductive or capacitance loads to
the circuit without ensuring that this will not exceed the
permissible voltage and current permitted for the equipment in
use.
Intrinsically safe components are the only types that can be
worked on while live in the presence of a flammable atmosphere.
The test apparatus shall be at the correct rating. Replace
components only with parts specified by the manufacturer. Other
parts may result in the ignition of refrigerant in the atmosphere
from a leak.
Equipment shall be labelled stating that it has been de-
commissioned and emptied of refrigerant. The label shall be
dated and signed. Ensure that there are labels on the
equipment stating the equipment contains flammable
refrigerant.
NO IGNITION
SOURCES
No person carrying out work in relation to a refrigeration system which involves exposing any pipe work
that contains or has contained flammable refrigerant shall use any sources of ignition in such a manner
that it may lead to the risk of fire or explosion. All possible ignition sources, including cigarette smoking,
should be kept sufficiently far away from the site of installation, repairing, removing and disposal, during
which flammable refrigerant can possibly be released to the surrounding space. Prior to work taking
place, the area around the equipment is to be surveyed to make sure that there are no flammable
hazards or ignition risks. No Smoking signs shall be displayed.
CHARGING
PROCEDURES
In addition to conventional charging procedures, the following requirements shall be followed.
•
Ensure that contamination of different refrigerants does not occur when using charging
equipment. Hoses or lines shall be as short as possible to minimise the amount of refrigerant
contained in them.
•
Cylinders shall be kept upright.
•
Ensure that the refrigeration system is earthed prior to charging the system with refrigerant.
•
Label the system when charging is complete (if not already).
•
Extreme care shall be taken not to overfill the refrigeration system.
Prior to recharging the system, it shall be pressure tested with OFN. The system shall be leak tested on
completion of charging but prior to commissioning. A follow up leak test shall be carried out prior to
leaving the site. The safety wire model is 5*20_5A/250VAC, and must meet the explosion-proof
requirements.
Содержание CS-i 250
Страница 1: ......