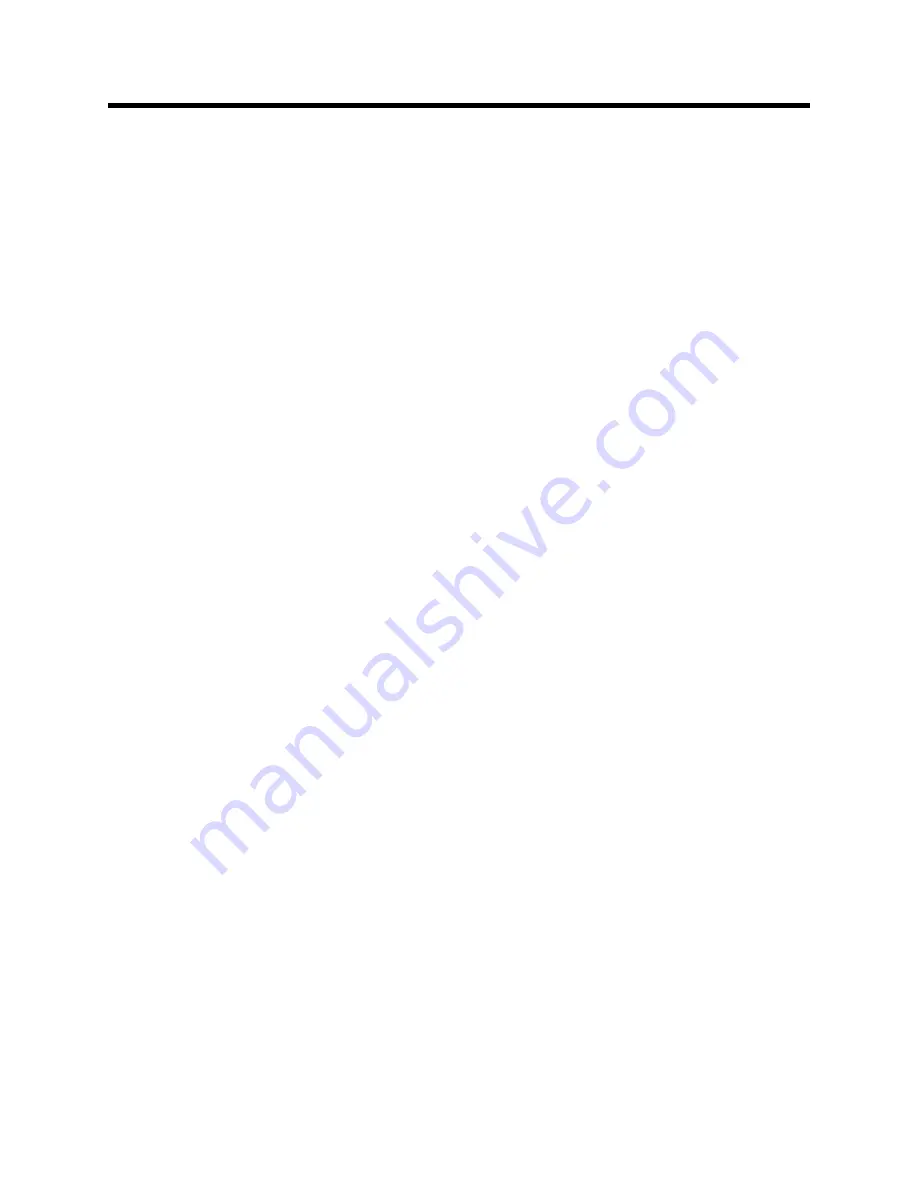
11
over
-
currents internally and limits amp draw from the
power source, it also helps to improve arc termina-
tion. When converting over from a transformer a
welder with a habit of stretching the arc too far may
find the arc will stop suddenly. Constant Current
Inverters operate on somewhat different principles
than Constant Current transformers so some retrain-
ing and even rethinking may be necessary by welders
who have developed an exaggerated motion using a
transformer welder. A practical example is during
the whipping motion required when welding E6010.
If the welder is accustomed to exaggerating the whip-
ping motion required, then the arc may go out. This
usually happens when the tip of the rod is flipped too
far up vertically at the end of the
“
whip
”
and raises
the tip up further than necessary. This can be simply
avoided if the rod is stepped out further in front of
the puddle with less flipping up to draw out the arc.
2.2 Basic Overview and operation.
Package:
The PowerARC 300ST includes a stick electrode holder
with cable, and a work clamp with cable. Cables are
approximately 10 ft. in length. Longer cables can be
added to electrode holder, work clamp and connect-
ors. This unit does not include TIG torch or regulator.
Stick:
The stick function is fairly simple and straight forward.
Arc striking can be done quite easily with practice and
the hot start reduces sticking. As with any type of
welding, this takes practice. Be sure to double check
that the electrode holder cable is located in the posi-
tive terminal, and the work clamp is located in one of
the negative terminals. See page 17 for arc striking
technique and general rod size selection. Using too
much hot start or arc force control can result in burn
through. Using too little will result in poor arc perfor-
mance and rod sticking.
TIG:
Although the PA 300ST is sold as a DC Stick welder, the
unit can be used as a lift
-
start DC TIG welder for weld-
ing most all metals
except
aluminum and magnesium.
The unit though does not provide a HF circuit, foot
pedal or torch switch for starting the arc, so a lift start
method must be used to strike the arc.
Note:
The
torch will always be powered. Avoid touching the
tungsten to the metal until ready to weld. When using
for lift TIG, be sure to turn the arc force and hot start
controls to the minimum setting. Contact Everlast for
an optional TIG package if desired, or source one local-
ly at a nearby welding supply store.
2.3 Handling and general maintenance
.
Duty Cycle and Overcurrent:
Be careful to observe the duty cycle of the welder.
Overheating may occur if the duty cycle is exceeded.
Overheating will cause the unit safety cutout to en-
gage, subsequently interrupting output. Allow the unit
to rest while remaining switched on for 10 –
15
minutes
if the safety cut out has triggered. After that, reset the
unit by cycling the main power switch on the rear.
High heat and humid conditions will also affect the
duty cycle of the welder. If the unit overheats or an
overcurrent condition is experienced, the duty cycle
light will light as well. Welding will resume once the
duty cycle light is cleared after resting and cycling the
power switch. An over current or under current condi-
tion is usually caused by dirty power conditions, over/
under voltage power supply or an internal fault. If the
overcurrent light is lit, turn the machine off and check
for wiring faults, then turn the unit back on to see if
the light has cleared. If it does not clear, contact Ever-
last technical support for further instruction.
The unit
should be stored in a dry place for long term storage.
Humid/wet conditions can contribute to the eventual
decay of the circuitry in the machine. For safety rea-
sons, do not use this machine directly in the rain or
with soaked clothing or damp protective gear. The
service rating for this unit is IP21S, and is not designed
for wet environment use.
Make sure that the unit
’
s cooling fan and exhaust
vents are kept free of obstruction.
Before every oper-
ation, inspect unit for unexpected obstructions such as
insect and vermin nests. Once a month, or as needed,
clean the machine thoroughly inside and out with com-
pressed air.
Before removing the covers however, un-
plug the welder for 30 minutes to allow the internal
capacitors to discharge to prevent shock, injury and
even death.
Afterwards, open the units by removing
the rear plastic cover and the metal cover only. Do not
remove the front cover. Do not remove circuit boards
unless authorized. Check all plugs and connections for
tightness before replacing the covers. Do not pinch
any wires when reinstalling the covers. Wear safety
glasses/goggles to prevent eye injury from flying parti-
cles that may get dislodged while cleaning with com-
pressed air. Do not concentrate compressed air on the
skin or serious injury may occur.
GENERAL SETUP AND OPERATION
Section 2