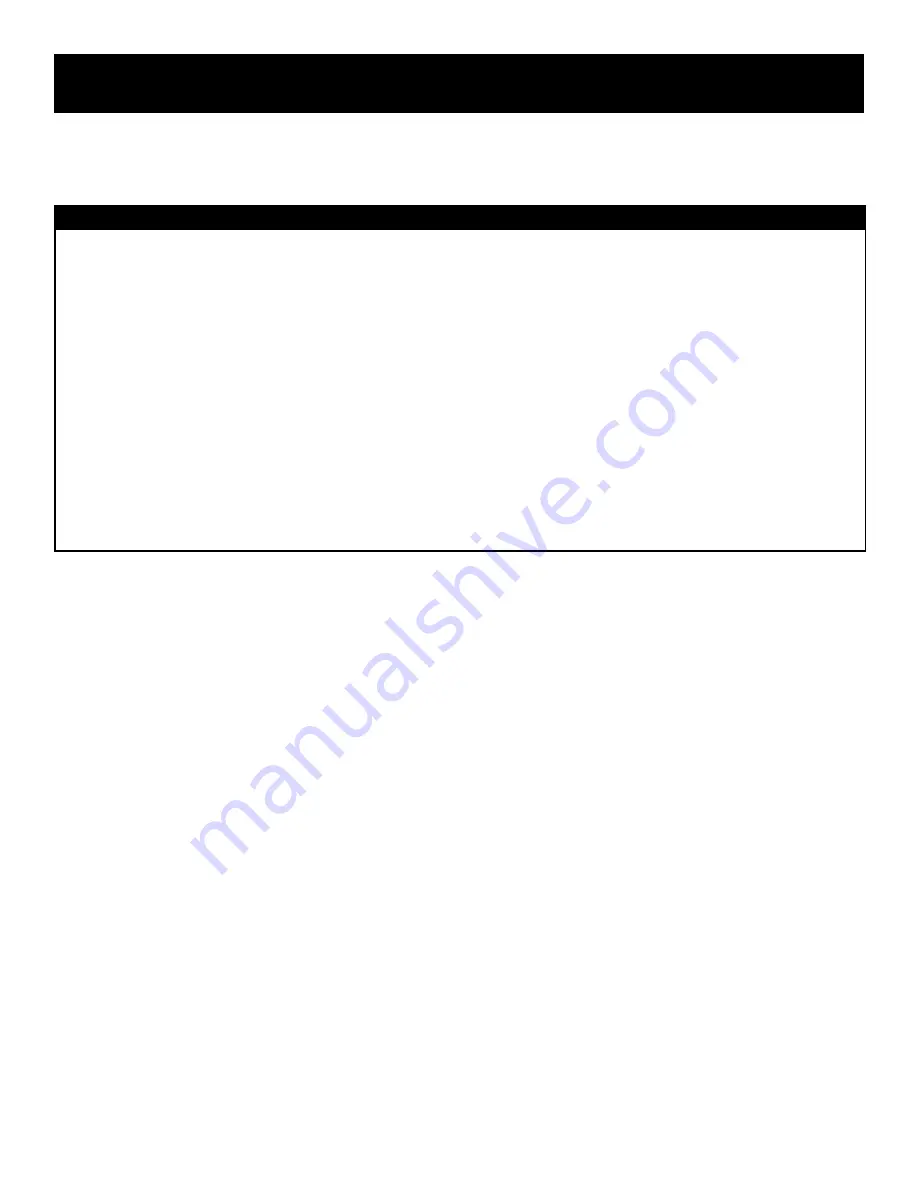
32
Troubleshooting
Common Welding Issues
NO.
Trouble
Possible Cause
Solution
1.
Unit is switched on, but the power light isn
’
t on.
Switch damaged.
Service Breaker/ Input Line Damaged
Check.
Replace.
2.
After welding machine is overheating and the fan
does not work.
Fan damaged.
Fan connector plus is loose
Replace.
Check. Reinstall.
4.
Intermittent, wandering arc.
Work Clamp not connected directly to part being
welded.
Work Clamp worn/damaged
Torch height too high.
Reconnect.
Replace.
Reduce MIG torch height to under
3/8”.
5.
Porosity of the Weld. Discolored weld color.
Tungsten is discolored.
Low flow rate of shielding gas. High flow rate of
shielding gas. Possible gas leaks internally or
externally due to loose fittings. Base metal is
contaminated with dirt or grease.
Increase flow rate on regulator. Check for kinks in tubing. Increase post
-
flow
time. Reduce stick
-
out to less than
1/4”.
Increase gas nozzle size. Clean
metal thoroughly with approved metal cleaner, or use acetone and a rag to
clean metal.
6.
Weld quality is poor.
Weld is dirty/oxidized, or porous.
Drafty conditions. The welder is located on the
workpiece and is blowing gas off due to fan
activity. Solenoid is sticking.
Eliminate drafts. Move welder. Check if there is sufficient shielding gas left
in tank. Check gas flow. Adjust for higher flow of gas. Listen for audible click
of gas solenoid. If no click is heard, then contact Everlast Support. Clean
weld properly. Increase pre flow or post flow.
7.
Unstable Arc. Spatter.
Bad work clamp connection. Metal is indirectly
connected through table or other item. Incorrect
settings
Change Work Clamp. Use a direct connection to the part being welded.
Check and adjust settings. Spatter usually increases when smaller wires are at
the maximum welding capacity.
8.
Other.
Contact Everlast
Содержание Cyclone 200E
Страница 33: ...33 ...