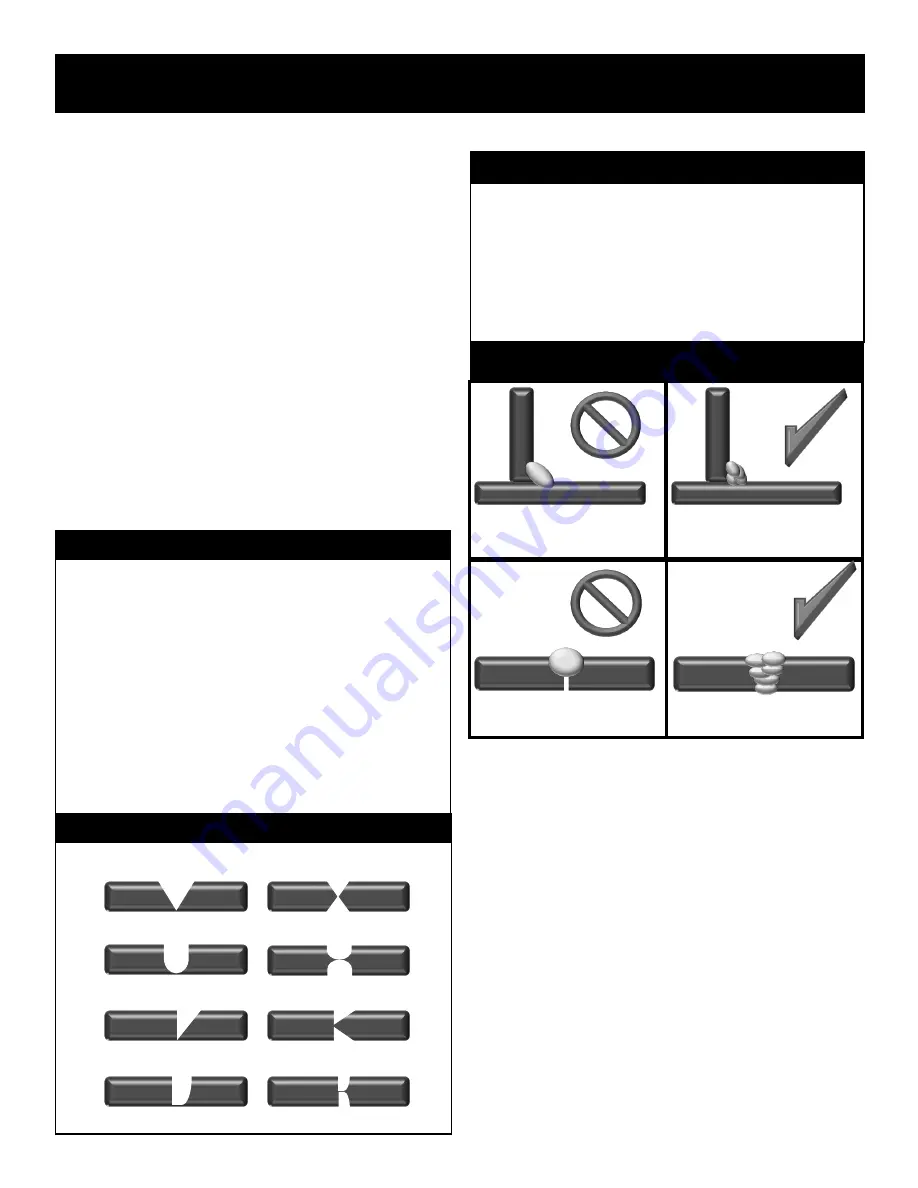
29
COMPONENT IDENTIFICATION AND FUNCTION
Welding Information and Tips
dling. A thick pass may also begin to cool before contaminates and gas
pockets have the time to float out to the surface. It
’
s far better to make
multiple smaller passes to complete a plate weld for a higher quality result.
For best results, this requires that most joints
1/4”
and over be prepared
with a grinder to accept multiple weld passes. The weldment edges
should be ground to form a V, U or J shaped groove to create a recess
where the welds can be welded one on top of another. For welding
with
.035”
wire and under, create a bead no thicker than
3/16”
in a single
pass, no more than
1/8”
with
.030”
wire, and with
.025”
wire and smaller no
more than 3/32 for best results. This will help maintain proper fluidity of
the weld and prevent gas from being trapped in the weld and give time for
any minor contaminates to float out of the weld. It will also help to main-
tain reasonable forward travel speeds. Too slow of travel speeds will
create excess build up and can tend to create cold lap at the weld toes
resulting in poor tie in. One issue created with a weaving technique even
if the metal deposited is the correct thickness is that it can slow the for-
ward progress down. If weaving is too wide, one side of the puddle will
cool and oxidize before the torch is brought back across to that side. This
is a point where porosity can be introduced.
Joint Preparation
DOUBLE J
-
GROOVE
V
-
GROOVE (60
-
80°)
DOUBLE V
-
GROOVE
DOUBLE U
-
GROOVE
U
-
GROOVE
BEVEL GROOVE
DOUBLE BEVEL GROOVE
J
-
GROOVE
What Are the Different Kinds of Welds?
Besides a butt joint (Flat edge to flat edge) and lap joint (overlapping
edges) which are often used for thinner metal gauges, consider using
one of these groove joints for best welding results. When grinding or
cutting the bevels, especially with a single V
-
groove, it may be beneficial
to leave a small land with a gap between the joint to achieve full penetra-
tion. In this case a temporary backer plate can be used to support the
bottom of the weld to create the root pass. The root weld will weld the
backer to the main plate. This backer can later be ground or cut off.
However, in many cases a plain open root can be used as a backer plate
adds to the time and labor involved. A knife edge is also acceptable so
long as the joint is fully penetrated when the weld is completed. Open
root gaps without a backer can range from
1/16”
to
1/8”
depending upon
wire diameter and application.
When Do I Use Multi
-
Pass Welds?
When welding material
1/4”
and over be careful about trying to put too
much metal down in a single pass. Use multiple passes to complete the
weld along with any necessary joint preparation especially with wires of
smaller diameter. As metal thickness goes up so does the number of
required passes. Depending upon the wire diameter and power settings
used, a
1/4”
joint may only require 1 or 2 passes, but a
3/8”
joint in
plate metal or pipe will require not only beveling but 4 to 6 overlapping
weld passes including a cap and root pass. See Example below.
≥
1/4”
Fillet
≥
1/4”
Fillet
s
≥
1/4”
V
≥
1/4”
Butt
Weld Pass Examples
Содержание Cyclone 200E
Страница 33: ...33 ...