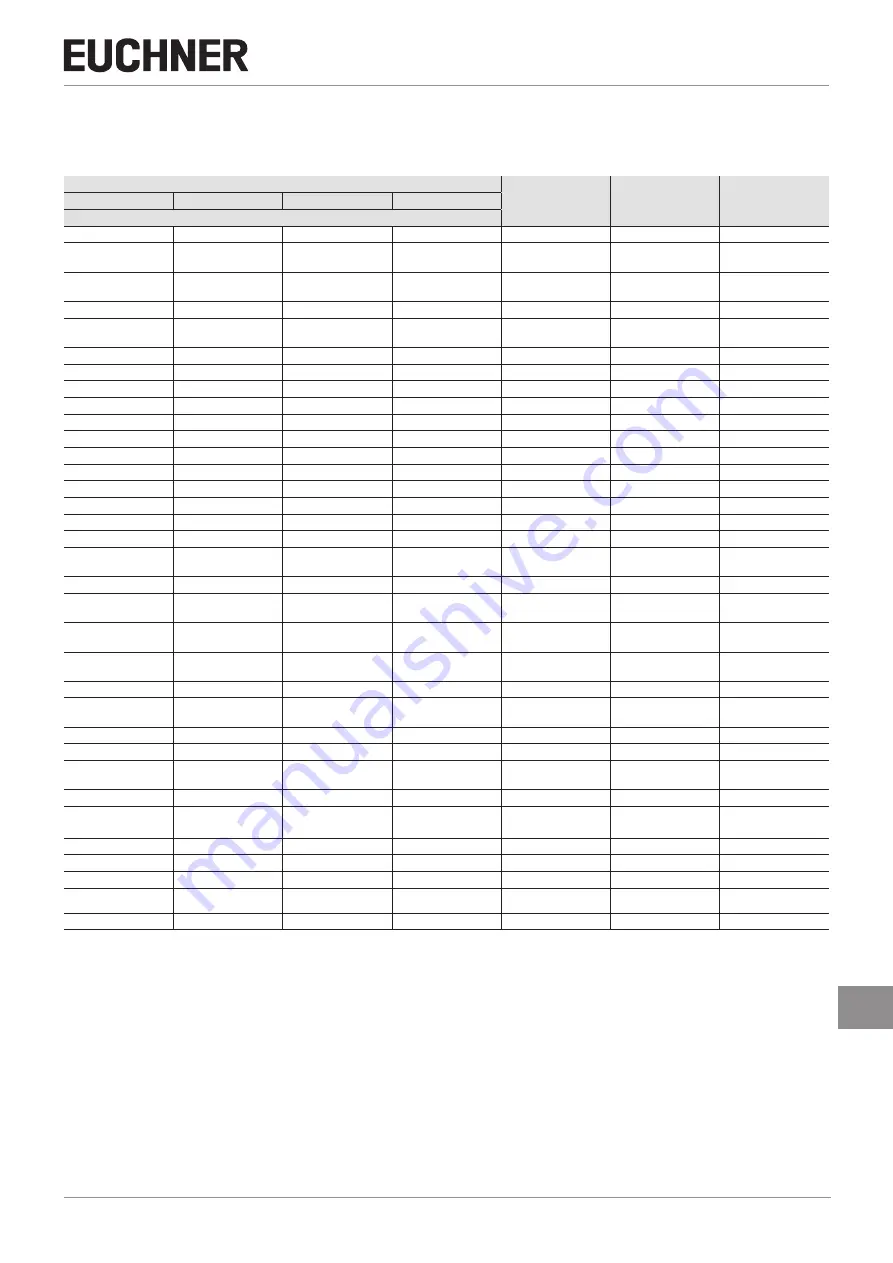
21
2510145-05-08/21 (translation of the original operating instructions)
Operating Instructions
Non-Contact Safety Switch CES-I-BR-.-C07-…
EN
11.3.2. Acyclical data (device data and events)
Table 3: Acyclical data (examples)
Command
Answer
(number of bytes)
Category
Use in device
classes
Dez
Bin
Hex
Meaning
General information
1
1
1
2
10
2
Send device ID-number/
serial number
6
PWR-UP
All
3
11
3
Send device Versions
number
5
PWR-UP
All
4
100
4
5
101
5
Complete number of
participants
2
PWR-UP
All
6
110
6
7
111
7
8
1000
8
9
1001
9
10
1010
A
11
1011
B
12
1100
C
13
1101
D
14
1110
E
15
1111
F
16
10000
10
17
10001
11
18
10010
12
Send current error
code
1
Error
All
19
10011
13
Send last error code
1
Error
All
20
10100
14
Request of size of
error log
1
Error
All
21
10101
15
Send error with
number
1
Error
All
22
10110
16
Send detected tag
code
5
Transponder
All
23
010111
17
Send taught tag code
5
Transponder
All
24
011000
18
Send blocked tag
code 1
5
Transponder
All
25
011001
19
Voltage (Power supply)
2
Additional
All
26
011010
1A
Temperature
1)
1
Additional
All
27
011011
1B
Number of switching
cycles (Door position)
3
Additional
All
28
011100
1C
29
011101
1D
Reset device (Soft-
Reset)
2)
1
Reset
All
30
011110
1E
Factory reset
1
Reset
All
31
011111
1F
32
100000
20
.
.
.
.
.
.
.
.
.
63
111111
3F
1) The read value is the internal operating temperature in the switch. This value can exceed the ambient temperature. The device enters the fault state when the internal operating temperature exceeds
80 °C.
2) Each BR switch must be addressed individually in a BR switch chain.
For more information on these and other acyclical data, refer to the operating instructions for your BR/IO-Link Gateway.