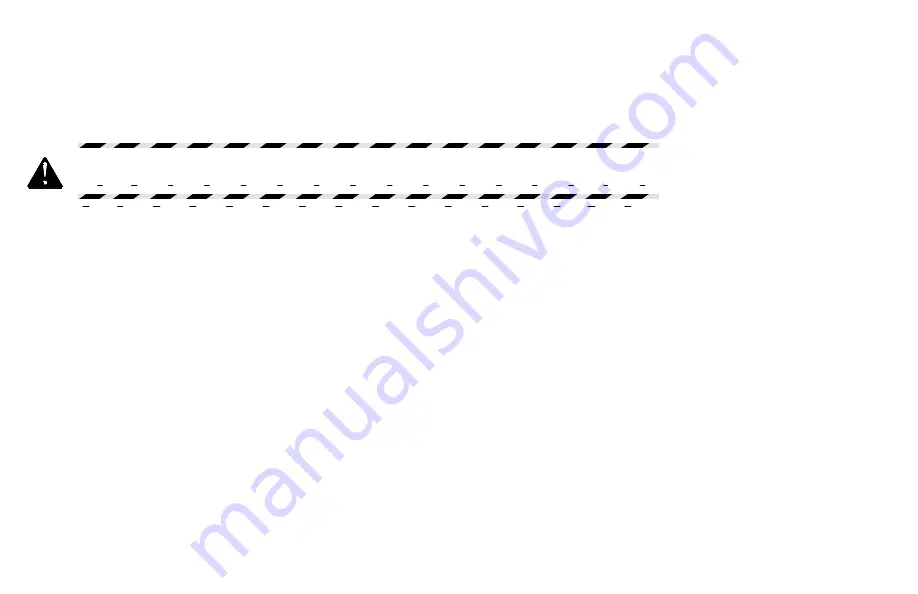
45-2 Preparing the Winch and Work Area
HG12 Winch
Wire Rope Failure
Wire rope will break if abused or misused. Failure is usually cumulative. A wire rope that almost fails under a heavy load can fail
under a lighter load on the next pull.
DANGER: Wire rope whip lash can be fatal. Be sure the wire rope is in good condition
and that it is securely attached to the load.
When it breaks, wire rope will whip or lash because of the sudden release of tension on the wire rope. The wire rope can also whip
or lash if it is suddenly pulled loose from its load. Be sure the wire rope is securely attached to its load.
Содержание Hammerhead HG12
Страница 6: ...This page intentionally left blank ...
Страница 16: ...This page intentionally left blank ...
Страница 24: ...This page intentionally left blank ...
Страница 26: ...15 2 Safety Decals HG12 Winch ...
Страница 27: ...HG12 Winch Safety Decals 15 3 ...
Страница 28: ...15 4 Safety Decals HG12 Winch ...
Страница 30: ...This page intentionally left blank ...
Страница 40: ...25 10 Controls HG12 Winch ...
Страница 46: ...This page intentionally left blank ...
Страница 50: ...This page intentionally left blank ...
Страница 80: ...This page intentionally left blank ...
Страница 92: ...This page intentionally left blank ...
Страница 106: ...This page intentionally left blank ...
Страница 108: ......