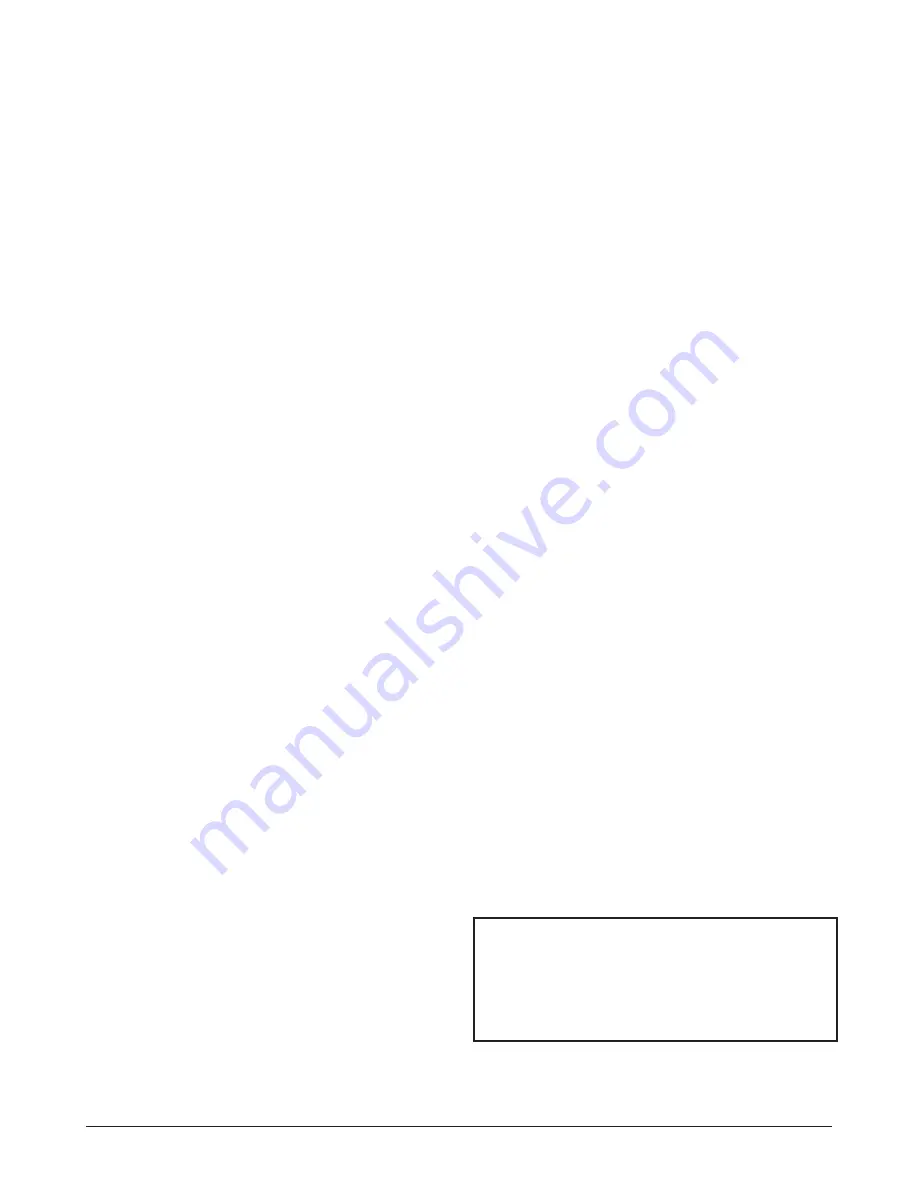
4
user manual LokPilot V2.0 / LokPilot DCC V2.0 01/2005
Prior to installation
The locomotive must be in perfect technical condition
prior to installation. Only a locomotive with a trouble-
free mechanism and smooth running properties in
analogue mode should be converted for digital mode.
Wear and tear parts, such as motor brushes, wheel
contacts, light bulbs, etc. must be inspected and
cleaned or replaced if necessary.
All work has to be carried out with the locomotive
placed on a suitable base (not the track) and definitely
un-powered. Make sure there can never be any
electrical power applied to the loco during the
conversion – even inadvertently.
Locomotives with DCC Interface
The LokPilotDCC is equipped with an interface as per
NEM 650/652 (NMRA page 9.1/9.2 - see fig. 1). In-
stallation in locomotives with interface is therefore
particularly easy:
• Remove the body from the chassis. Please refer to
the instructions provided with your locomotive!
• Remove the plug from the DCC socket. Please keep
it for later use.
•Insert the plug in such a way that pin 1 of the plug
(near the red / orange wires) is located next to the
point marked *, +, . or 1. Please take care to avoid
bending the pins. Do not rely on the assumption
that the wires have to lead from the socket in a
certain direction: only the position of pin 1
determines which way the plug has to be inserted.
• Locate the decoder at a suitable position within the
locomotive. Most modern models have sufficient
space for a decoder. Use double sided adhesive
tape or a small amount of hot glue.
Locomotives without interface
First separate all wires in the locomotive and make
sure there is no hidden connection from one of the
motor terminals to the chassis or the wheel contacts.
The motor terminals definitely must be insulated.
Fleischmann models often have such a connection,
which can easily be overlooked. Check all connections
using an Ohmmeter and make sure there are no short
circuits between the motor terminals and the wheel
contacts.
How to proceed depends on how the headlights and
other functions are wired:
a) If directional headlights and functions are isolated
from the locomotive body proceed as per figure 2.
b) Directional headlights and functions may be
connected with their common to the track voltage
(e.g. almost all Maerklin® -locomotives and older
Fleischmann or ROCO locomotives are wired like
that) as per figure 3.
• Connect the red wire to the right rail pickup (or
centre pick up in AC models),
• and the black wire to the left rail pickup (wheels in
AC models).
• Connect the orange wire with the motor terminal,
which was originally wired to the right wheel pick
up (centre pick up in AC models).
• The grey wire goes to the terminal, which was
originally connected to the left rail (common rails
for AC models).
• Solder the back up lights to the yellow wire, the
front headlights to the white wire.
• Connect the green wire to the function output,
which you want to switch with function button F1.
• Connect the purple wire with the function output,
which you want to switch with the function button
F2.
If your locomotive is wired as per b) above, then wiring
is completed.
In the case as per fig. 2 you have to connect the
second pole of all light bulbs or other loads to the
blue wire. The blue wire must not be connected to
the chassis!
Connecting Auxiliary Functions
Any load may be connected to the light and
function outputs as long as it doesn’t exceed the
maximum current. Please note that the overload
protection of the decoder responds very quickly
and will switch off all functions immediately in case
of overload or short circuit.
Therefore use only 16 V bulbs or higher and a
maximum nominal current of 50 mA:
Incandescent lamps have a high starting current
and this may activate the overload protection of
the decoder when the lights are switched on.