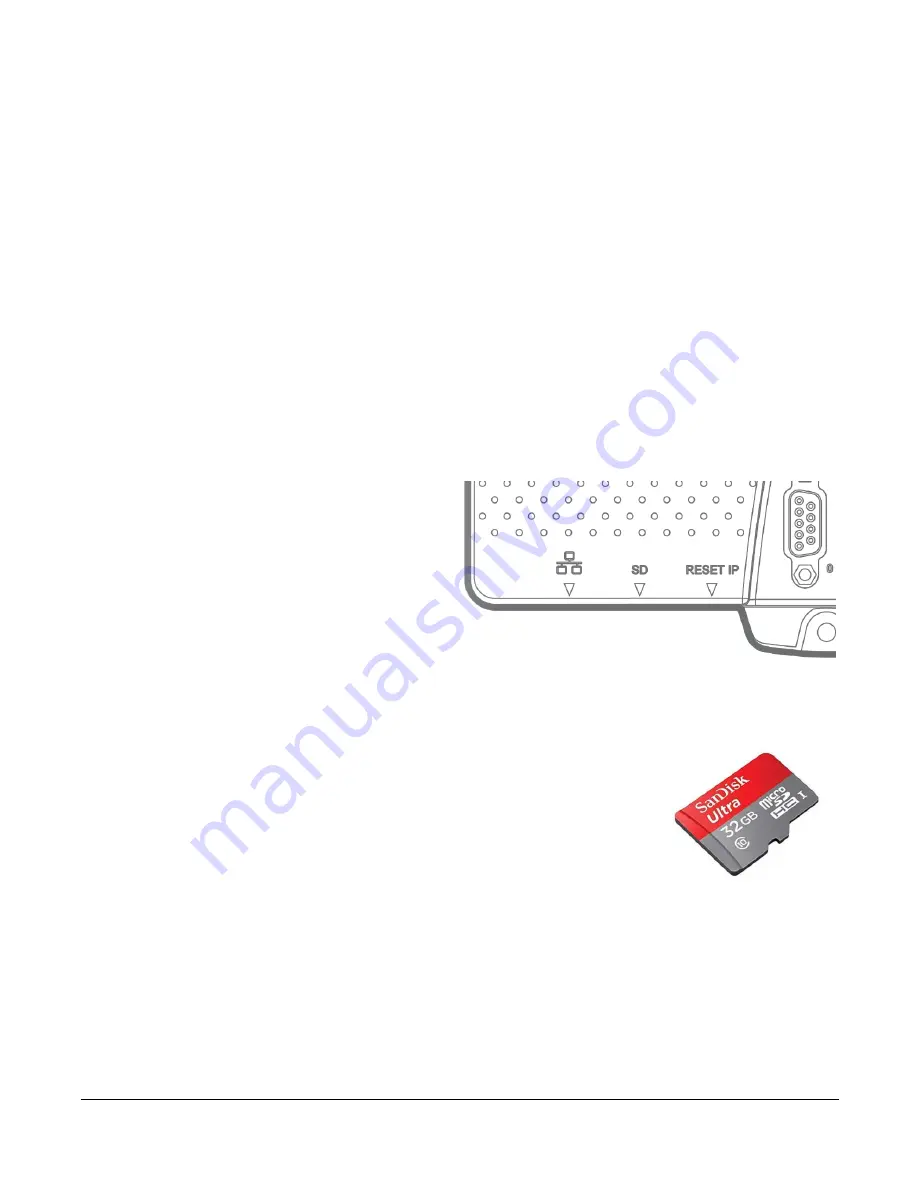
MC404-Z
Document Version: 1.05
© 2021 All rights reserved.
8
be defined to be used by the controller for end of travel limits, registration, datuming and
feedhold functions if required. The MC404-Z can have up to 512 external Input and Output
channels connected using DIN rail mounted CAN I/O modules. These units connect to the
built-in CANbus port.
Communications
A 10/100 base-T Ethernet port is fitted as standard and this is the primary communications
connection to the MC404-Z. Protocols supported include Telnet (Client and Server), Modbus
TCP (Client and Server), Ethernet IP (Client) and the TrioPCMotion DLL/ActiveX channel.
The MC404-Z has one built in RS232 port and one built in duplex RS485 channel for simple
factory communication systems. Either the RS232 port or the RS485 port may be configured
to run the Modbus or Hostlink protocol for PLC or HMI interfacing.
If the built-in CAN channel is not used for connecting I/O modules, it may optionally be used
for CAN communications. E.g. DeviceNet, CANopen etc.
IP Address reset
To reset the IP _ ADDRESS, IP _ GATEWAY
and IP _ NETMASK to their default values
press the IP reset button located next to
the SD card slot and power cycle the
controller while keeping the button
pressed.
The factory default IP address is
192.168.0.250. This can be changed using
the ETHERNET or IP_ADDRESS commands via
Motion Perfect.
Removable storage
The MC404-Z has a micro-SD Card slot which allows a simple means
of transferring programs, firmware and data without a PC
connection. Offering the OEM easy machine replication and servicing.
The memory slot is compatible with a wide range of micro-SD cards
up to 32 GBytes using the FAT32 compatible file system.
Axis positioning functions
The motion control generation software receives instructions to move an axis or axes from
the Motion-iX or IEC 61131-3 language which is running concurrently on the same processor.
The motion generation software provides control during operation to ensure smooth,
coordinated movements with the velocity profiled as specified by the controlling program.
Linear interpolation may be performed on groups of axes, and circular, helical or spherical
interpolation in any two/three orthogonal axes. Each axis may run independently, or they
may be linked using interpolation, electronic gearboxes and simple kinematics.