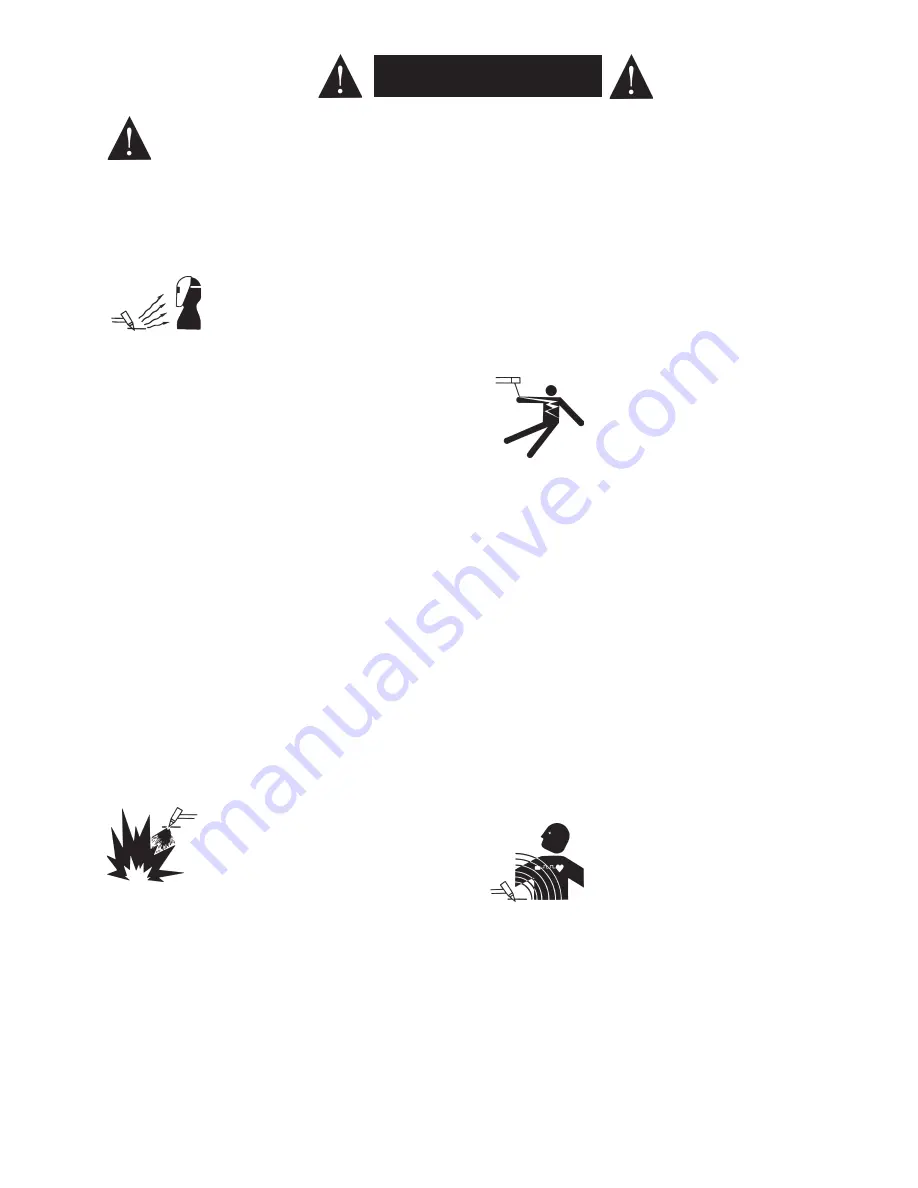
3
such as a garden hose, water pail, sand bucket, or
portable fire extinguisher. Be sure you are trained in its
use.
5. Do not use equipment beyond its ratings. For example,
overloaded welding cable can overheat and create a fire
hazard.
6. After completing operations, inspect the work area to
make certain there are no hot sparks or hot metal which
could cause a later fire. Use fire watchers when neces-
sary.
7. For additional information, refer to NFPA Standard 51B,
"Fire Prevention in Use of Cutting and Welding Pro-
cesses," available from the National Fire Protection Asso-
ciation, Batterymarch Park, Quincy, MA 02269.
ELECTRICAL SHOCK -- Contact can
cause severe injury or death. DO NOT
use AC output in damp areas, if move-
ment is confined, or if danger of falling
exists. Put on dry, hole-free gloves
before turning on the power. Also:
1.
Be sure the power source frame
(chassis) is connected to the ground system of the input
power.
2. Connect the workpiece to a good electrical ground.
3. Connect the work cable to the workpiece. A poor or
missing connection can expose the operator or others to
a fatal shock.
4. Use well-maintained equipment. Replace worn or dam-
aged cables.
5. Keep everything dry, including clothing, work area, cables,
torch/electrode holder and power source. Fix water leaks
immediately.
6. Make sure that you are well insulated, especially when
standing on metal or working in tight quarters or in a damp
area. Wear rubber-soled shoes and stand on a dry board
or insulating platform.
7. Turn off the power before removing your gloves.
8. Refer to ANSI/ASC Standard Z49.1 (see listing below) for
specific grounding recommendations. Do not mistake the
work lead for a ground cable.
ELECTRIC AND MAGNETIC FIELDS —
May be dangerous. Electric current flow-
ing through any conductor causes lo-
calized Electric and Magnetic Fields
(EMF). Welding and cutting current cre-
ates EMF around welding cables and
welding machines. Therefore:
1. Welders having pacemakers should consult their physi-
cian before welding. EMF may interfere with some pace-
makers.
2. Exposure to EMF may have other health effects which are
unknown.
3. Welders should use the following procedures to minimize
exposure to EMF:
A. Route the electrode and work cables together. Secure
them with tape when possible.
B. Never coil the torch or work cable around your body.
C. Do not place your body between the torch and work
cables. Route cables on the same side of your body.
WARNING:
T
hese Safety Precautions are for
your protection. They summarize precautionary
information from the references listed in Addi-
tional Safety Information section. Before per-
forming any installation or operating procedures, be sure to
read and follow the safety precautions listed below as well as
all other manuals, material safety data sheets, labels, etc.
Failure to observe Safety Precautions can result in injury or
death.
PROTECT YOURSELF AND OTHERS
-
-
Some welding, cutting, and gouging
processes are noisy and require ear
protection. The arc, like the sun, emits
ultraviolet (UV) and other radiation and
can injure skin and eyes. Hot metal can cause burns.
Training in the proper use of the processes and equip-
ment is essential to prevent accidents. Therefore:
1. Always wear safety glasses with side shields in any work
area, even if welding helmets, face shields, and goggles
are also required.
2. Use a face shield fitted with the correct filter and cover
plates to protect your eyes, face, neck, and ears from
sparks and rays of the arc when operating or observing
operations. WARN bystanders not to watch the arc and
not to expose themselves to the rays of the electric-arc or
hot metal.
3. Wear flameproof gauntlet type gloves, heavy long-sleeve
shirt, cuffless trousers, high-topped shoes, and a welding
helmet or cap for hair protection, to protect against arc
rays and hot sparks or hot metal. A flameproof apron may
also be desirable as protection against radiated heat and
sparks.
4. Hot sparks or metal can lodge in rolled up sleeves, trouser
cuffs, or pockets. Sleeves and collars should be kept
buttoned, and open pockets eliminated from the front of
clothing
5. Protect other personnel from arc rays and hot sparks with
a suitable non-flammable partition or curtains.
6. Use goggles over safety glasses when chipping slag or
grinding. Chipped slag may be hot and can fly far. By-
standers should also wear goggles over safety glasses.
FIRES AND EXPLOSIONS --
Heat from
flames and arcs can start fires. Hot
slag or sparks can also cause fires and
explosions. Therefore:
1. Remove all combustible materials well away from the
work area or cover the materials with a protective non-
flammable covering. Combustible materials include wood,
cloth, sawdust, liquid and gas fuels, solvents, paints and
coatings, paper, etc.
2. Hot sparks or hot metal can fall through cracks or crevices
in floors or wall openings and cause a hidden smoldering
fire or fires on the floor below. Make certain that such
openings are protected from hot sparks and metal.
3. Do not weld, cut or perform other hot work until the
workpiece has been completely cleaned so that there are
no substances on the workpiece which might produce
flammable or toxic vapors. Do not do hot work on closed
containers. They may explode.
4. Have fire extinguishing equipment handy for instant use,
SAFETY PRECAUTIONS
Содержание PCM-50i
Страница 24: ...24 Figure 5 2 PCM 50i Series A Wiring Diagram 380 415 V 3 Phase Input 35534...
Страница 30: ......
Страница 31: ......
Страница 32: ...F 15 269 8 95 1 5M Printed in U S A...