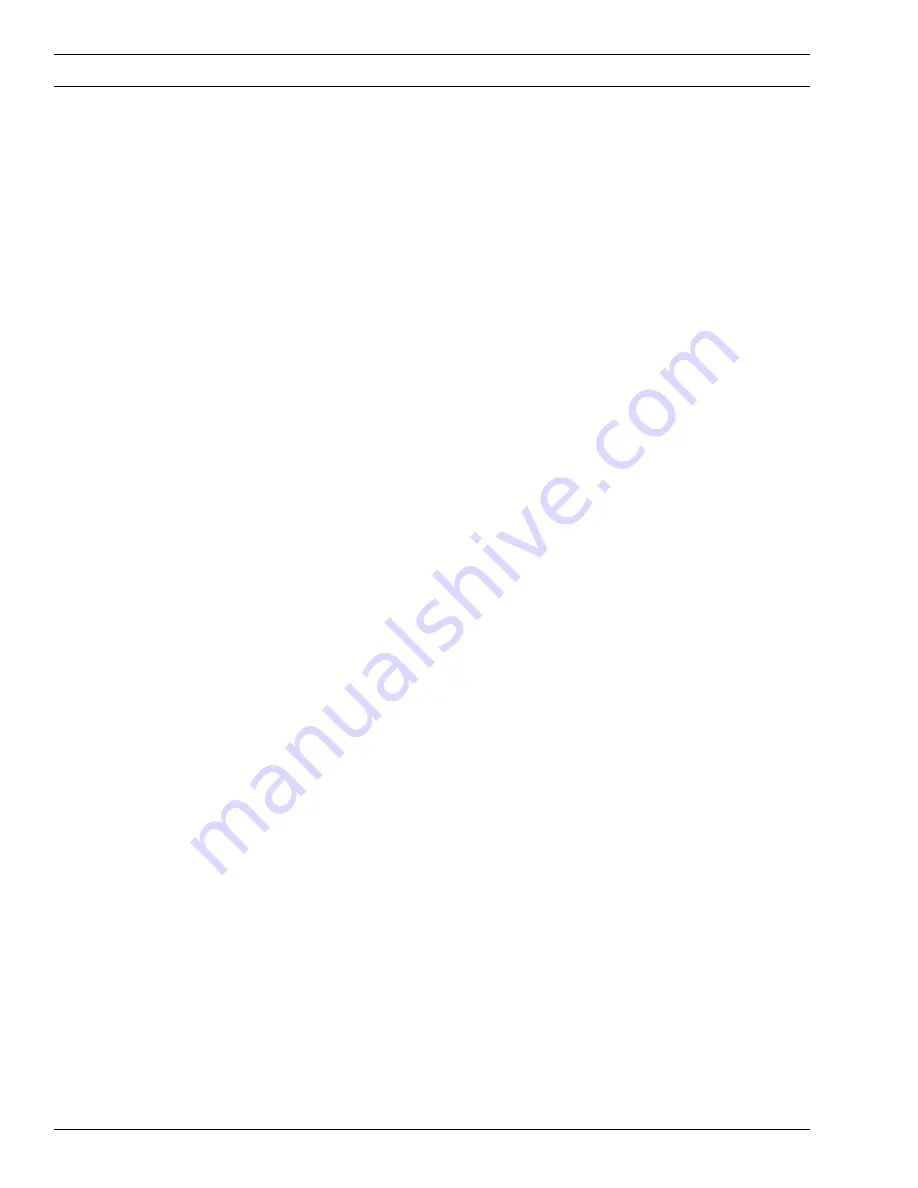
SECTION 3
OPERATION
18
2. Depress the torch switch. (Air and high frequency
should energize.)
3. Two seconds after depressing torch switch, the plasma
arc will start cutting. (If using the LOCK-IN mode,
torch switch can be released after establishing the
cutting arc.)
4. After starting the cut, the tip can be dragged along the
workpiece if cutting up to 1/4'’ thick material. When
cutting material greater than 1/4'’, maintain a 1/8'’ tip-
to-work (standoff) distance.
5. When ending a cut, the torch switch should be re-
leased (press and release if using LOCK-IN mode)
and lifted off the workpiece just before the end of the
cut to minimize double-arcing which can damage the
tip. This is to prevent high frequency from reigniting
after cutting arc extinguishes.
6. In the postflow mode, the arc can be restarted imme-
diately by depressing the torch switch. The two sec-
ond preflow will automatically cancel.
3.5 OPERATING TECHNIQUES
1. Piercing
- Materials (up to 1/4-in. thick) may be
pierced with the torch touching the work. When pierc-
ing thicker materials (up to 3/16-in. aluminum or 1/4-
in. stainless or carbon steel) immediately raise the
torch to 1/16-in. standoff after initiating the cutting arc.
This will reduce the chance of spatter from entering
the torch and prevent the possibility of welding the tip
to the plate. The torch should be angled at about 30
°
when starting to pierce, and then straightened after
accomplishing the pierce.
2. Grate Cutting
- For rapid restarts, such as grate or
heavy mesh cutting, do not release the torch switch.
This avoids the 2 second preflow portion of the cutting
cycle.
3.6 COMMON CUTTING PROBLEMS
Listed below are common cutting problems followed by
the probable cause of each. If problems are determined
to be caused by the PCM-500i, refer to the maintenance
section of this manual. If the problem is not corrected
after referring to the maintenance section, contact your
ESAB representative.
A.
Insufficient Penetration.
1.
Cutting speed too fast.
2.
Damaged cutting nozzle.
3.
Improper air pressure.
B.
Main Arc Extinguishes.
Cutting speed too slow.
C.
Dross Formation.
(In some materials and thick-
nesses, it may be impossible to get dross-free
cuts.)
1.
Cutting speed too fast or too slow.
2.
Improper air pressure.
3.
Faulty nozzle or electrode.
D.
Double Arcing.
(Damaged Nozzle Orifice.)
1.
Low air pressure.
2.
Damaged cutting nozzle.
3.
Loose cutting nozzle.
4.
Heavy spatter.
E.
Uneven Arc.
Damaged cutting nozzle or worn electrode.
F.
Unstable Cutting Conditions.
1.
Incorrect cutting speed.
2.
Loose cable or hose connections.
3.
Electrode and/or cutting nozzle in poor condi-
tion.
G.
Main Arc Does Not Strike.
Loose connections.
H.
Poor Consumable Life.
1.
Improper gas pressure.
2.
Contaminated air supply.
Содержание PCM-500i
Страница 28: ...28 D 36403 G Sheet 1 Figure 5 2 Wiring Diagram PCM 500i 200 230 Vac 50 60 Hz 1 Phase Sheet 1 ...
Страница 29: ...29 D 36403 G Sheet 2 Figure 5 2 Wiring Diagram PCM 500i 200 230 Vac 50 60 Hz 1 Phase Sheet 2 ...
Страница 30: ...30 D 36339 E Figure 5 3 Schematic Diagram PCM 500i 380 415 Vac 50 60 Hz 3 Phase ...
Страница 31: ...31 D 36524 E Sheet 1 Figure 5 4 Wiring Diagram PCM 500i 380 415 Vac 50 60 Hz 3 Phase Sheet 1 ...
Страница 32: ...32 D 36524 E Sheet 2 Figure 5 4 Wiring Diagram PCM 500i 380 415 Vac 50 60 Hz 3 Phase Sheet 2 ...