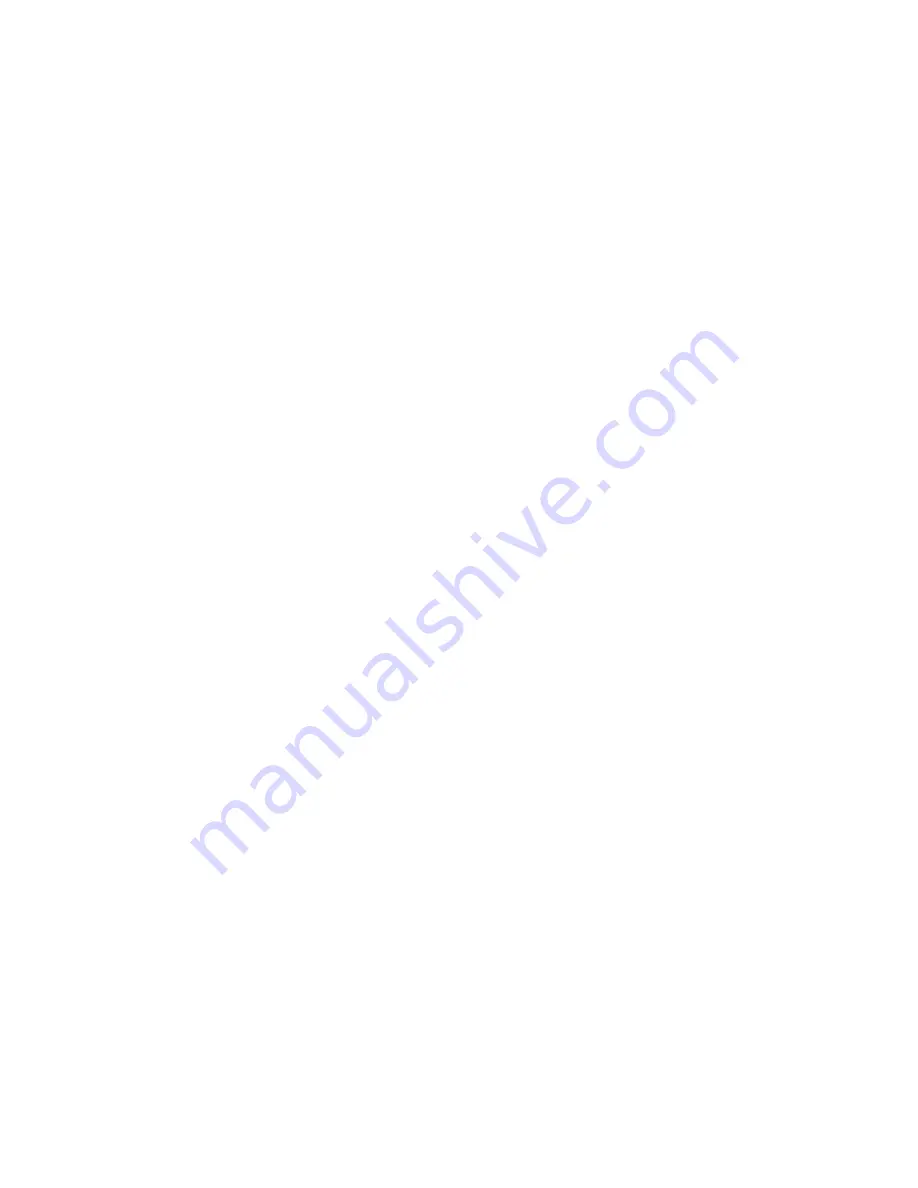
3
Lighting
Open the preheat oxygen valve on the torch a fraction
of a turn. Open the fuel gas valve on the torch about
two turns, and light the gas at the nozzle with a friction
lighter. DO NOT USE A MATCH. Then open the cutting
oxygen valve and adjust the preheat flames by open-
ing the preheat oxygen valve gradually. This will usu-
ally provide maximum preheat for the nozzle in use. If
the flames burn away from the end of the nozzle, or if
less preheat is desired, close the torch fuel gas valve
until the flame inner cones shorten noticeably, and then
readjust the flames with the preheat oxygen valve. Be
sure to keep the cutting oxygen valve open during any
adjustment of the preheat flames.
Shutting Off
Release the cutting oxygen valve lever. Then close the
fuel gas valve, and finally the preheat oxygen valve.
Operating Precautions
Backfire:
Improper operation of the torch may cause
the flames to go out with loud ‘pop’. Such a backfire
may be caused by contact of nozzle with the work, by
spatter from the work, by the use of incorrect gas pres-
sures, or by leakage at the cutting nozzle seats due to
dirt or nicks on seats or to a loose nozzle nut.
Flashback:
Under certain exceptional circumstances,
the flame may not ‘pop’ out (backfire) but instead burn
back inside the torch with a shrill hissing or squeal. This
is called a ‘flashback’. A flashback should never occur
if (1) the equipment is in good condition; (2) preheat
ports on cutting nozzles or welding tips are cleaned
frequently; and (3) operating pressures are correct.
Should flashback occur, IMMEDIATELY shut off the
torch. Allow it to cool off for at least a minute. Then
check your nozzle or tip, gas pressures, readjust regu-
lators if necessary, and relight the torch. If flashback
recurs, send the torch with nozzle in use when flashback
occurred to your distributor or to ESAB Remanufacturing
Center, Florence SC for repair.
MAINTENANCE
For all repairs other than those covered below, send
the apparatus to your ESAB Welding Products dis-
tributor or to ESAB Remanufacturing Center, 411 S.
Ebenezer Road, Florence SC 29501. Improperly re-
paired apparatus is hazardous.
Preheat Valves:
Leakage around either valve stem can
usually be corrected by tightening the packing nut
slightly. If this does not stop the leakage, replace the
valve stem assembly.
If either preheat valve fails to shut off completely, remove
the valve stem assembly from the torch. With a clean
cloth, wipe the ball in the end of the stem. Then reinsert
valve stem assembly and tighten it several times with
maximum force. If this does not eliminate leakage, try a
new valve stem assembly. If then the valve does not shut
off completely, send the torch to a repair station for
reseating of the body.
After installing a new valve stem assembly, tighten the
packing nut until the valve stem can be turned only with
great difficulty, and set the unit aside, for three or four
hours at least, to set the packing. Then back off the pack-
ing nut until the valve stem turns readily.
Cutting Valve:
If leakage develops around the cutting
valve stem or between the cutting valve guide and the
torch body, or if the valve fails to shut off completely,
proceed as follows:
1.
Remove cutting valve lever (see pg. 3).
2.
Unscrew cutting valve guide and lift out entire valve
assembly: guide (with external and internal O-rings),
valve stem, spring, and O-ring retaining washer.
3.
Pull stem out of guide. Replace it with new part
unless the molded rubber seat appears to be in ex-
cellent condition.
4.
Remove the internal O-ring (85W10) from the guide
and insert a new O-ring. Replace the external O-
ring (638797) if it shows distinct signs of wear.
5.
Reassemble by placing retaining washer and spring
in guide, then placing stem through spring and O-
ring in guide.
6.
Screw valve assembly into body. Before reassem-
bling cutting lever, connect torch to oxygen source,
apply at least 60 psi pressure, and check for leak-
age through the valve, around the stem, and around
the guide.
7.
Reassemble cutting lever to torch.
Mixer:
To remove the mixer for cleaning or replace-
ment, first unscrew the mixer chamber plug. Then let
the two springs drop out in your hand. Finally, dislodge
the mixer and its three washers (two brass, one Neo-
prene) either by rapping the torch, held vertically,
against a block of soft wood, or by turning a long 10-32
machine screw into the thread in the end of the mixer
and pulling it out.
When reassembling, place the three washers (one neo-
prene between two brass) on the extreme back end of
the mixer. (Be sure to use a new neoprene washer un-
less the old one appears to be in equal-to-new condi-
tion.) Slip mixer into torch, then insert large spring and
push it down hard to seat the forward brass washer
against shoulder in body. Then drop small spring inside
large spring, insert mixer plug, and tighten plug firmly.
Be sure the mixer chamber plug is fitted with an O-ring in
good condition (even in cases where the plug carried no
O-ring originally).
Содержание OXWELD C-62
Страница 7: ...7 ...