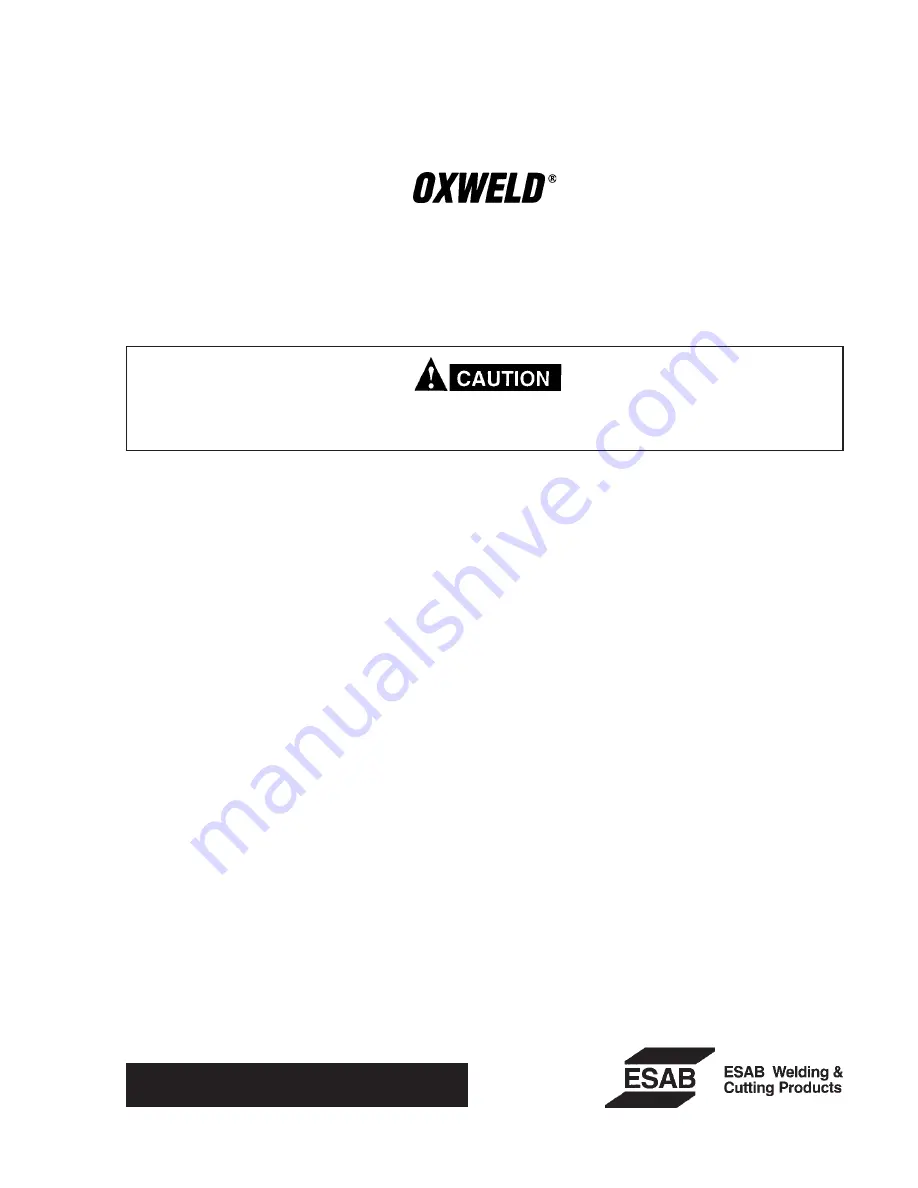
INSTRUCTIONS for
F-9178-K
May, 2009
C-62 Cutting Torch
and
Powder-Washing Attachment
These INSTRUCTIONS are for experienced operators. If you are not fully familiar with the principles of operation and safe practices for oxy-fuel gas
equipment, we urge you to read our booklet “Precautions and Safe Practices for Welding, Cutting and Heating”, Form 2035. Do not permit untrained
persons to operate this equipment. Do NOT attempt to operate this equipment until you have read and fully understand these instructions. If you do
not fully understand these instructions, contact your supplier for further information.
Be sure this information reaches the operator.
You can get extra copies through your supplier.
Testing for Leaks
Every cutting outfit should be thoroughly tested for leaks
after it is first hooked up, and at regular intervals there-
after. After all connections have been made, make sure
all valves on the torch handle are closed. Then turn in
the regulator pressure-adjusting screws until the oxy-
gen delivery-pressure gauge registers 60 psi and the
fuel gas delivery-pressure gauge registers 10 psi. Us-
ing Leak Test Solution that is suitable for oxygen ser-
vice, such as P/N 998771 (8 oz. container), check for
leaks at the cylinder valves, the cylinder-to-regulator con-
nections, the regulator-to-hose connections, and the hose-
to-torch connections. If bubbling at any point indicates
leakage, tighten the connection. If this does not stop leak-
age, close the appropriate cylinder valve, open the corre-
sponding torch valve to remove all pressure from the line,
and finally release the regulator pressure-adjusting screw
by turning it counterclockwise. Then break the leaky con-
nection, wipe metal seating surfaces with a clean dry
cloth, and examine them for nicks and scratches. Re-
make the connection(s) and retest. Do not try to light the
torch until you are satisfied that all connections are gas-
tight.
After lighting the torch and adjusting the flames, use
leak test solution to check for leakage at all torch valves
and at the nozzle nut.
OPERATION
Connecting
1.
Attach regulators to the oxygen and fuel gas cylin-
ders. Follow all instructions supplied with the regu-
lators.
2.
Attach oxygen and fuel gas hose to the regulators
and to the torch, after making sure all metal seat-
ing surfaces are clean. Tighten all connection nuts
with a wrench.
3.
Attach nozzle to torch head, and tighten connec-
tion nut with a wrench.
Adjusting Gas Pressures
Fuel Gas:
Open the fuel gas valve about one turn. Turn in
the pressure-adjusting screw on the acetylene regulator
until its delivery-pressure gauge registers the desired pres-
sure (see cutting chart on page 4). Then immediately
close the acetylene valve.
Oxygen:
Open the cutting oxygen valve by depressing
its valve lever fully. Turn in the pressure-adjusting screw
on the oxygen regulator until its delivery-pressure gauge
registers the desired pressure (see cutting chart on page
4). Then release the cutting oxygen lever.
NOTE: When gaugeless regulators are used, do not
open torch valves. Merely turn in the pressure-
adjusting screws to the desired pressure as in-
dicated on the scales of the regulator caps.
Содержание OXWELD C-62
Страница 7: ...7 ...