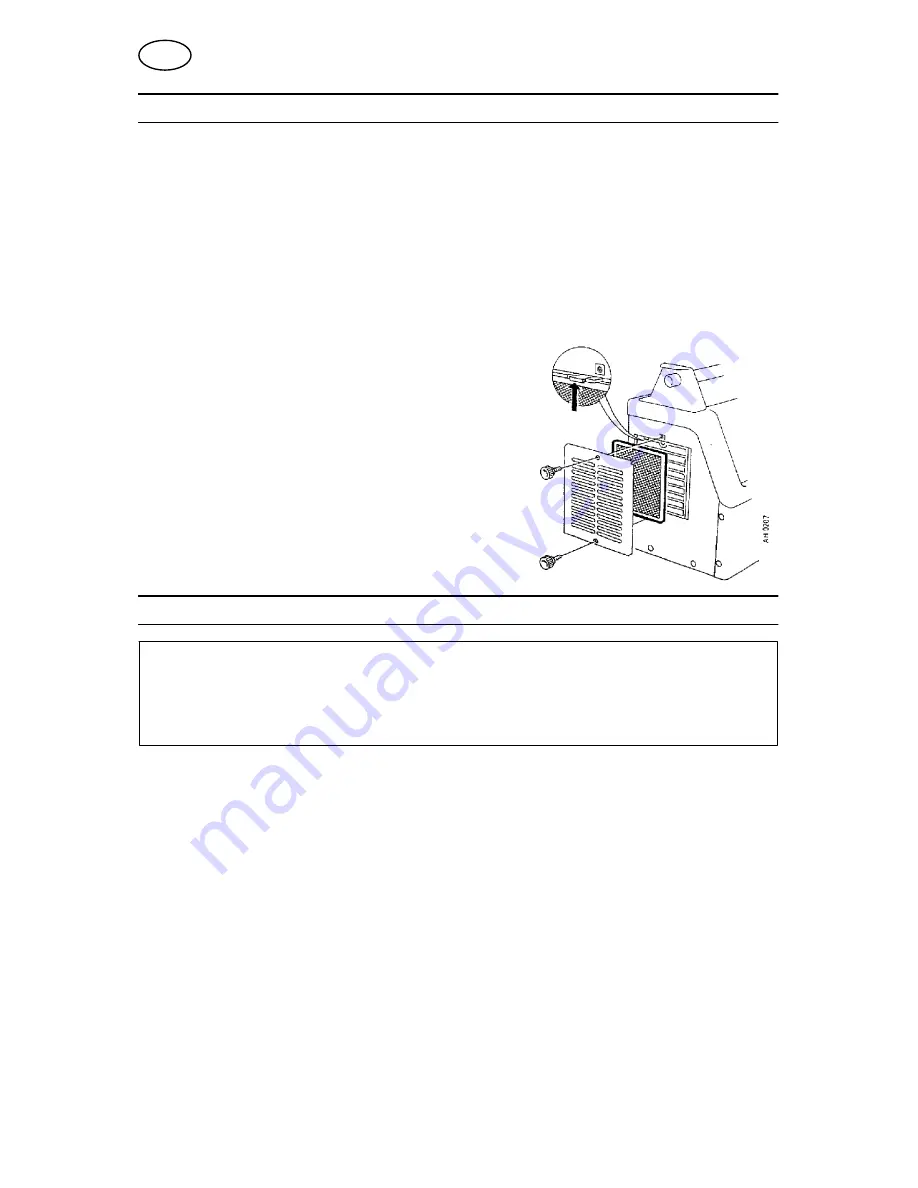
bt07d109
−
15
−
dpb1d1ea
7
MAINTENANCE
Regular maintenance is important for safe, reliable operation.
Only those persons who have appropriate electrical knowledge (authorized
personnel) may remove the safety plates to connect or carry out service,
maintenance or repair work on welding equipment.
Note!
All guarantee undertakings from the supplier cease to apply if the customer himself
attempts any work in the product during the guarantee period in order to rectify any
faults.
7.1
Check
−
up and cleaning
Clean the welding power source once a year using
dry compressed air (reduced pressure). The dust
filter is to be checked up and cleaned regularly.
If the welding power source is used in a dusty and
dirty environment, the cleaning should be
performed more frequently.
For maximal service reliability it could be
advisable to let an authorised retailer service the
machine once a year.
8
ORDERING OF SPARE PARTS
DTE 255 is designed and tested in accordance with the international and European
standards IEC/EN 60974
−
1 and EN 50199. It is the obligation of the service unit which
has carried out the service or repair work to make sure that the product still conforms
to the said standard.
Spare parts may be ordered through your nearest ESAB dealer, see the last page of
this publication.
GB
Содержание Aristotig255 AC/DC DTE 255
Страница 16: ...Edition 031110 Diagram 16 dpb1e11a ...