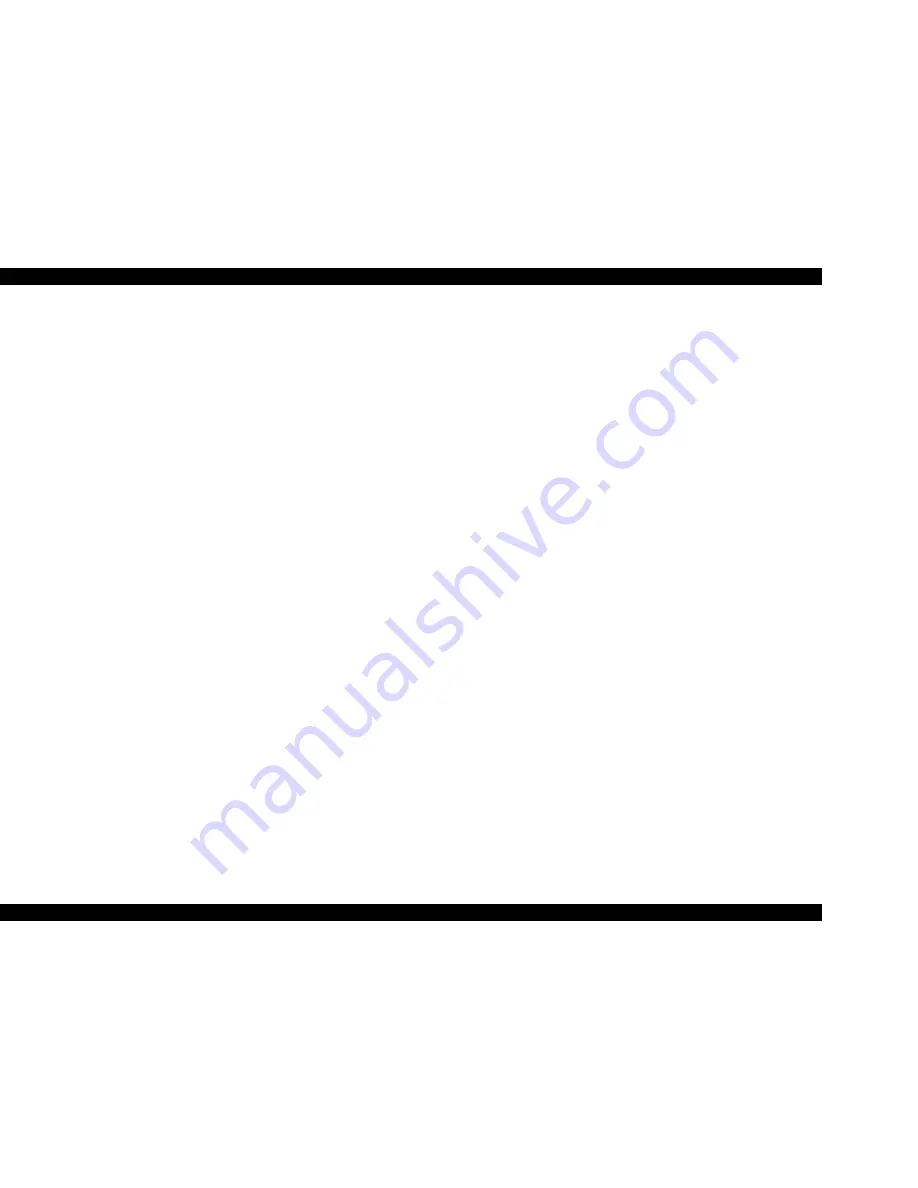
EPSON Stylus Pro 9500
Revision A
2
NOTE:
The contents of this book may change at anytime without notice.
No patent liability is assumed with respect to the use of information contained herein.
SEIKO EPSON CORPORATION assumes no liability for problems or damages resulting from the use of the information contained
herein.
EPSON is a registered trademark of SEIKO EPSON CORPORATION.
Other product names used herein are for identification purposes only and may be trademarks of their respective owners. EPSON
disclaims any and all rights in those marks.
Copyright 2000 SEIKO EPSON CORPORATION.
Содержание Stylus Pro 9500 Engine
Страница 6: ...C H A P T E R PRODUCTDESCRIPTION ...
Страница 43: ...C H A P T E R OPERATINGPRINCIPLES ...
Страница 69: ...C H A P T E R TROUBLESHOOTING ...
Страница 82: ...C H A P T E R DISASSEMBLY ASSEMBLY ...
Страница 155: ...C H A P T E R ADJUSTMENT ...
Страница 219: ...C H A P T E R MAINTENANCE SETUP ...
Страница 232: ...C H A P T E R APPENDIX ...
Страница 249: ...PSON Stylus Pro 9500 Revision A ppendix Exploded view Diagram 249 Figure 7 2 PF L Frame Assembly Fan Bracket Assembly ...
Страница 250: ...PSON Stylus Pro 9500 Revision A ppendix Exploded view Diagram 250 Figure 7 3 R Frame Assembly ...
Страница 251: ...PSON Stylus Pro 9500 Revision A ppendix Exploded view Diagram 251 Figure 7 4 PF Rail Assembly ...
Страница 252: ...PSON Stylus Pro 9500 Revision A ppendix Exploded view Diagram 252 Figure 7 5 CR Rail Assembly ...
Страница 253: ...PSON Stylus Pro 9500 Revision A ppendix Exploded view Diagram 253 Figure 7 6 CR Assy ...
Страница 254: ...PSON Stylus Pro 9500 Revision A ppendix Exploded view Diagram 254 Figure 7 7 Maintenance Assy ...
Страница 255: ...PSON Stylus Pro 9500 Revision A ppendix Exploded view Diagram 255 Figure 7 8 I H Assy Left ...
Страница 256: ...PSON Stylus Pro 9500 Revision A ppendix Exploded view Diagram 256 Figure 7 9 I H Assy Right ...
Страница 257: ...PSON Stylus Pro 9500 Revision A ppendix Exploded view Diagram 257 Figure 7 10 I H Assy 1 ...
Страница 258: ...PSON Stylus Pro 9500 Revision A ppendix Exploded view Diagram 258 Figure 7 11 I H Assy 2 ...
Страница 259: ...PSON Stylus Pro 9500 Revision A ppendix Exploded view Diagram 259 Figure 7 12 Tube Assembly ...
Страница 260: ...PSON Stylus Pro 9500 Revision A ppendix Exploded view Diagram 260 Figure 7 13 Board Assembly ...
Страница 261: ...PSON Stylus Pro 9500 Revision A ppendix Exploded view Diagram 261 Figure 7 14 Cover Assembly ...
Страница 265: ......
Страница 266: ......