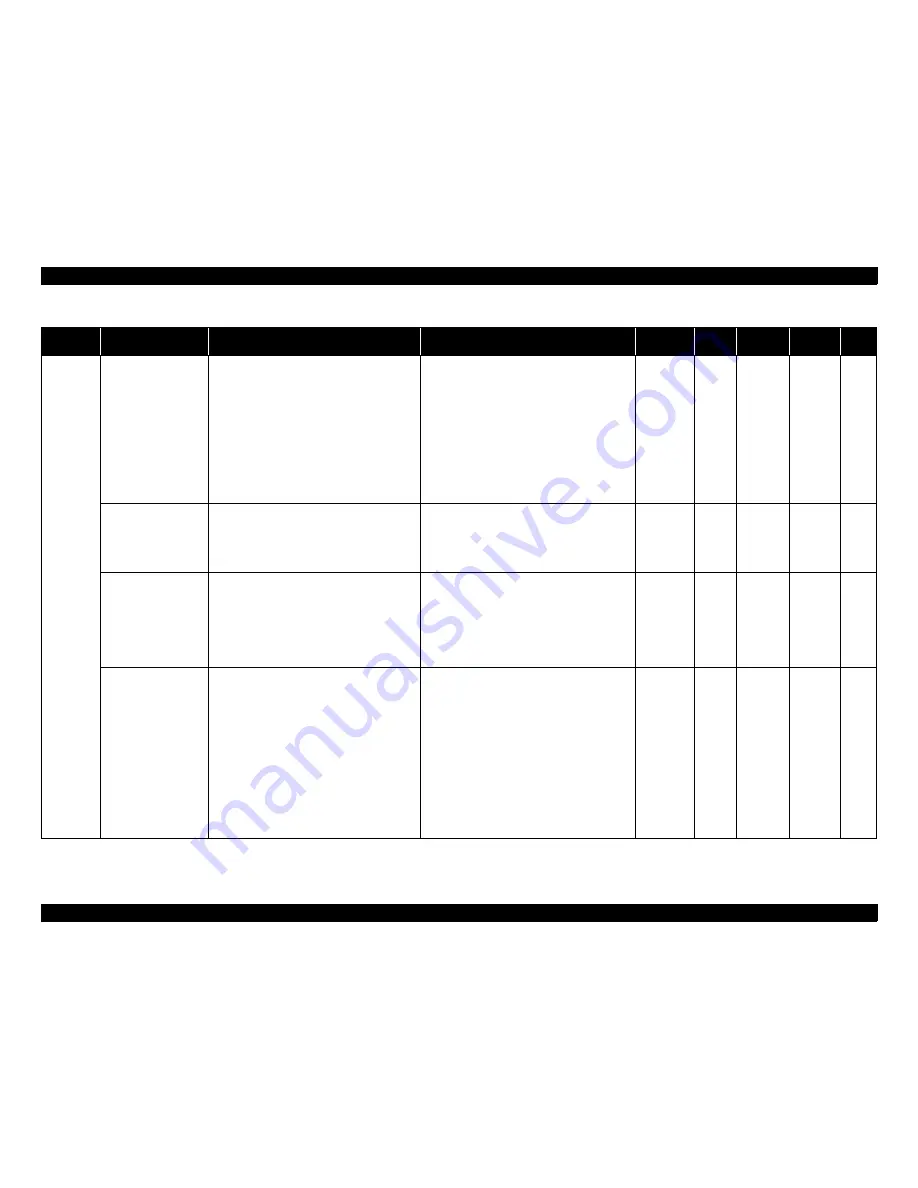
SC-T7000 series/SC-T5000 series/SC-T3000 series
Revision B
ADJUSTMENT
Overview
212
Confidential
CR related
CR Motor Measurement
& Automatic
Adjustment
The CR MOTOR is designed to stop when the
amount of heat generation (motor temperature)
during motor operation reaches a predetermined
limit. The amount of heat generation is estimated
based on the electrical characteristics of the
motor, which vary by motor and power supply of
the printer. Therefore, to get the motor control to
work properly, the electrical characteristics
values of the motor need to be measured and
stored in the memory on the MAIN BOARD.
If this adjustment is not made, the estimation of
the motor temperature cannot be made properly
and may cause the following symptoms.
Even though there is no problem with the
motor temperature, the printer pauses during
printing because it judges that the motor is in
high-temperature state.
Despite the motor is in a high-temperature
state, a lower motor temperature is estimated
and the printer does not stop. This may cause
the printer to malfunction.
Normal
mode
√
p. 279
Auto Uni-d adjustment
Reduces misalignment of ink droplets fired to
paper during unidirectional printing.
If this adjustment is not made, print quality
problems such as misaligned lines, grainy image,
banding may occur.
Normal
mode
√
Premium
Glossy
Photo
Paper
(250)
p. 241
Auto Bi-D adjustment,
acceleration and
deceleration correction
Auto Bi-d adjustment: Reduces misalignment
of ink droplets fired to paper during
bidirectional printing.
Acceleration and deceleration correction: To
improve print quality for bidirectional
printing, corrects the movement speed of the
CR UNIT.
Auto Bi-d adjustment: If this adjustment is not
made, print quality problems such as
misaligned lines, grainy image, banding may
occur.
If this adjustment is not made, print quality
problems may occur.
Normal
mode
√
Premium
Glossy
Photo
Paper
(250)
p. 242
PW + T&B&S check
and adjustment
PW: Checks that the PW sensor detects the
edges of paper correctly. Feed A4 matte paper
from the paper cassette and perform the
detection operation using the Service
Program.
T&B&S: Adjusts the print start position of the
top, bottom, right and left edges of paper.
Feed A4 matte paper from the paper cassette
and print the adjustment patterns using the
Service Program. Measure the adjustment
patterns then input the measurement result.
The print start position is automatically
adjusted.
If this adjustment is not made, the width or length
of paper cannot be detected correctly. As the
result, misaligned print position or insufficient
blank space may occur, or printed images may be
broken.
Normal
mode
√
Archival
Matte
Paper/
Enhanced
Matte
Paper
p. 243
Table 4-2. Adjustment Items
Class
Adjustment Items
Overview
Symptoms that the Adjustment is Needed
Printer Mode
Service
Program
Jig
Media
Page
Содержание SC-T3000
Страница 10: ...Confidential C H A P T E R 1 PRODUCTDESCRIPTION ...
Страница 39: ...Confidential C H A P T E R 2 TROUBLESHOOTING ...
Страница 66: ...Confidential C H A P T E R 3 DISASSEMBLY ASSEMBLY ...
Страница 197: ...Confidential C H A P T E R 4 ADJUSTMENT ...
Страница 280: ...Confidential C H A P T E R 5 MAINTENANCE ...
Страница 290: ...Confidential C H A P T E R 6 APPENDIX ...
Страница 309: ...SC T7000 series SC T5000 series SC T3000 series Revision B APPENDIX Panel Menu Map 309 Confidential 6 3 Panel Menu Map ...