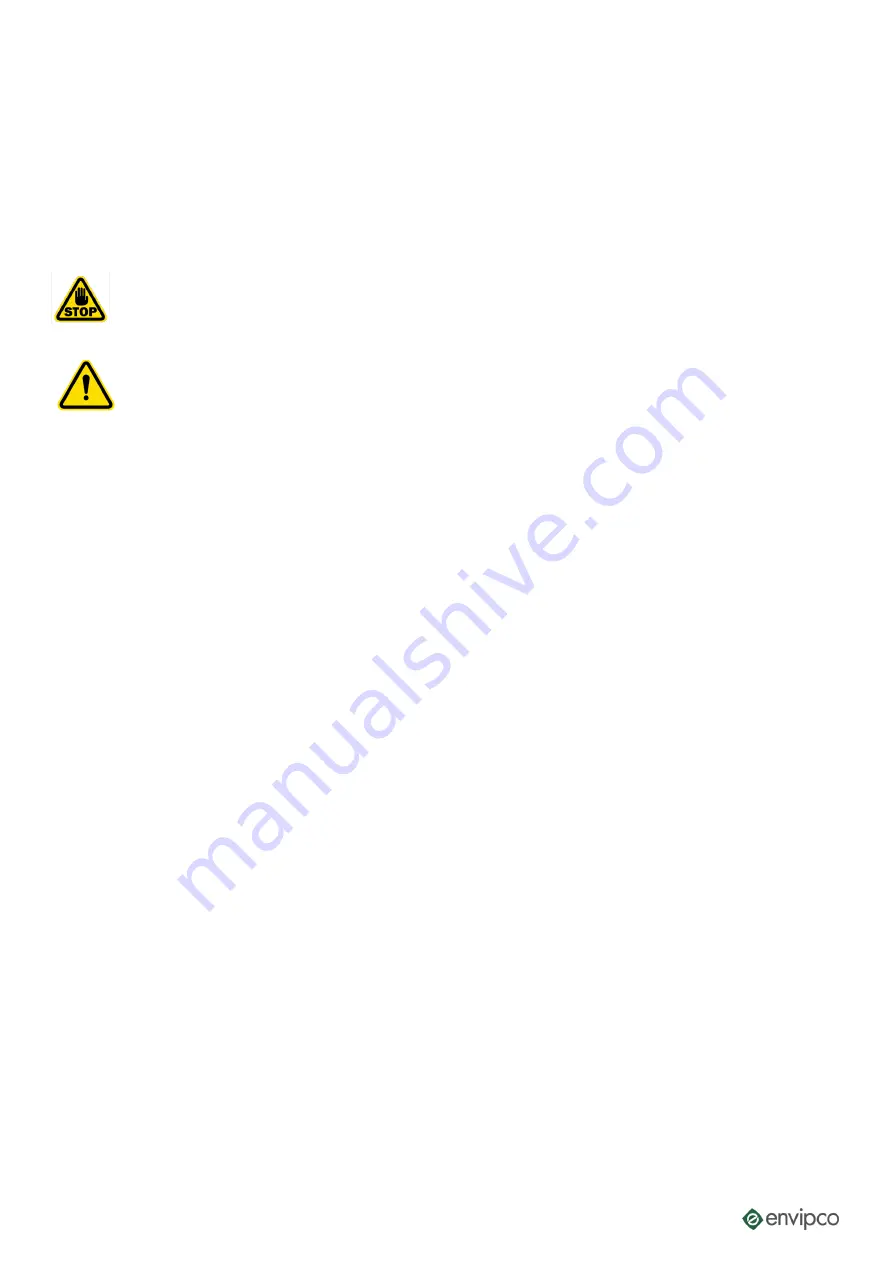
FLEX LS | USER MANUAL | 23
2.6. SERVICING THE FLEX LS
When a machine requires attention, it goes out of service and displays a message on the LCD screen.
The attendant can handle messages such as “machine full” and “out of paper.” When any other message
appears, call the service number listed inside the front of the machine.
WARNING!
If the cord is damaged, it must be replaced by the manufacturer, its service agent or simi-
larly qualified persons in order to avoid a hazard.
NOTE:
THE SERVICE PHONE NUMBER IS LISTED INSIDE THE
FRONT UPPER DOOR OF THE MACHINE.
The customer service dispatcher will require some basic information from the caller. To save time,
have the following information ready before calling:
• Name and location of the store.
• The type of machine needing service.
• The message displayed on the machine.
• Other information which may be useful to the technician such as “The machine will not crush
containers” or “We are unable to clear a jam.”
2.6.1 MAINTENANCE PROVIDER RESPONSIBILITIES
The maintenance provider performs the following tasks at each visit:
•
Cabinet –
Clean the cabinet as needed to maintain a neat and clean appearance.
•
Harness –
Check that all clamps are in place and secure. Make sure that all wires are well connected.
•
Printer –
Check operation, and clean away any excess paper bits or dirt.
•
AC motor control box –
Check incoming power, and adjust if necessary.
•
In-feed unit –
Clean the conveyor area and the conveyor belts.
•
Drip Tray –
Clean the drip tray and connected hoses.
•
Scanners –
Clean the scanner windows using ammonia free cleaner and a soft microfiber cloth.
•
Sorter unit –
Clean debris away from the proximity switch and make any needed adjustments.
•
Compactor –
Adjust the compactor stall sensor, if necessary.
•
Bins –
Clean up any debris that has fallen out of the bins.
•
Feed sensors –
Clean and calibrate.