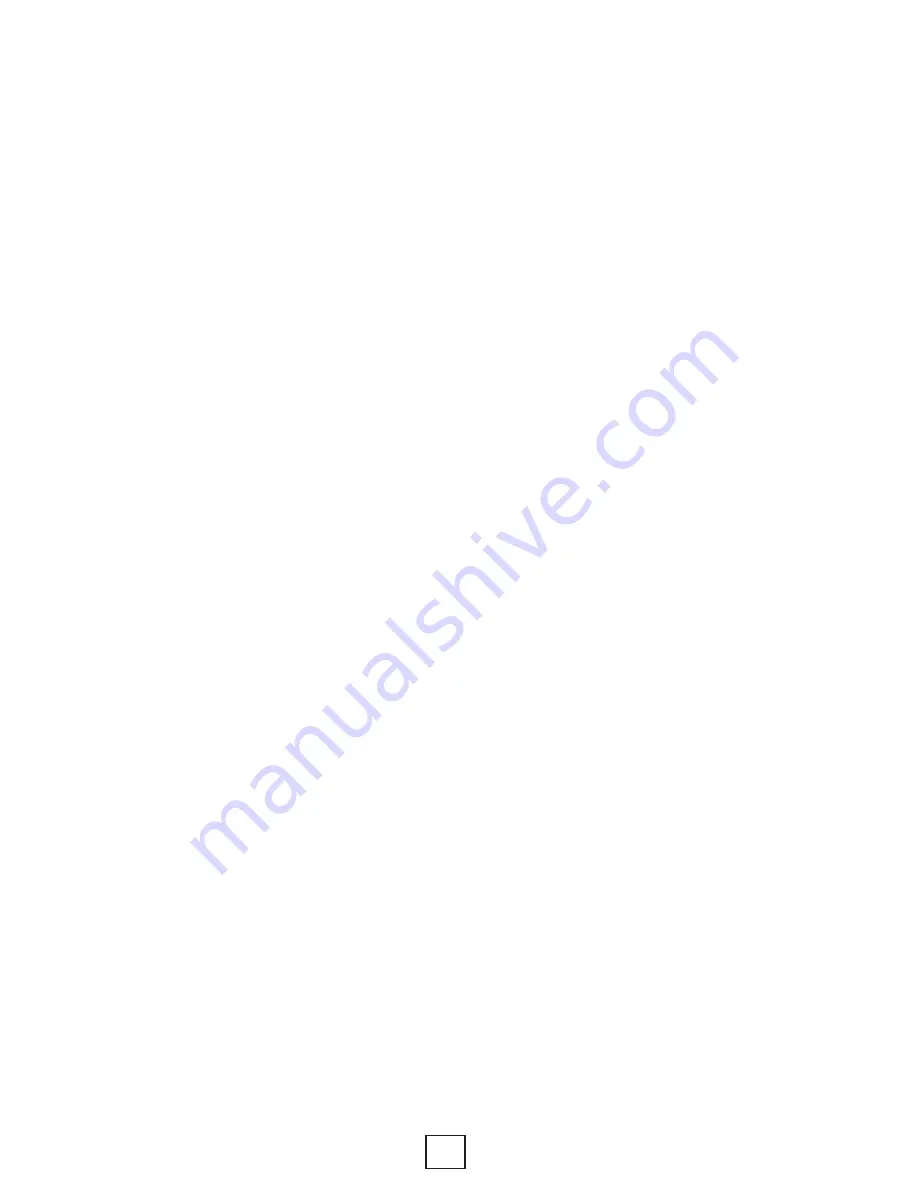
18
Enertech Global
HP IOM, Rev. B
Section 6: Antifreeze
Antifreeze Overview
In areas where minimum entering source temperatures drop
below 40°F, or where piping will be routed through areas
subject to freezing, antifreeze is required. Alcohols and glycols
are commonly used as antifreeze. However, local and state/
provincial codes supersede any instructions in this document.
In addition, the system needs antifreeze to protect the braze
plate heat exchanger from freezing and rupturing. Freeze
protection should be maintained to 15°F below the lowest
expected entering loop temperature. For example, if 30°F is
the minimum expected entering loop temperature, the leaving
source temperature could be 22 to 25°F. Freeze protection
should be set at 15°F (30-15 = 15°F). To determine antifreeze
requirements, calculate how much volume the system holds.
Then, calculate how much antifreeze will be needed by
determining the percentage of antifreeze required for proper
freeze protection. See Tables 3a and 3b for volumes and
percentages. The freeze protection should be checked during
installation using the proper hydrometer to measure the
specific gravity and freeze protection level of the solution.
Antifreeze Characteristics
Selection of the antifreeze solution for closed loop systems
require the consideration of many important factors, which
have long-term implications on the performance and life of the
equipment. Each area of concern leads to a different “best
choice” of antifreeze. There is no “perfect” antifreeze. Some
of the factors to consider are as follows (Brine = antifreeze
solution including water):
Safety: The toxicity and flammability of the brine (especially in
a pure form).
Cost: Prices vary widely.
Thermal Performance: The heat transfer and viscosity effect of
the brine.
Corrosiveness: The brine must be compatible with the system
materials�
Stability: Will the brine require periodic change out or
maintenance?
Convenience: Is the antifreeze available and easy to transport
and install?
Codes: Will the brine meet local and state/provincial codes?
The following are some general observations about the types
of brines presently being used:
Methanol: Wood grain alcohol that is considered toxic in pure
form. It has good heat transfer, low viscosity, is non-corrosive,
and is mid to low price. The biggest down side is that it is
flammable in concentrations greater than 25%.
Ethanol: Grain alcohol, which by the ATF (Alcohol, Tobacco,
Firearms) department of the U.S. government, is required to
be denatured and rendered unfit to drink. It has good heat
transfer, mid to high price, is non-corrosive, non-toxic even in
its pure form, and has medium viscosity. It also is flammable
with concentrations greater than 25%. Note that the brand of
ethanol is very important. Make sure it has been formulated
for the geothermal industry. Some of the denaturants are not
compatible with HDPE pipe (for example, solutions denatured
with gasoline).
Propylene Glycol: Non-toxic, non-corrosive, mid to high price,
poor heat transfer in high concentrations, and potential for
high viscosity when cold (in high concentrations). It has also
been known to form a “slime-type” coating inside the pipe
when inhibitors are not used. Do not use food grade glycol,
since it does not include inhibitors. A 25% to 30% brine
solution is a minimum concentration for required inhibitors,
depending upon brand of glycol. If using a lower concentration
(e.g. 20% provides 19°F freeze protection), additional
inhibitors must be added. Note that some states/provinces
have toxicity requirements that must be verified based upon
the chemical composition of the inhibitors.