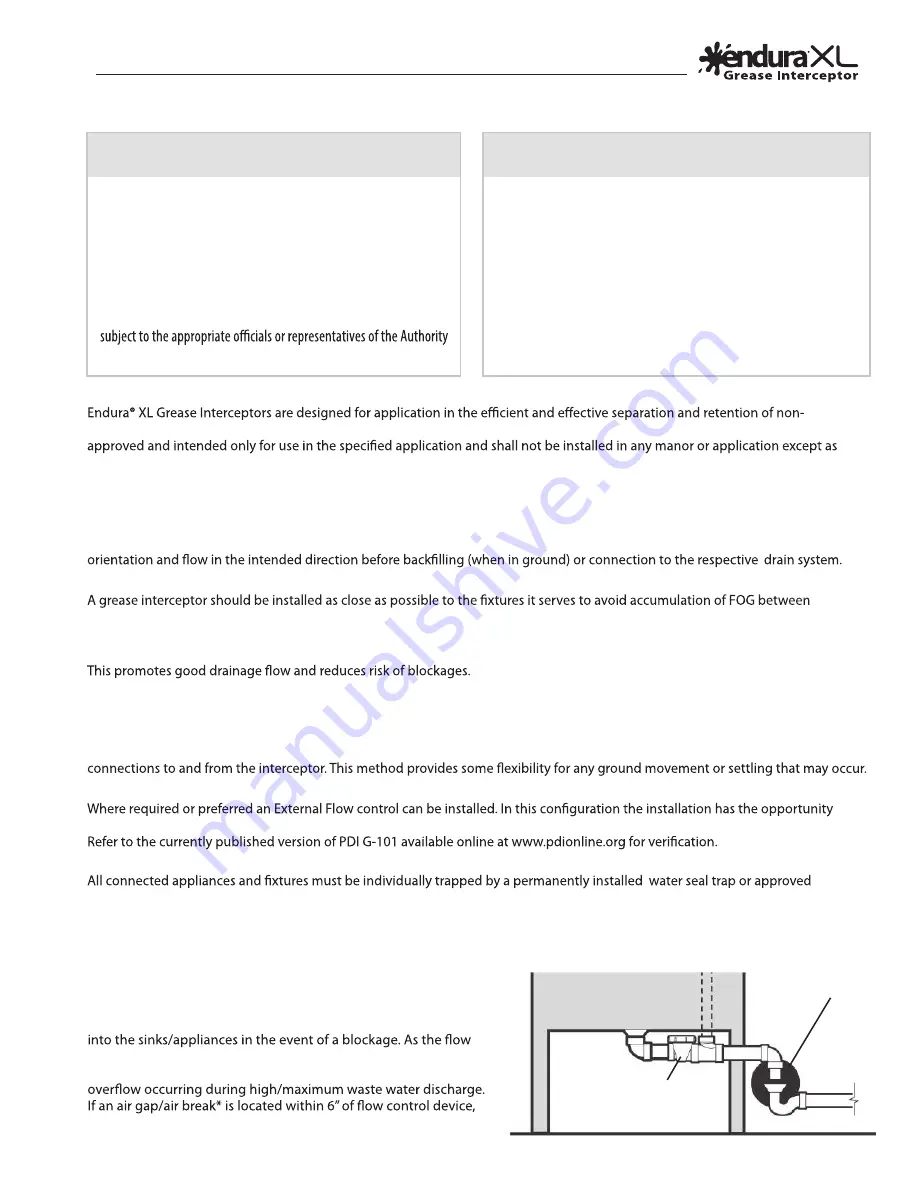
Installation Instructions
Installation
Scope of Application:
petroleum Fats, Oil and Grease as a by-product of commercial foodservice activities. The Endura® XL interceptor models are
tested and rated.
Accessibility:
Installations shall be made in such a manner that full access for maintenance and cleaning is maintained once the interceptor is
commissioned. A zone based on a column measured 3ft out from the cover perimeter and extending 7ft vertically is recommended.
Inlet (IN) and Outlet (OUT) connections are indicated on the interceptor itself. Ensure that the interceptor is in the correct
Location:
the source and the interceptor. Adequate provision for rodding and service access is particularly important upstream of the
interceptor. Please refer to local code requirements.
Drain lines servicing the interceptor shall be laid at a minimum ¼”per foot fall and with more gradient where possible.
Piping Connections:
The primary bulkhead-style connections (in-line) of Endura® XL are injection molded in Polyproylene (PP). PP does not accept
solvent weld cement and will not provide a serviceable connection. DO NOT SOLVENT WELD these drain connections.
Best practice and most codes typically require the use of Nationally or locally approved Mechanical Joint (MJ) couplings for the
Flow Control:
to meet the requirements of PDI G-101, assuming that the applicable venting and installation criterial are met (See Page 12).
Trapping:
equivalent, in compliance with applicable plumbing code requirements.
Venting:
The installation of the interceptor shall be vented downstream in accordance with local code requirements - typically within 10 ft max.
• Air Gap/ Air Break
• Flow Control Device
Indirect Connections/ Air Gap/Air Brake :
Some local jurisdictions require warewashing installations to be
made on an indirect basis incorporating an air gap.
This is to prevent the back up of contaminated waste water
control device provides a restriction within the system it must be
incorporated before the indirect connection to prevent the risk of
installation of the air intake tee is optimal.
*Dependent on jurisdiction
WARNING – SAFETY FIRST!
GREASE INTERCEPTORS ARE HAZARDOUS
ENVIRONMENTS AND MUST NEVER BE LEFT UNCOVERED
AND UNATTENDED, EVEN DURING MAINTENANCE.
• All access covers MUST be fully and completely secured
• All required bolts MUST at all times be in place and well tightened
• Missing bolts MUST be reported to management and replaced immediately
•
•
Covers MUST meet the required load rating for the application (see the
Technical Information section)
Do NOT use alternate covers
WARNING – SAFETY FIRST!
ALL INSTALLATION SHALL BE CONDUCTED UNDER THE
APPLICABLE HEALTH AND SAFETY REGULATIONS IN
FORCE WITHIN THAT JURISDICTION.
Plumbing operatives shall be adequately trained and appropriately
licensed to conduct the installation. All installations will be made
respective and in compliance with applicable plumbing code and any
locally published by-laws. Installation and approval of the same is
Having Jurisdiction (AHJ).
- 11 -