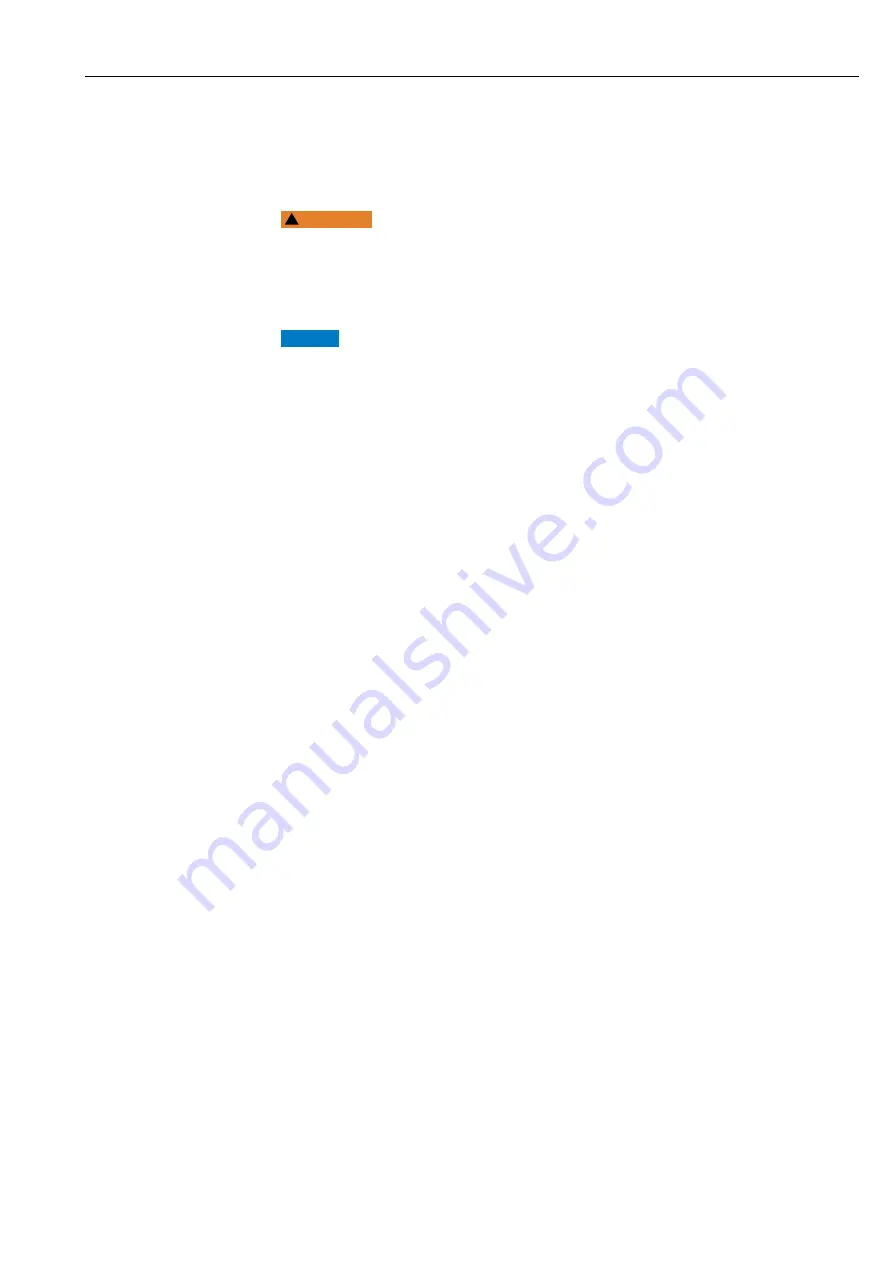
Conducal CLY421
Maintenance
Hauser
15
4
Maintenance
4.1
Cleaning
WARNING
!
The device is energized.
Performing cleaning work on live parts can result in injury or death.
‣
Disconnect the case from the power supply before commencing the cleaning tasks.
Clean the front of the housing of the transmitter and the case with commercially available
cleaning agents.
NOTICE
Cleaning agents can damage the surface of the device
Never use any of the following to clean the device:
‣
Concentrated mineral acids or bases
‣
Benzyl alcohol
‣
Methylene chloride
‣
High-pressure steam
If used correctly in the pure and ultrapure water range, no contamination will occur on the
flowmeter and the comparison sensor. Nevertheless, if the units do need to be cleaned, you
can rinse them with hot water or isopropyl alcohol.
4.2
Recalibration
Depending on the operating conditions and the frequency of use, the conductivity calibration
kit must be calibrated regularly at the factory (annual recalibration is recommended). You
then receive an updated factory calibration certificate.
4.3
Repair
If the device requires repair, please return the case containing the complete calibration kit to
Hauser.
4.4
Return
The device must be returned if repairs or a factory calibration are required, or if the wrong
device has been ordered or delivered. According to legal regulations, Hauser, as an
ISO-certified company, is required to follow certain procedures when handling returned
products that are in contact with medium.
To ensure swift, safe and professional device returns, please read the return procedures and
conditions on the internet site:
www.services.endress.com/return-material
4.5
Disposal
The product contains electronic components and must therefore be disposed of in
accordance with regulations on the disposal of electronic waste.
Observe local regulations.
Содержание Conducal CLY421
Страница 2: ...Endress Hauser...
Страница 23: ...Conducal CLY421 Endress Hauser 23...
Страница 24: ...www addresses endress com 71142937...