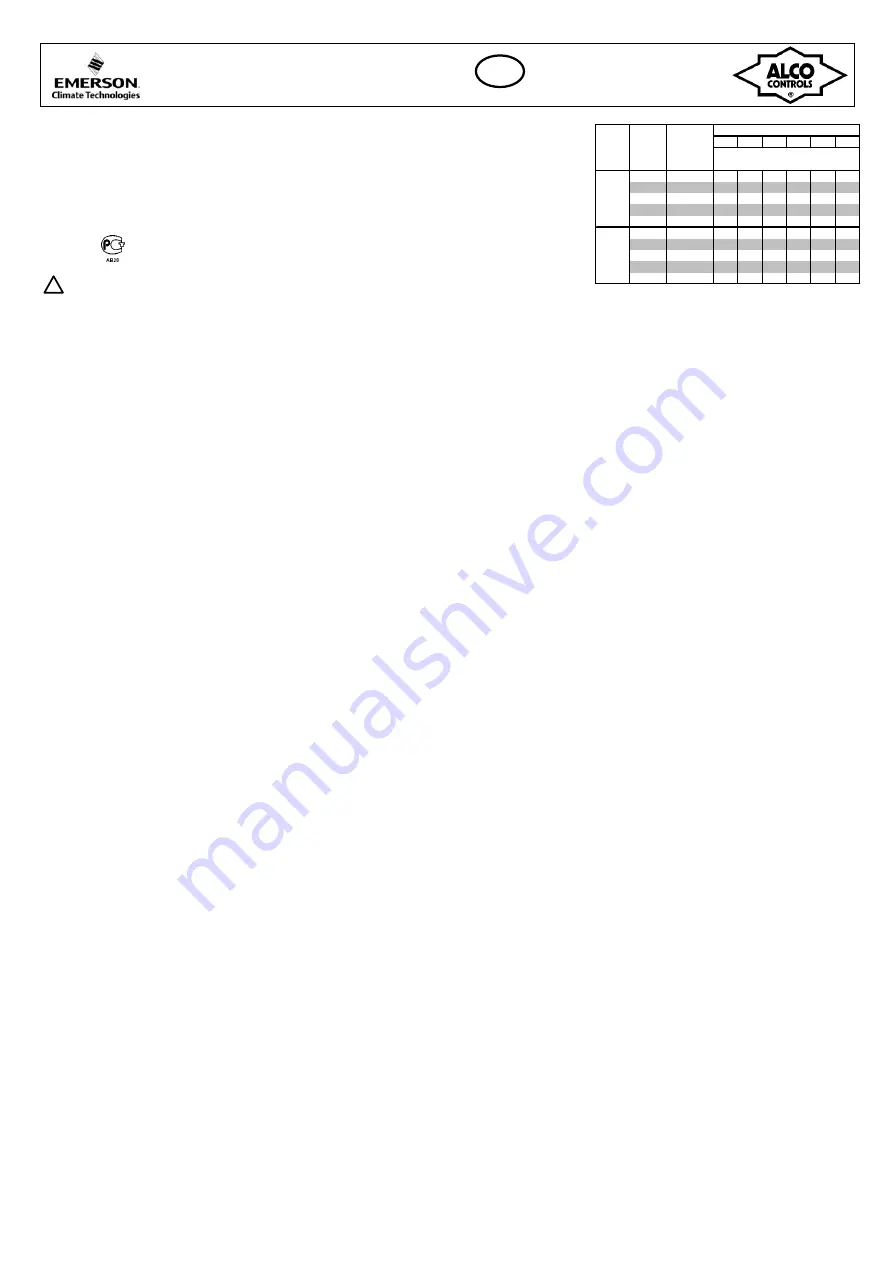
T_S__65022__R04.doc
Replacement for 03
Date: 21.07.2009
PCN 862157
Installation Instructions
Thermo
®
Expansion Valves
TCLE,
TJRE, TERE, TIRE, THRE
GB
Emerson Electric GmbH & Co. OHG
Heerstr.111 – D-71332 Waiblingen
Tel.: 07151 509-0 - Fax.: -200
www.emersonclimate.eu
General information and technical data
•
Refrigerants: see nameplate
•
Evaporating Temperature Range:
a) for valves with pressure limitation (MOP): see
nameplate
b) for valves without pressure limitation:
+30° C to -45° C
•
Max. Working Pressure PS: 31 bar
•
Safe Working Temperature: 80° C
•
Marking:
!
Safety instructions
•
Read installation instruction thoroughly.
Failure to comply can result in device failure,
system damage or personal injury.
•
It is intended for use by persons having the
appropriate knowledge and skill. Before
opening any system make sure pressure in
system is brought to and remains at
atmospheric pressure. Do not leak any
refrigerant into the atmosphere.
•
Do not use on service conditions or fluids not
specifically cataloged, without prior approval of
Alco Controls.
Installation (Fig. 1)
1 Power Assembly
7 Body Flange
2 Remote
Bulb
Gasket
3 External Equalizer
8 Seat Gasket
Connection
9
Body
Flange
4 Seal Cap
10 Cap Screws
5 Body Flange Gasket
11 Lugged Spring
6 Cage Assembly
Carrier
1.
Valves may be installed in any position, but
should be located as close as possible to
distributor or evaporator inlet.
2.
Install line connections to valve so its flow
arrow corresponds to flow direction on flange.
On valves with solder connections remove cap
screws, power assembly, cage assembly and
gaskets prior to brazing.
3.
Assemble valve after brazing, according to Fig
1, making sure that lugs of spring carrier line up
with slots inside power assembly.
4.
Tighten cap screws evenly to torque
specification 35 Nm. Overtorqueing may result
in valve body damage.
5.
Attach remote bulb to suction line as close to
evaporator outlet as possible in a horizontal run
and fix it, normally at the 4 or 8 o'clock
position. Clean surface of suction line before.
6.
Connect one end of external equalizer line (OD
= 6 mm = ¼ inch) to valve. Connect other end
to suction line slightly downstream from remote
bulb location and position it so that it cannot
syphon oil from the suction line.
7.
Check for leaks, sufficient system refrigerant
and be sure no flash gas is present.
Superheat Adjustment (Fig. 2)
ALCO Thermo
-Expansion Valves are factory
preset for optimum superheat settings. This setting
should be modified only if absolutely necessary. The
readjustment should be at the lowest expected
evaporating temperature:
1.
Remove seal cap (1) on side of valve.
2.
Turn adjusting stem clockwise to increase
superheat and counter-clockwise to decrease it.
Allen key X 99999 (2).
3.
Reinstall seal cap. Wait 20 minutes before
further adjustments.
4.
If refrigerant escapes use allen key X99999 (3)
to fix spindle gasket.
Pressure
Evaporating temperature °C
Valve Refri- c10
0
-10 -20 -30 -40
Series gerant per turn
Static superheat changes
(bar)
per turn of stem (K)
R 134a
0,05
0,4
0,5
0,6
0,9
R 22
0,05
0,3
0,3
0,4
0,5
0,7
1,0
TCLE R 404A
0,05
0,2
0,3
0,3
0,4
0,6
0,8
R 407C
0,05
0,2
0,3
0,4
0,6
R 507
0,05
0,2
0,3
0,3
0,4
0,5
0,7
TJRE R 134a
0,038
0,3
0,4
0,5
0,7
TERE, R 22
0,038
0,2
0,3
0,3
0,4
0,5
0,7
TIRE, R 404A
0,038
0,2
0,2
0,3
0,3
0,5
0,6
THRE R 407C
0,038
0,2
0,2
0,3
0,4
R 507
0,038
0,2
0,2
0,2
0,3
0,4
0,5
Note
1.
Foreign particles in Thermo
-Valve may cause
diaphragm failure, flooding or starving. Use of
an ALCO Filter Drier is strongly recommended.
2.
Protect valve against excessive vibrations as it
may result in bulb tubing breaking.
Leakage test:
After completion of installation, a test pressure must
be carried out as follows:
- According to EN378 for systems which must
comply with European pressure equipment directive
97/23/EC
- To maximum working pressure of system for other
applications
Warning:
- Failure to do so could result in loss of refrigerant
and personal injury.
- The pressure test must be conducted by skilled
persons with due respect regarding the danger
related to pressure.