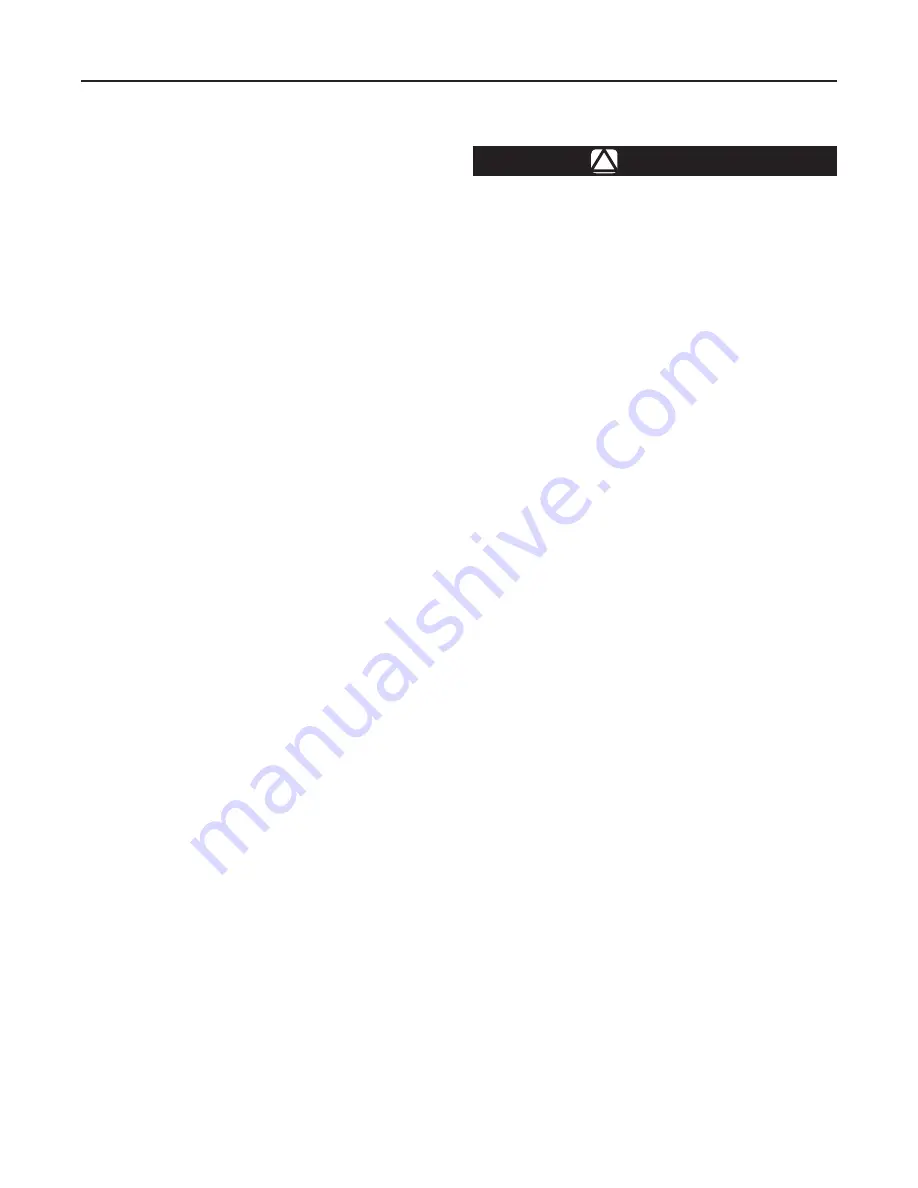
Type S402Y
5
1. Check to see that all downstream equipment is
turned off.
2. Slowly open the upstream shutoff valve.
3. Slowly open the downstream shutoff valve.
4. Check all connections for leaks.
5. Light the downstream equipment pilot lights
if applicable.
adjustment
If set pressure adjustment is necessary, monitor
downstream pressure with a gauge during the
adjustment procedure. To increase the outlet
pressure, the adjusting screw (key 12) must be turned
clockwise. This requires removal of the closing cap
(key 11). To reduce the outlet pressure setting, turn
the adjusting screw counterclockwise. Do not adjust
the spring to produce an outlet pressure setting above
the limit stamped on the regulator.
The range of allowable pressure settings is stamped
on the regulator. If a pressure setting beyond this
range is necessary, substitute the appropriate
regulator control spring. When changing the spring,
also change the range stamped on the regulator to
indicate the actual pressure range of the spring in use.
Before increasing the setting, refer to Table 1. Review
the pressure limits for the control spring range being
used and be certain that the new pressure setting
will not result in an overpressure condition. After the
spring adjustment has been completed, replace the
closing cap.
Shutdown
Installation arrangements may vary, but in any
installation it is important that the shutoff valves be
opened or closed slowly and that the outlet pressure
be vented before venting inlet pressure to prevent
damage caused by reverse pressurization of the
regulator. The steps below apply to the typical
installation as indicated.
1. Slowly close the upstream shutoff valve.
2. Release downstream pressure and be sure the
upstream pressure has been exhausted.
Maintenance
!
WaRning
To avoid personal injury or equipment
damage from sudden release of pressure
or uncontrolled gas, do not attempt any
maintenance or disassembly without
first isolating the regulator from
system pressure and relieving all
internal pressure as described in the
shutdown procedure.
Regulators that have been diassembled
for repair must be tested for proper
operation before being returned to
service. Due to the care Fisher takes in
meeting all manufacturing requirements
(heat treating, dimensional tolerances,
etc.), use only replacement parts
manufactured or furnished by Fisher to
repair Fisher
®
regulators. Relight
pilot lights according to normal
startup procedures.
Due to normal wear or damage that
may occur from external sources, this
regulator should be inspected and
maintained periodically. The frequency
of inspection and replacement of parts
depends upon the severity of service
conditions or the requirements of local,
state, and federal rules and regulations.
A program of periodic regulator inspection should be
established. Visually inspect the regulator for:
1. Improper installation.
2. Plugged or frozen vent.
3. Wrong regulator in the system.
4. Internal or external corrosion.
5. Age of the regulator.
6. Any other condition that could cause the
uncontrolled escape of gas.
Failure to establish an inspection program, as
outlined above, could result in personal injury or
property damage.