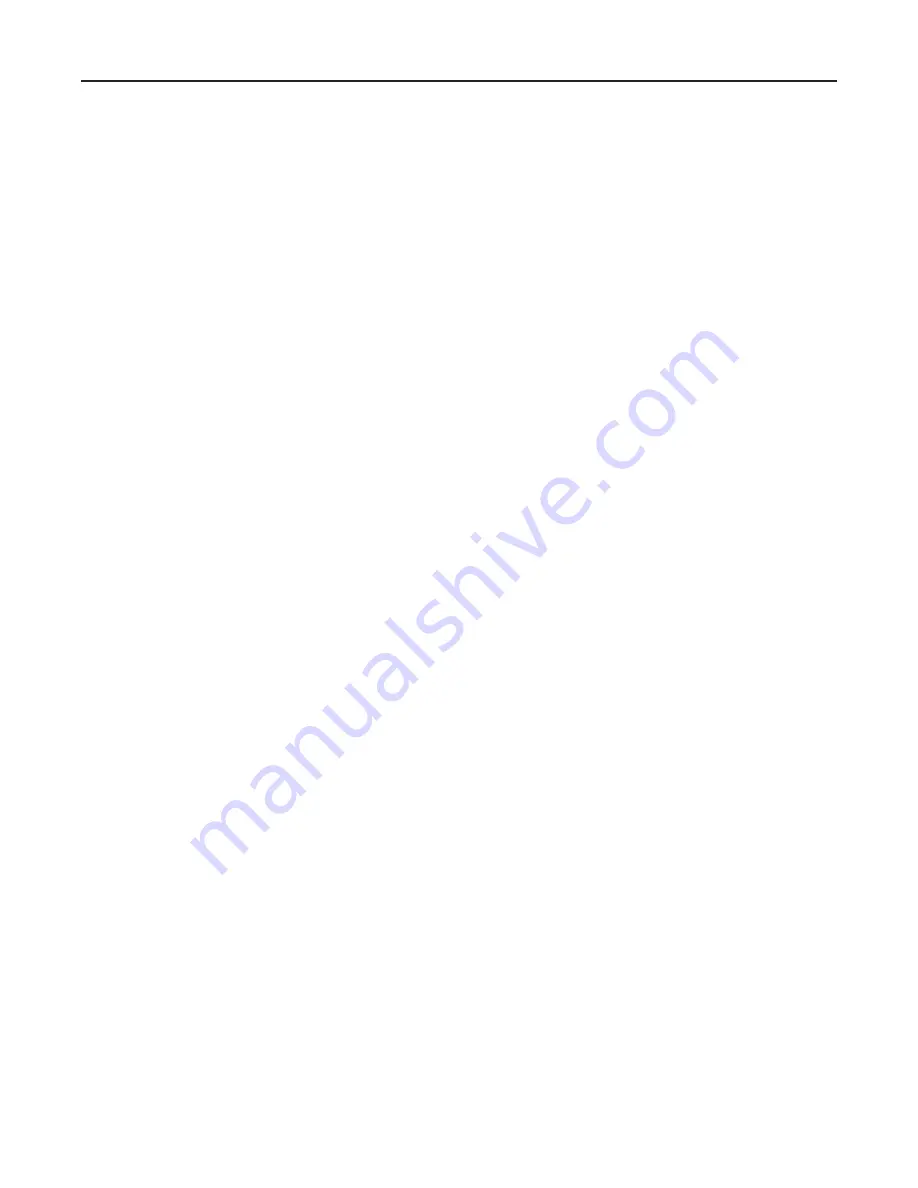
b. Avoid wrinkling the diaphragms when replacing
the diaphragm case and spring case.
c. Replace the diaphragm case, carefully working
the upper relay diaphragm (key 14) into the
recess in the diaphragm case. If the diaphragm
case rocks with respect to the pilot body,
diaphragm is probably wrinkled.
d. Replace the spring case, using care to smooth
the lower relay diaphragm (key 15) evenly into
the recess in the pilot body.
e. Install the eight cap screws, tightening them down
evenly in a crisscross pattern to avoid crushing the
diaphragm. Recommended final torque on these
cap screws is 10 to 12 ft-lbs / 14 to 16 N•m.
8. After assembly, make sure of the proper control
spring setting according to the Installation and
Startup section and restamp the nameplate
(key 27) if needed.
Type 161EBM Pilot
Key numbers are referenced in Figure 10 unless
otherwise noted.
Trim Parts
1. As shown in Figure 10, remove the body plug
(key 3). Use needle nose pliers to remove the plug
spring (key 6) and plug/stem assembly (key 4).
2. Inspect the removed parts and body plug O-ring
(key 15), replace as necessary and make sure the
plug seating surfaces are free from debris.
3. Sparingly apply lubricant to the body plug O-ring
(key 15) and the threads of the body plug (key 3).
Install the body plug O-ring over the body plug.
4. As shown in Figure 10, stack the plug spring
(key 6) and plug/stem assembly (key 4) on the
body plug (key 3). Install the body plug with
stacked parts into the body (key 1).
Diaphragm Parts
1. Remove the closing cap (key 16), loosen the
locknut (key 12) and back out the adjusting screw
(key 11) until compression is removed from the
control spring (key 9).
2. Remove the machine screws (key 13) and
separate the spring case (key 2) from the body
assembly (key 1). Remove the control spring seat
(key 8), the control spring (key 9) and, if used, the
diaphragm limiter (key 10).
3. Remove the diaphragm assembly (key 7) and
inspect the diaphragm.
4. To gain access to the stem guide seal O-ring,
remove and inspect the stem guide seal assembly
(key 19) and if damaged replace the complete
assembly. Inspect the outer O-ring (key 22),
replace if necessary.
5. Install the diaphragm assembly (key 7) and push
down on it to see if the plug/stem assembly
(key 4) strokes smoothly and approximately
1/16 in. / 1.6 mm.
Note
In step 6, if installing a control spring
with a different range, be sure to replace
the spring range indicated on the
spring case with the new spring range.
A diaphragm limiter (key 10) and other
listed parts are required with the highest
spring range.
6. As shown in Figure 10, stack the control spring
(key 9), the control spring seat (key 8) and, if used,
the diaphragm limiter (key 10) onto the diaphragm
assembly (key 7). Make sure that, if used, the
diaphragm limiter is installed bevelled side up.
Sparingly apply lubricant to the control spring seat.
7. Install the spring case (key 2) on the body (key 1)
with the vent (key 18) oriented to allow for wrenches,
needed for connecting outlet piping and to prevent
clogging or entrance of moisture. Install the machine
screws (key 13) and, using a crisscross pattern,
torque them to 5 to 7 ft-lbs / 6.8 to 9.5 N•m for
Stainless steel constructions and 2 to 3 ft-lbs / 2.7 to
4.1 N•m for aluminum constructions.
Note
Spring case vent may be mounted in
any orientation convenient to your
application, but plastic vent (key 18)
should be oriented downward.
8. When all maintenance is complete, refer to the
Startup and Adjustment section to put the regulator
back into operation and adjust the pressure
setting. Tighten the locknut (key 12), replace the
closing cap gasket (key 17) if necessary and install
the closing cap (key 16).
13
Type EZL