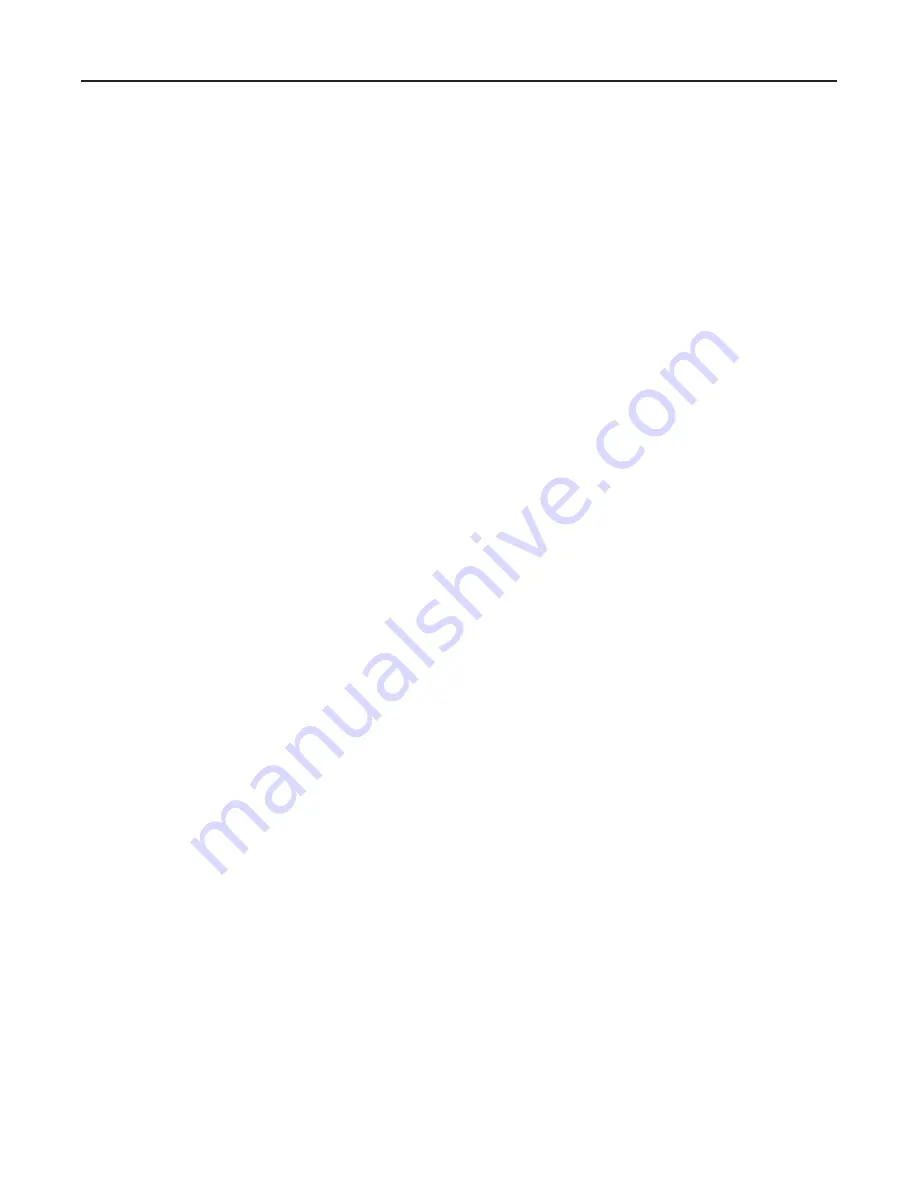
Never-Seez
®
is a mark owned by Never-Seez Corp.
Lok-Cease
®
is mark owned by Certified Laboratories.
3. Install the control spring (key 13), the lubricated
upper spring seat (key 14) and the spring case
(key 2). Insert and tighten the cap screws (key 17).
Lubricate the adjusting screw (key 16) with
Never-Seez
®
or equivalent lubricant, and thread it
into the spring case.
4. Unscrew the valve plug guide (key 5). Remove
the strainer screen (key 12), the valve plug
(key 4), the valve plug cap (key 26) and the valve
plug spring (key 11). Unscrew the orifice (key 3).
Clean and replace parts as necessary. Apply
Never-Seez
®
or equivalent lubricant to the orifice
threads, and screw the orifice into place.
5. Place the valve plug spring (key 11) into the valve
plug guide (key 5). Insert the valve plug cap (key 26)
into the valve plug (key 4), and then slide both
parts over the spring and into the valve plug guide.
Place the strainer screen (key 12) onto the valve
plug guide. Apply Lok-Cease
®
20/20 sealant or
equivalent (key 21) to the valve plug guide threads,
and screw the valve plug guide with the attached
parts into the pilot body (key 1).
6. When maintenance is completed, refer to the
Startup section to put the regulator back into
operation, and adjust the pressure setting.
Types 6492HM and 6492HTM
Safety Override Pilots
These procedures are to be performed if inspecting,
cleaning or replacing any pilot parts or of cycling,
erratic control or too high or too low an outlet (control)
pressure is noted. Perform only those procedures
in this section required to correct the problem. Key
numbers refer to Figure 11.
Note
Before performing any maintenance,
loosen the hex nut (key 16), if used,
and turn the adjusting screw (key 15) or
handwheel (key 31) counterclockwise
until all compression is removed from
the control spring (key 12). Remove the
pilot spring from the pipe nipple and
connectors (keys 82 and 83, Figure 12).
1. Unscrew the plug guide (key 2). Remove the
screen (key 77), inner valve (key 4), plug spring
(key 3) and stem (key 7). Unscrew the orifice
(key 5). Examine the orifice and plug seating
surfaces for damage.
2. Clean and replace parts as necessary. Apply
sealant to the orifice threads. Thread the orifice
into place and tighten using 19 to 25 ft-lbs / 26 to
34 N•m of torque.
3. Handle parts carefully, and place the plug spring
(key 3) in the plug guide (key 2). Slide the inner
valve (key 4) over the spring and into the plug
guide. Place the screen (key 77) onto the plug
guide. Place the stem (key 7) in the center hole
of the plug guide. Apply sealant to the plug guide
threads, and screw the guide plus attached parts
into the body (key 1).
4. Remove the pipe plug (key 74). Then remove the
pipe plug (key 94). Clean and replace the pipe
plugs as necessary.
5. Apply sealant to the threads of the pipe plug
(key 94) and install.
6. Apply sealant to the threads of the pipe plug
(key 74). Thread the pipe plug into place and
tighten using 5 to 15 ft-lbs / 6.8 to 20 N•m
of torque.
7. Remove the cap screws (key 17), spring case
(key 14), control spring (key 12) and upper spring
seat (key 13) from the body (key 1).
8. Remove the lower spring seat (key 11),
diaphragms (key 10) and diaphragm gasket
(key 18) from the body. Inspect and clean the
diaphragm gasket, and replace if necessary.
9. Unscrew the bellows retainer (key 8) and remove
the bellows (key 9). Replace worn parts as
necessary, and install the bellows and bellows
retainer. Tighten the bellows retainer using 19 to
25 ft-lbs / 26 to 34 N•m of torque.
10. Install the diaphragm gasket. Install both
diaphragms with their raised performed centers
facing toward the spring case.
11. Lubricate the upper spring seat and the exposed
threads of the adjusting screw. Install the lower
spring seat (key 11), control spring (key 12), upper
spring seat (key 13) and spring case (key 14).
Insert and tighten the cap screws (key 17) in a
crisscross bolting pattern using 12 to 18 ft-lbs /
16 to 24 N•m of torque.
Parts Ordering
When corresponding with your local Sales Office about
this equipment, always specify the equipment serial
number as found on the regulator nameplate.
When ordering replacement parts, specify the
complete 11-character part number of each needed
part as found in the following parts list.
11
Type 92C