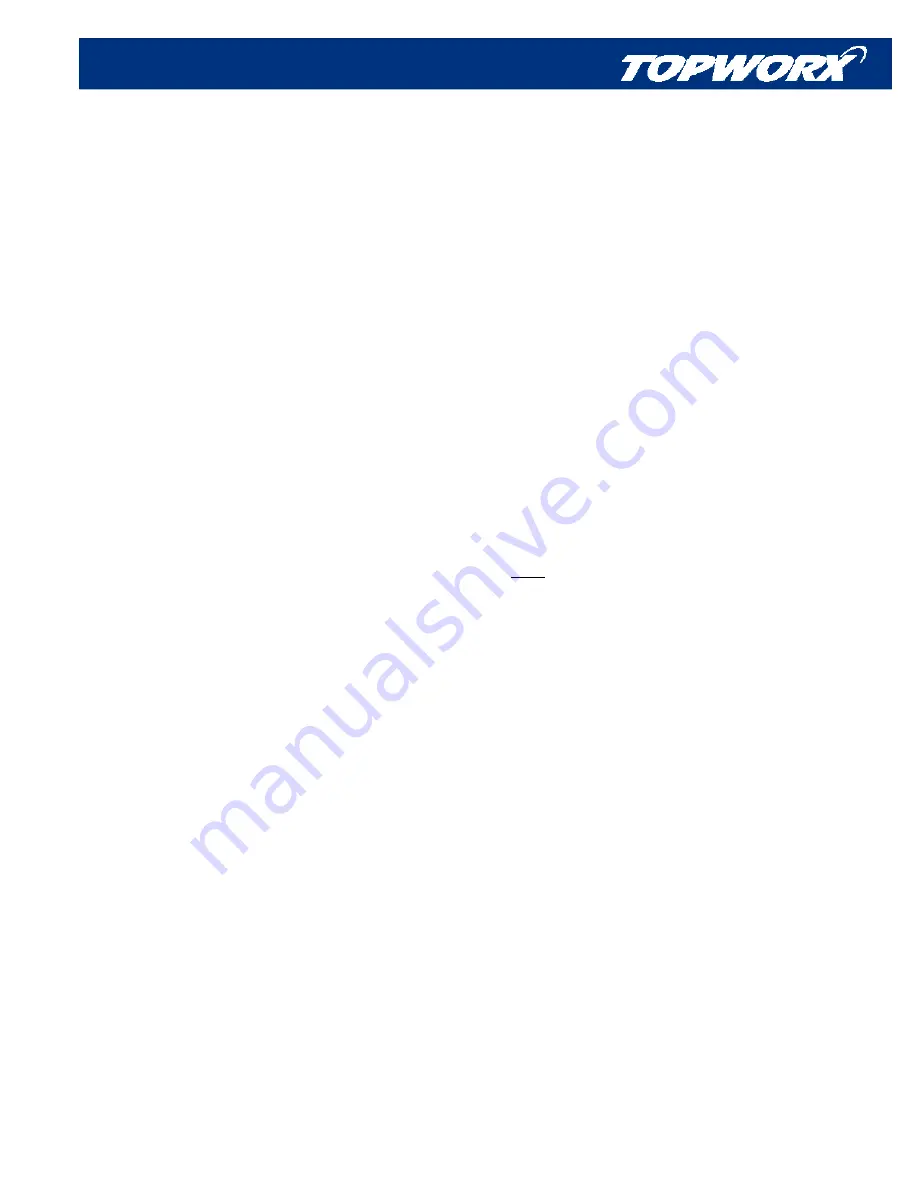
www.topworx.com
21
TM
Appendix C: Transducer Block
Transducer Block Initialization
There are several settings in the transducer block that should be set before
commissioning of the SCM-FF.
Through these parameters, a user can configure a wide range of diagnostics
and alarms. These include cycle timers, and counters, as well as temperature
monitoring. The alarm conditions can be configured through a transducer
channel in one DI Block.
Also, the user may configure the SCM-FF for use in Single or Dual pilot valves
for Direct or Reverse Acting applications, all through convenient Transducer
settings.
(a) Diagnostics & Alarming
There will be 5 limit parameters that must be set during calibration. These
parameters will vary with the type of valve the device is operating. The alarm
priorities must also be set, depending on the application.
By simply changing the settings in the transducer, all the diagnostic limits and
functional settings can be set by the end user.
1.
Cycle
Times
Set
the
Cycle Time Open Limit
(LIM_CYC_OPEN_TIME) and the
Cycle Time Close Limit
(LIM_CYC_CLOSE_TIME) parameters to
the maximum amount of time in seconds the valve is allowed to
complete its stroke before an alarm condition is invoked. If the LEDs
are enabled, they will blink for local notification of the time limit
alarms. If the Cycle Time Open Limit is exceeded, the green LED
will flash. If the Cycle Time Close Limit is exceeded, the red LED will
flash. Pushing the Alarm Reset Pushbutton on the board will stop
the flashing.
The default setting for both the Cycle Time Open and Cycle Time
Closed Time Limit is 10 seconds.
2.
Cycle
Count
Set
the
Cycle Count Limit
(LIM_CYC_COUNT) parameter to the
maximum number of valve cycles allowed before a Cycle Count
Alarm condition is activated.
The default setting for the Cycle Count Limit is 50000 cycles.
3.
Temperature
The
Temperature High Limit
(HI_LIM_BOARD_TEMP) parameter
should be set to alarm when the temperature sensor reads above a
user specified value and the
Temperature Low Limit
(LO_LIM_BOARD_TEMP) will be set to alarm when the temperature
sensor reads below a user specified value.
The default setting for the Temperature High Limit is 50°C. The
default setting for the Temperature Low Limit is -10°C.
(b) Functional Settings
1.
Single-Dual Action
The ACTION_ELEMENT parameter is used to determine what
direction the actuator goes when energized. The 2 settings of the
ACTION_ELEMENT parameter are Direct and Reverse Acting.
“Reverse Acting” is to be used when the energized state is to close
the valve.
The Default setting for Action Element is DIRECT Action.
2.
Channel 13
Channel 13 is a user configurable input channel. The user can
define the functionality of a DI block associated with Channel 13
by selecting the appropriate bits in the CHAN_13_MASK parameter.
One of several alarms can be used to trigger a DI including cycle
count, over stroke timer, temperature or any combination of these.
The unit is shipped with Channel 13 set up for over/under tempera-
ture indication.
The following is a list of bit selections for Channel 13. Simply select
the appropriate bit to activate the desired functionality.
0x00, No Selection
0x01, Cycle Count
0x02, Time to Open
0x04, Time to Close
0x08, Board Temp Hi
0x10, Board Temp Lo
(c) Calibration Switch Functionality
The SCM-FF is shipped in a mode where the calibration switch is
active. A 9 to 32 VDC power supply can be used to activate and
deactivate the device, to open and close the valve, and set the target.
In order to enable the calibration switch in a safe manner, three
conditions are required to be true simultaneously. These are:
1.
CAL_SW_ARM parameter is TRUE/Armed. The
operator may consider this like a calibration switch
lock out parameter when disabled.
2.
The calibration switch on the SCM-FF must be in
the FF position. This allows smooth transition to
the manual control condition.
3.
Transducer block must be in the Out Of Service (OOS)
mode. This sets all of the connected output parameters to
a BAD status, allowing upstream controllers to recognize
the device is not controlled by the control scheme.
The CAL_SW_STATE parameter transitions to Enabled when all
three conditions have been met simultaneously. This parameter will
transition to the disabled state when the Transducer Block is placed
into service or the CAL_SW_ARM is set to disabled.
NOTE
When the transducer mode changes from OOS mode,
the valve will go to the FF position calculated at the time
regardless of the current position of the valve or the
Calibration switch.
Transducer Special Diagnostic Features
During installation, a special diagnostic parameter called
ACTIVE _BLOCK_ALMS can be used to alert the user of configura-
tion errors specific to the device. This block is used to conveniently
identify some of the issues that may arise with installing the SCM-FF.
The values returned are explained below:
a.
None Active - No active block alarms are active.
b.
Invalid Mode - The computed actual mode for the block is
not supported the block’s actual mode will go to out of
service.
c.
Mode Error - The mode calculator detected an error.
d.
Both Contacts Closed - Both contacts are closed.
e.
Conflicting Channels Assigned - Conflicting output
channels have been assigned.
(See DO Block Section
for a description of the correct configuration of output
channels).
f.
Open without Close - An ‘Open’ output channel has been
assigned without a ‘Close’ channel.
g.
No Output Channels - No output channels have been
assigned.
h.
Out Of Service - Transducer block is out of service.
i.
Invalid Input - The target position is not valid for the
current device configuration. Check the target setting
to insure that it is in the correct position.
Stroke Valve Method
The method allows the user to simply invoke the method, receive
appropriate warnings of using an operating process and then allow
the user to repeatedly open/close the valve while viewing the actual
feedback from the valve on the screen. This method automatically
makes the necessary transducer block mode changes to enter the
method and automatically reinstate the previous transducer block
mode when the method exits. This prevents the user from uninten-
tionally rendering the device unusable from the host control system.
Содержание DXP-FF
Страница 11: ...www topworx com 11 TM DO DO DO DO DO DO DO ...
Страница 12: ...D Series with FF Option Installation Operation Maintenance 502 969 8000 12 ...
Страница 25: ...www topworx com 25 TM Complete Transducer Parameter Listing cont ...
Страница 37: ...www topworx com 37 TM Warranty ...
Страница 38: ...D Series with FF Option Installation Operation Maintenance 502 969 8000 38 NOTES ...
Страница 39: ...www topworx com 39 TM NOTES ...