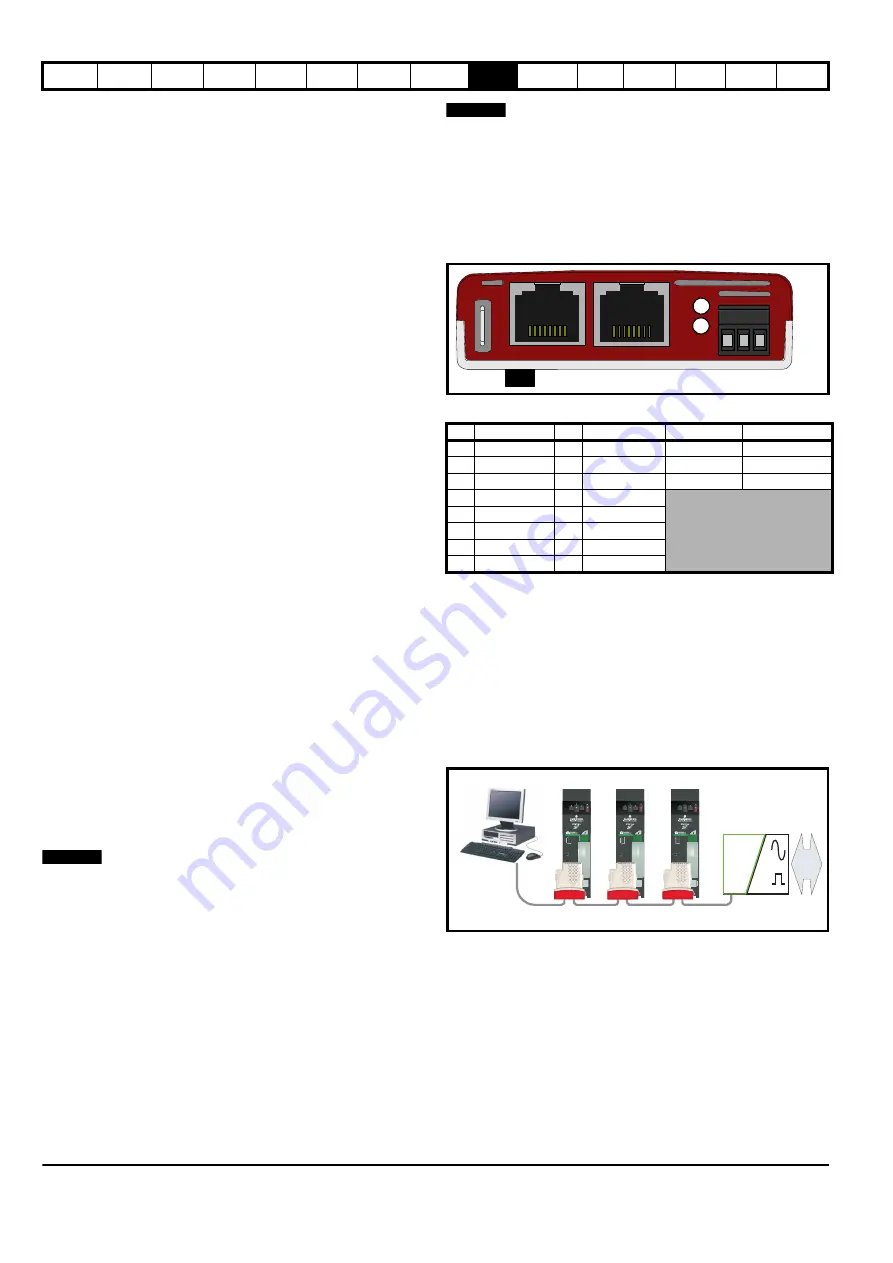
72
Digitax ST User Guide
Issue: 5
9 EtherCAT interface
9.1 Features
•
Standard RJ45 with support for shielded twisted pair, half-duplex /
full-duplex and 10Mbs / 100Mbs connectivity
•
Dual 100 Mbps EtherCAT interfaces for use in line topologies i.e.
daisy chaining
•
Control loop synchronization
•
Control cycle times down to 250 µs
•
Configured Station Alias
•
CANopen over EtherCAT (CoE) which includes:
Support of CANopen DSP-402 (Device Profile for Drives and
Motion)
•
Cyclic sync position mode
•
Interpolated position mode
•
Velocity mode
•
Profile torque mode
•
Homing mode
•
Two transmit and two receive PDOs
•
SDO access to all profile objects and drive parameters
•
Two digital inputs available for use in homing mode
•
EoE (Ethernet over EtherCAT)
9.2
What is EtherCAT?
EtherCAT is an open high performance Ethernet-based fieldbus system
that overcomes the system limitations of other Ethernet solutions. The
Ethernet packet is no longer received, then interpreted and copied as
process data at every connection; instead the Ethernet frame is
processed on the fly. The development goal of EtherCAT was to apply
Ethernet to automation applications that require short data update times
(also called cycle times) with low communication jitter (for
synchronization purposes) and low hardware costs. Typical application
fields for EtherCAT are machine controls (e.g. semiconductor tools,
metal forming, packaging, injection moulding, assembly systems,
printing machines, robotics and many others).
9.3 EtherCAT interface information
9.3.1 Bus media
The EtherCAT interface incorporates two 100 BASE-TX RJ45 interfaces.
9.3.2 Cabling considerations
To ensure long-term reliability it is recommended that any cables used to
connect a system together be tested using a suitable Ethernet cable
tester, this is of particular importance when cables are constructed on
site.
9.3.3 Cable
Cables should be shielded and as a minimum, meet TIA Cat 5e
requirements.
Cabling issues are the single biggest cause of network downtime.
Ensure cabling is correctly routed, wiring is correct, connectors are
correctly installed and any switches or routers used are rated for
industrial use. Office grade Ethernet equipment does not generally offer
the same degree of noise immunity as equipment intended for industrial
use.
9.3.4 Maximum network length
The main restriction imposed on Ethernet cabling is the length of a single
segment of cable. The EtherCAT interface has two 100BASE-TX
Ethernet ports, which support segment lengths of up to 100 m. This
means that the maximum cable length which can be used between one
EtherCAT interface port and another 100BASE-TX port is 100 m
however it is not recommended that the full 100 m cable length is used.
The total network length is not restricted by the Ethernet standard but
depends on the number of devices on the network and the transmission
media (copper, fiber optic, etc.).
The EtherCAT system designer must consider the impact that the
selected network structure will have on performance.
9.4 EtherCAT interface terminal
descriptions
The EtherCAT interface has two RJ45 Ethernet ports for the EtherCAT
network. There are also two digital inputs available for use in Homing
Mode.
Figure 9-1 EtherCAT connection
Table 9-1 EtherCAT terminal descriptions
9.5 Module grounding
EtherCAT interface is supplied with a grounding tag on the module that
should be connected to the closest possible grounding point using the
minimum length of cable. This will greatly improve the noise immunity of
the module.
9.6 Network topology
Emerson Industrial Automation
recommend implementing daisy chaining
on EtherCAT networks (see Figure 9-2). Other Ethernet network
topologies can be used but care must be taken to ensure that the system
still operates within the constraints specified by the designer.
Figure 9-2 EtherCAT interface daisy chain network topology
9.7 Minimum node-to-node cable length
There is no minimum length of cable recommended in the Ethernet
standards. To avoid possible problems it is recommended that you allow
sufficient cable length to ensure good bend radii on cables and avoid
unnecessary strain on connectors.
9.8 Quick start guide
This section is intended to provide a generic guide for setting up
EtherCAT interface with a master/controller PLC. It will cover the basic
steps required to get cyclic data communicating using the CANopen
over EtherCAT (CoE) protocol on the EtherCAT interface.
NOTE
Pin
A - IN
Pin
B - OUT
Digital Inputs
Function
1
Tr
1
Tr
1
0V Common
2
Transmit -
2
Transmit -
2
Digital input 0
3
R
3
R
3
Digital input 1
4
Not used
4
Not used
5
Not used
5
Not used
6
Receive -
6
Receive -
7
Not used
7
Not used
8
Not used
8
Not used
NOTE
1 2 3
A
B
A
B
Master / PLC
Digitax ST
SM
-
EtherCAT
SM
-
EtherCAT
Distributed I/O
Digitax ST
Digitax ST
Digitax ST
SM
-
EtherCAT
Содержание Digitax ST
Страница 1: ...User Guide AC variable speed drive for servo motors Part Number 0475 0001 05 Issue 5 ...
Страница 209: ......
Страница 210: ...0475 0001 05 ...