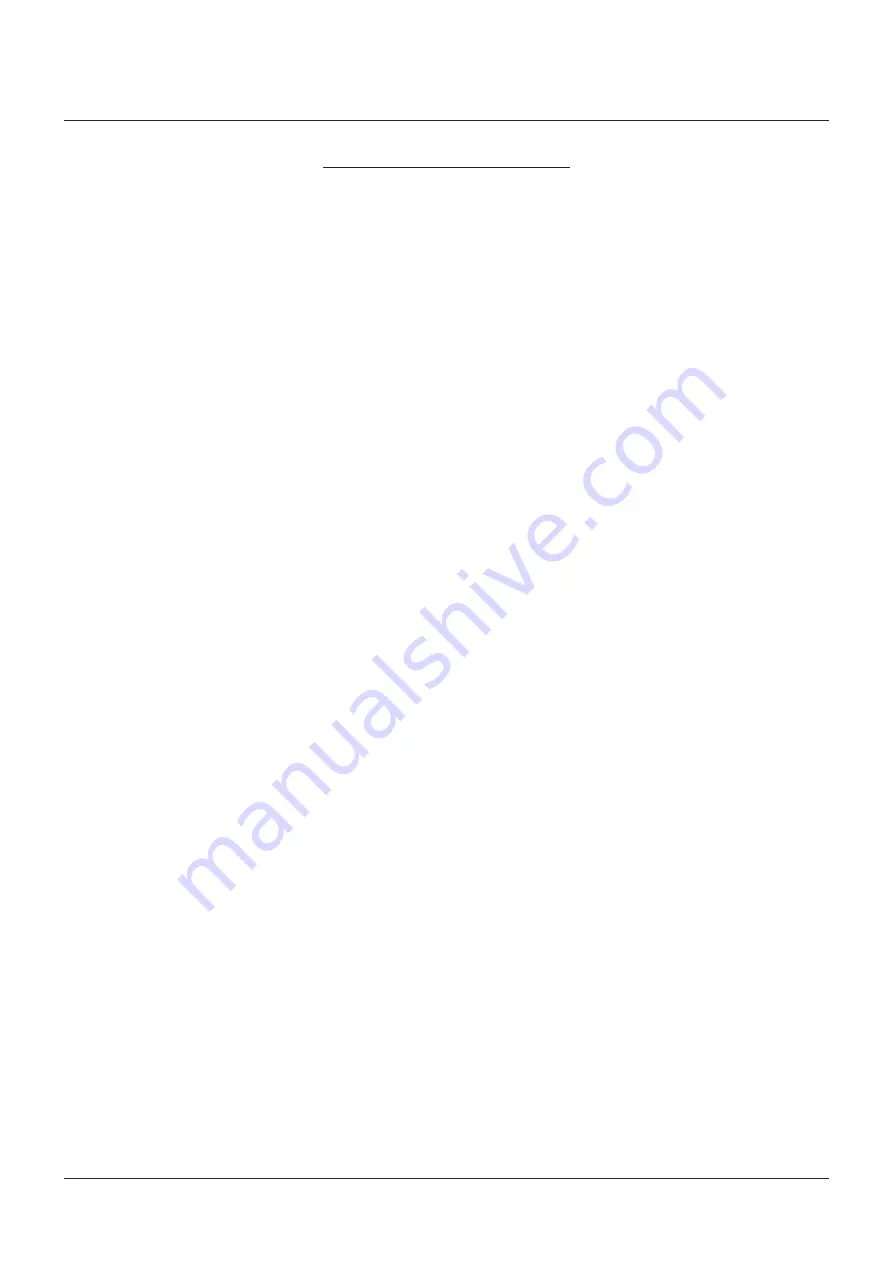
5
5 INSTALLATION
Inlet piping
Many safety valves are damaged when first
placed in service because of failure to clean
the connections properly before installation.
The safety valve inlet, the vessel and the line
on which the safety valve is mounted must be
cleaned thoroughly of all foreign matter.
Safety valves should be mounted in a vertical
position, directly on the pressure vessel.
The ASME boiler and pressure vessel code limits
the distance between the safety valve inlet and
the boiler to the length of a standard tee fitting.
The nozzle should have a well-rounded
approach that provides smooth, unobstructed
flow between the vessel and the safety valve.
A safety valve should never be installed on a
fitting having an inside diameter smaller than
the inlet connection of the valve.
Such restriction of flow can cause faulty
valve operation.
Inlet piping (nozzles) must be designed to
withstand the total resultant forces due to
the safety valve discharging at the maximum
accumulated pressure and the expected
piping loads. The precise nature of the loading
and the resulting stresses will depend on
the configuration of the safety valve and the
discharge piping. Determination of outlet
reaction forces is the responsibility of the
designer of the vessel and/or piping.
Outlet piping
Discharge piping should be simple and
direct. Back pressures built up by discharge
flow affect the operation of safety valves.
Where possible, a short vertical pipe connected
through a long radius elbow discharging
directly into the atmosphere is the most
desirable type of outlet piping.
Discharge piping should not impose any loading
on the safety valve. Excessive discharge piping
loads may cause seat leakage or faulty valve
operation. The inside diameter of the discharge
pipe must never be less than that of the safety
valve outlet.
Valve effluent must discharge to a safe
disposal area.
Safety valve bodies have pipe thread openings
for drains. These should be connected to
prevent any accumulation of fluid in the valve
body. In addition, discharge piping also should
be drained to prevent any accumulation of fluid.
Care must be taken to ensure that the drains
are directed or piped to a safe disposal area.
Welding of welded inlet valve body to boiler
Welded inlet safety valve bodies should be
welded to the boiler in accordance with
applicable Code requirements. The protective
cover (Figure 3) should be left in place until
ready for the hydrostatic test of the unit.
If visual inspection is necessary, the protective
cover may be removed, but should be replaced.
CROSBY
®
STYLES HC AND HCA ISOFLEX™ SAFETY VALVES
INSTALLATION, MAINTENANCE AND ADJUSTMENT INSTRUCTIONS
NOTES
Note 1 to Figure 3
Delivered with the body and packaged in small
bag are the following:
• One O-ring (for hydrostatic test)
• One backup ring (for hydrostatic test)
• One hydrostatic test plug pin
Note 2 to Figure 4
Delivered with the superstructure and
packaged in a small box are the following:
• Valve nozzle ring*
• Valve nozzle ring set screw*
• Valve guide ring set screw*
• Seal wires
* Marked with valve identification number.
NOTE
When the above parts are removed from their boxes,
be sure that the identification of parts to valve number
is maintained and that the parts are stored to facilitate
later recovery for assembly.
Factory preparation of welded inlet valves
for shipment
All Crosby Style HC and HCA welded inlet safety
valves are equipped with hydrostatic test plugs
and shipped in two parts: valve body and valve
superstructure. This makes handling easier for
installation welding (see Figures 3 and 4).
The welded inlet Style HC and HCA safety
valves are specially prepared for shipment
from the factory.
After the safety valve is tested as a complete
assembly for set pressure and tightness, the
spring set compression is held by spacer
blocks under the bottom spring washer as
illustrated in Figure 4.
The safety valve superstructure is then
removed from the valve body. The two portions
are boxed and shipped separately. Each portion,
ready for shipment, is illustrated in Figures 3
and 4.
Figure 3 shows the safety valve body as shipped
to the installation site. It is tagged as follows:
• Install and/or weld in place as required
• Prepare for hydrostatic test. See instruction
Hydrostatic plug in place
• Install O-ring and backup ring prior to
hydrostatic test.
Figure 4 shows the safety valve superstructure
as shipped to the installation site. It is boxed
separately from the valve body and is tagged
as follows:
• Hold for assembly after hydrostatic test.