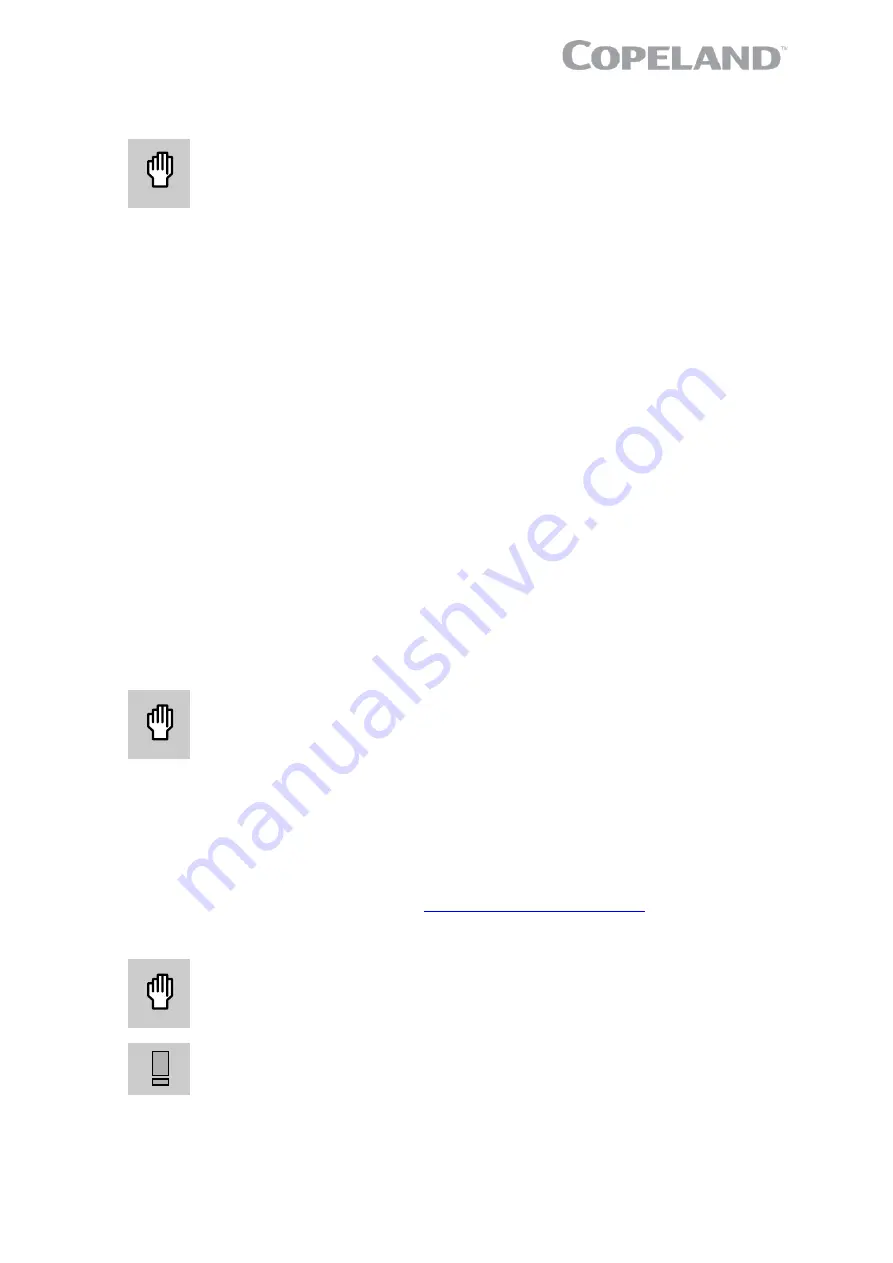
AGL_Ref_ST_ZO_E_Rev00
13
3.4 Pressure safety controls
3.4.1 Pressure relief valves
CAUTION
High pressure! System leak!
In the event that a pressure relief valve
activates repeatedly, check and replace it in order to avoid a permanent leak.
Always check system for CO
2
loss after activation of the pressure relief valve.
Pressure relief valves shall be placed on both the suction and discharge sides of the compressor.
The pressure relief valve does not replace pressure switches or additional safety valves in the
system.
▪
High-pressure side (HP):
60 bar
▪
Low-pressure side (LP):
45 bar
Usually after a blow-off, pressure relief valves are no longer perfectly tight. It is therefore
recommended to control (replace) the pressure relief valves after any blow-off.
3.4.2 High-pressure protection
Applicable regulations and standards, for example EN 378-2, shall be followed to apply appropriate
control and ensure that the pressure never exceeds the maximum limit.
High-pressure protection is required to stop the compressor operating outside the allowable pressure
limits. The high-pressure control must be installed correctly, which means that no service valve is
allowed between the compressor and the pressure protection.
The high-pressure cut-out setting shall be determined according to the applicable standard, the type
of system, the refrigerant and the maximum allowable pressure PS.
The high-pressure limiter has to be connected to the drive. For electrical specification please check
the drive user manual. Normally the high-pressure limiter must be closed. If the limiter is open, the
drive will not operate.
NOTE: For detailed specifications and instructions to connect the high-pressure limiter to the
drive, please refer to the EVM/EVH User Manual.
3.4.3 Low-pressure protection
CAUTION
Operation outside the application envelope! Compressor breakdown!
A
low-pressure protection shall be fitted in the suction line to stop the
compressor when it operates outside the envelope limits.
Applicable regulations and standards shall be followed to apply appropriate control and ensure that
the pressure is always above the required minimum limit.
Low-pressure protection is required to stop the compressor operating outside the allowable envelope
limits. The low-pressure control must be installed correctly into the suction line, which means that no
service valve is allowed between the compressor and the pressure protection.
The minimum cut-out setting shall be determined according to the refrigerant and the allowed
operation envelope
– see Select software at
3.5 Crankcase heater
CAUTION
Overheating and burnout! Compressor damage!
Never apply power to the
crankcase heater in free air, before the crankcase heater is installed on the
compressor or when it is not in complete contact with the compressor shell.
IMPORTANT
Oil dilution! Bearing malfunction!
Turn the crankcase heater on 12 hours
before starting the compressor.
A crankcase heater is used to prevent refrigerant from migrating into the shell during standstill
periods.
The initial start-up in the field is a very critical period for any compressor because all load-bearing
surfaces are new and require a short break-in period to carry high loads under adverse conditions.
The crankcase heater must be turned on a minimum of 12 hours prior to starting the
Содержание COPELAND ZO18AG
Страница 4: ...AGL_Ref_ST_ZO_E_Rev00 Appendix1 Tightening torques 32 DISCLAIMER 32 ...
Страница 5: ......