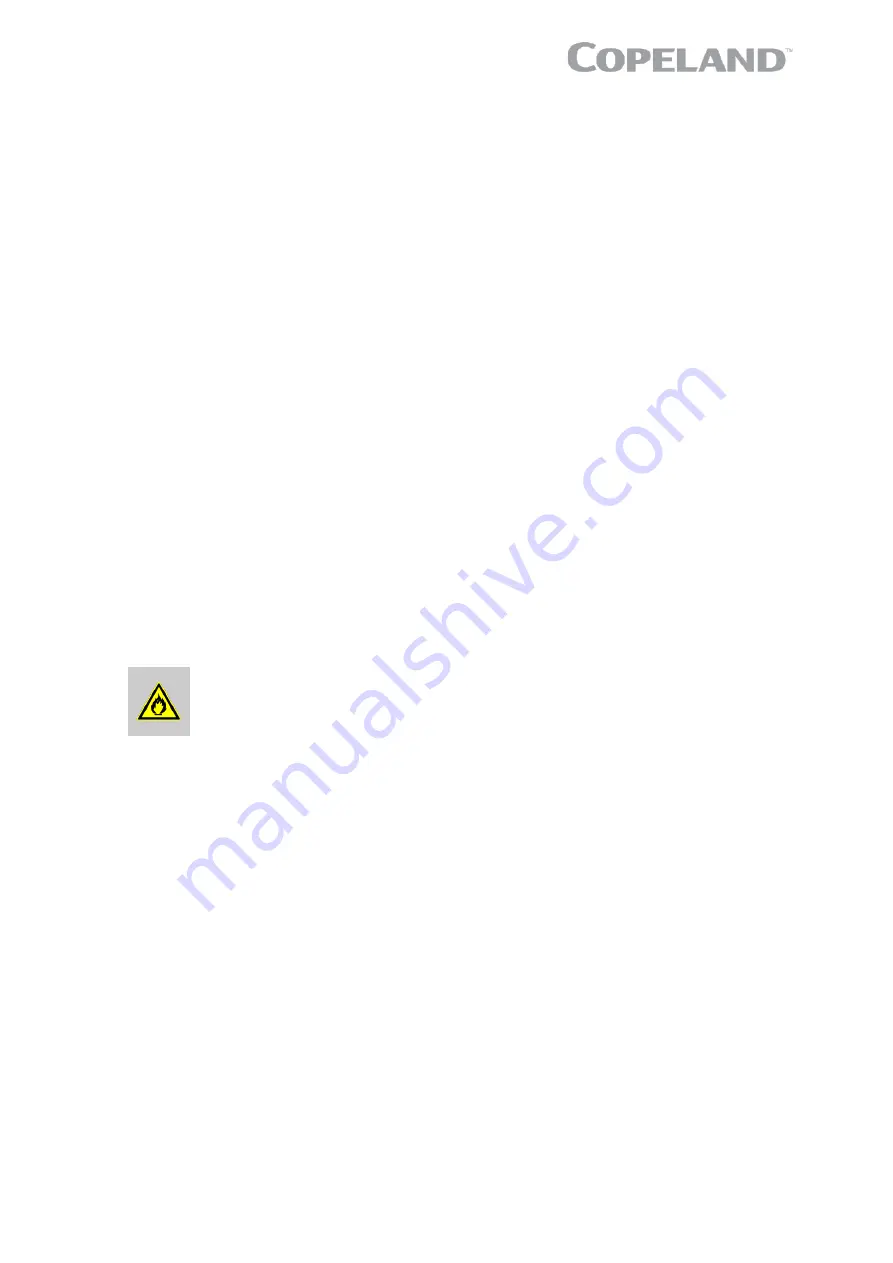
AGL_Stream_ST_A2L_A1_4M_6M_EN_Rev00
35
The compressor shall be tested for tightness before it is charged with refrigerant. For proper tightness
test, see applicable standards, eg, EN 378. All joints shall be tested with detection equipment with a
capability of 5 g/year of refrigerant or better.
6.1 Qualification of workers
Personnel working on the maintenance, repair and decommissioning of an A2L refrigerant system
shall be adequately trained. Any work procedure affecting safety shall only be executed by qualified
and trained personnel in compliance with national or other equivalent certification systems.
Examples of such work procedures are:
▪
breaking into the refrigerating circuit;
▪
opening sealed components;
▪
opening ventilated enclosures
…
6.2 Preparation and work procedure
For all A2L refrigerant systems, a work procedure shall be provided in the preparation stage. All
maintenance personnel and others working at the site shall be instructed on the nature of the work
being carried out.
If any work is to be conducted on the refrigeration systems or any associated parts, appropriate fire
extinguishing equipment shall be provided. Dry powder or CO
2
fire extinguishers are considered
appropriate. Confirm that appropriate fire extinguishing equipment is available near the work area.
Prior to starting to work on systems containing flammable refrigerants, safety checks are necessary
to ensure that the risk of ignition is minimized.
Work shall be undertaken under a controlled procedure so as to minimize the risk of a flammable
gas or vapour being present while the work is being performed.
Avoid working on systems filled with flammable refrigerant in a confined space.
6.3 Unbrazing system components
WARNING
Explosive flame! Fire hazard!
Oil-refrigerant mixtures are highly flammable.
Remove all refrigerant before opening the system. Avoid working with an
unshielded flame in a refrigerant-charged system.
Before opening up a system it is important to remove all refrigerant from both the high and low sides
of the system. If a brazing torch is then applied to the low side while the low side shell and suction
line contain pressure, the pressurized refrigerant and oil mixture could ignite when it escapes and
contacts the brazing flame. To prevent this occurrence, it is important to check both the high and low
sides with manifold gauges before unbrazing. Instructions should be provided in appropriate product
literature and assembly (line repair) areas. If compressor removal is required, the compressor should
be cut out of system rather than unbrazed.
6.4 Disassembling system components
When disassembling system components please follow the main steps described hereunder:
1.
For A1 refrigerant systems (R448A, R449A, R407A, R407F, R404A, R407C, R513A, R450A and
R134a
), recover refrigerant and evacuate system using a recovery unit and vacuum pump. All
the refrigerant shall be recovered to avoid significant release.
2.
For A2L refrigerant systems (R454C, R455A and R454A), recover refrigerant and evacuate
system using an A2L-dedicated recovery unit and vacuum pump. Ensure that the outlet of the
vacuum pump is not close to any potential ignition source and that ventilation is available.
3.
Flush system with inert gas (dry nitrogen). Compressed air or oxygen shall not be used for
purging refrigerant systems.
4.
For A2L refrigerant systems, the procedure of evacuation and flushing with oxygen-free nitrogen
may need to be repeated until no refrigerant is present in the system. When the final oxygen-
free nitrogen charge is used, the system shall be vented down to atmospheric pressure to
enable work to take place.
5.
Disassemble components with a cutting tool.