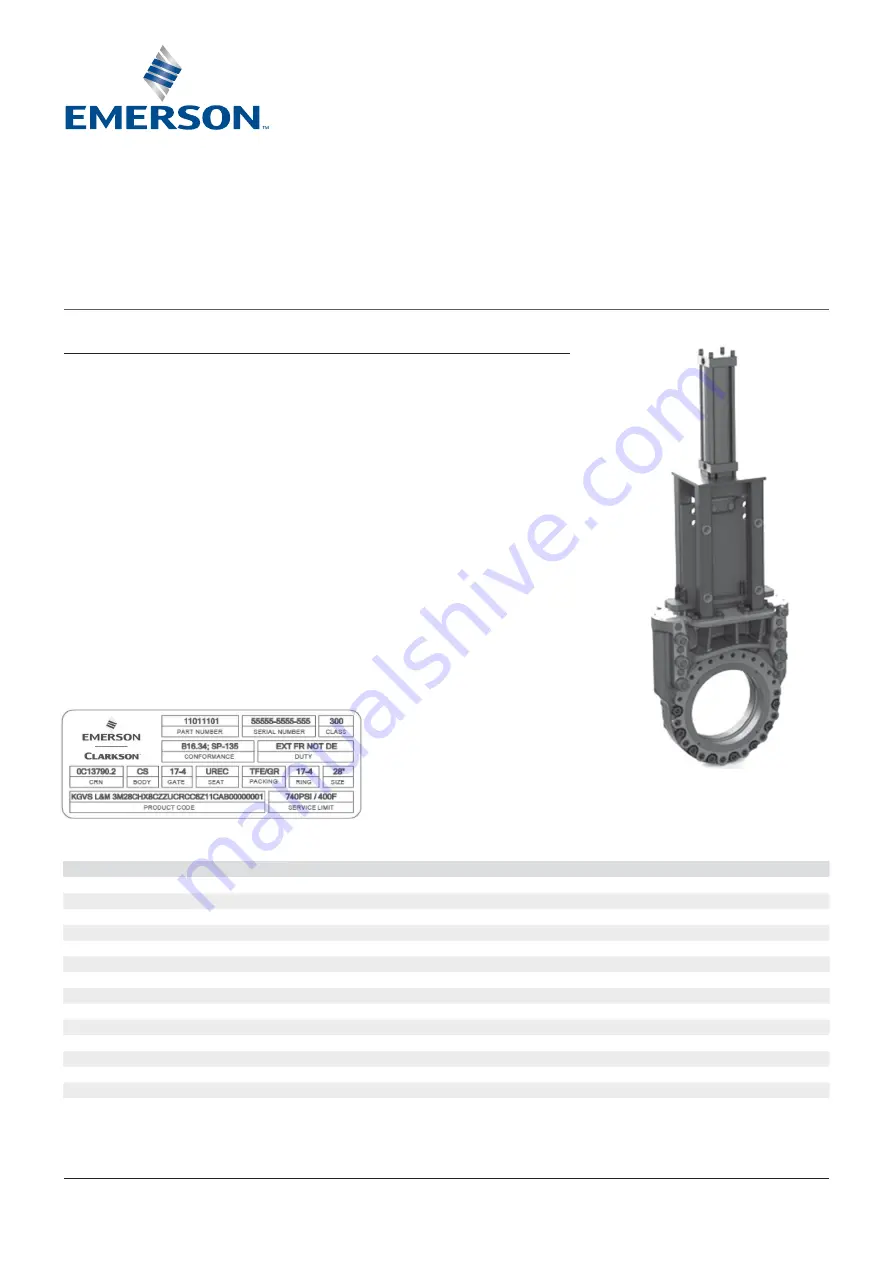
CLARKSON
KNIFE GATE VALVE MODEL ZP3OO
INSTALLATION AND MAINTENANCE INSTRUCTIONS
Before installation these instructions must be fully read and understood
GENERAL INFORMATION
LABEL CONTENTS
Item
Description
Example
Product code
Manufacturer’s model/code
KGVS Clarkson 3M28CHX8CZZUCRCC6Z11CAB00000001
Part number
Manufacturer’s pn
11011101
Serial number
Manufacturer’s sn
55555-5555-555
Size
NPS valve size
28
Class
Pressure rating per conforming standard
300
Duty
Type of service depending on valve configuration (ext or int mounted flow ring will change duty) EXT FR NOT DE or INT FR DE
Ring material
Compliance standard for flow ring material
17-4
Service limit
Limits in pressure and temperature operation
740psi/100F
Conformance
Standard used for design and manufacture
ASME B16.34, MSS SP-135
Crn
Canadian registration number
0C13790.2
Body material
Compliance standard for body material
WCB/LCB
Gate material
Compliance standard for gate material
17-4
Seat material
Seat material
URET
Packing material Packing material
TPE/GR
COMPLIANCE LABEL
3. Mating line flanges must be properly
aligned. Slip-on or weld flanges can be used.
Never try to make up for misaligned pipe
flanges by the line bolting.
4. Flange fasteners should be tightened in a
uniform manner using a cross-pattern to
prevent distortion of the valve.
5. Pipe supports and/or expansion joints should
be used to minimize pipe loads on valves.
ZP300 valves are suitable for use in either
vertical or horizontal lines. If installation is
other than vertical, additional support will be
required for cylinder actuated valves.
© 2017 Emerson. All Rights Reserved.
Emerson.com/FinalControl
VCTDS-03757-EN 16/12
The Clarkson ZP300 knife gate valve is
designed to meet extremely rugged and
challenging requirements of expansible fluid
applications in the oil sands processes.
Please take note of specific installation tags
provided with each ZP300 series valve.
1. Compliance to ASME B16.34 Class 300,
Valves-Flanged, Threaded, and Welding End
and MSS SP 135 (Long Face-to-Face).
2. Bi-directional valve, no special concerns
in relation to direction of flow are required
when installing the valve.