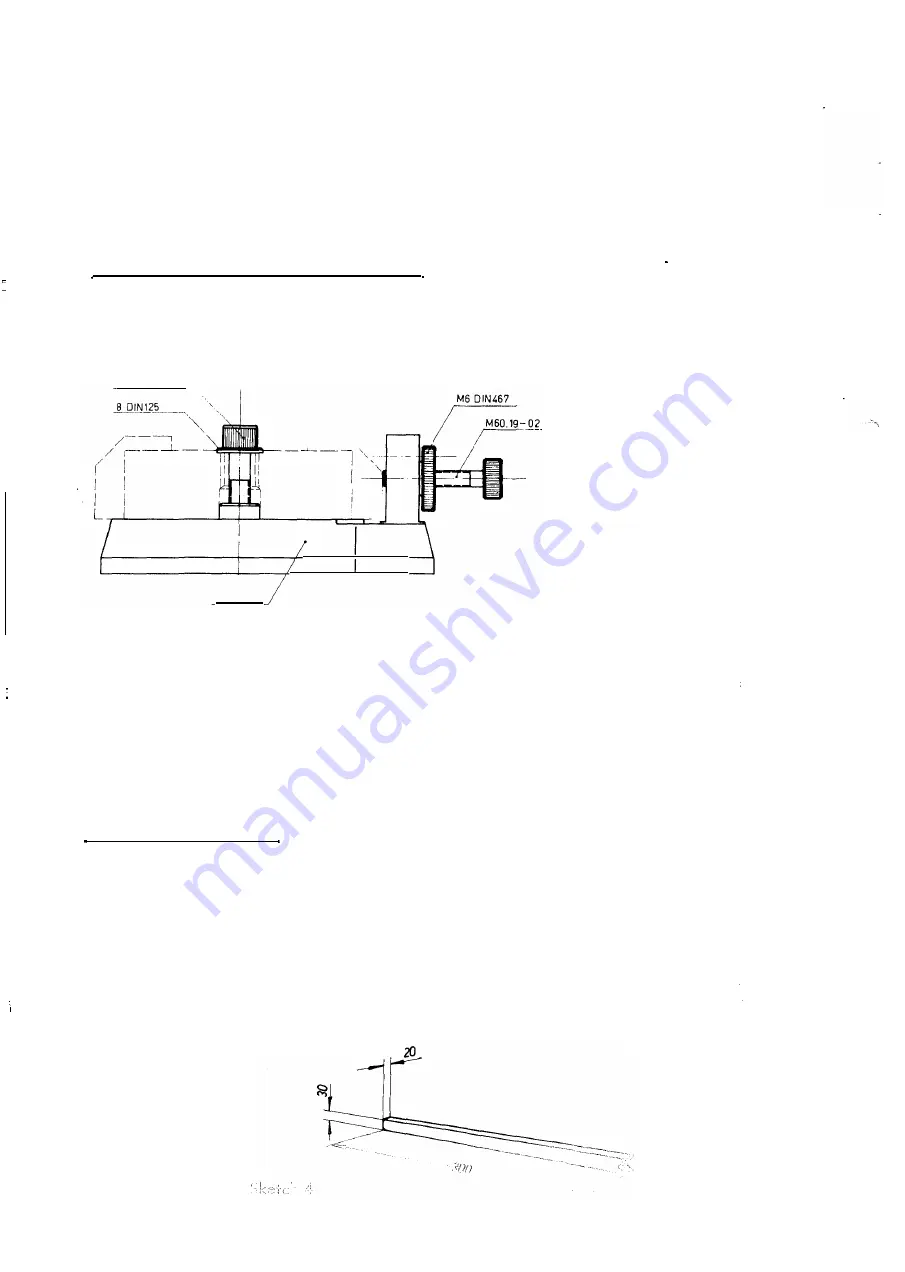
- 22 -
5. Return the batten to its initial position.
6. When the second cutter carries the batten the same distance from the initial position A to the
final position E, both cutters will be correctly located. If necessary, the position of the second
cutter will have to be corrected.
7. When both cutters have been correctly positioned, as indicated by the check, tighten the
socket-head bolts up firmly.
8. Form cutters are set up in the same way as straight cutters.
GAUGE FOR SETTING CUTTER BLOCK:
A considerably simpler method of setting the cutter block than that described above is to use the
setting gauge
M
60.19 for adjusting the flat cutters in the block. This is effected as follows:
The flat cutters are inserted in the block and are I ightly held by screwing up the socket-head bolts
Sketch 3
MB x35 D IN9'2
-,,
:--"
M60 19-01
I
_J
very gently.
Now place the cutter block on the
setting gauge with one blade
pointing towards the brass knurled
screw
M
60. 19-02 (see sketch).
The cutter block is held in this
position by tightening up the socket
head bolt M 8 x 35 DIN 912. The
knurled half nut M 6 DIN 467 is
loosened, and the knurled screw
turned back until the whole cutting
edge of the blade projects beyond
the periphery of the cutter block.
This position of the screw is fixed
by tightening up the knurled nut
M 6 DIN 467. Then hold the cutter
blade in contact with the knurled screw with one hand, and with the other secure the blade in the
cutter block (with the aid of the Allen key). The socket-head bolt M 8 x 35 is then unscrewed, and
the cutter block turned through 180
°
, so that the second cutter points towards the knurled screw.
The second cutter is then pushed out until it is in contact with the knurled screw, which remains
fixed, and secure. Both cutters are now ad justed to the same setting, and the cutter block can be
removed from the setting gauge.
To adjust moulding cutters PM 9 and PM 11 the knurled screw is inserted in the upper hold in the
setting gauge. The other moulding cutters are dealt with in the same way as flat cutters.
SAFETY PRECAUTIONS:
l . Always use sharp cutters.
2. Screw the cutter block on firmly.
3. Make sure the cutters are always correctly positioned and firmly clamped.
4. Set the guard so that it just contacts the top of the components.
5. Loose knots must be removed from the wood before it is machined.
6. Do not use too deep a cut or too fast a feed.
7. The components must be pressed firmly against the table and against the fence whil� they are
being machined.
8. Small components should be fed past the cutters with the aid of a push rod (see Sketch 4) made
up locally, and not directly by hand.
wooden push rod
i1